Product Description
Common installation dimensions in the market, international standard flange.
Reserved multiple screw holes.
Can implement multiple communication protocols.
Optimized waterproof design, durable, long service life, anti-interference.
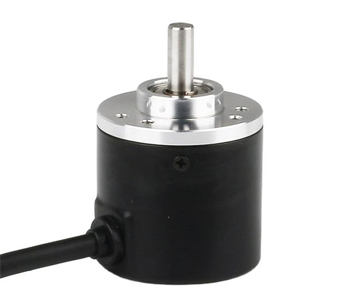

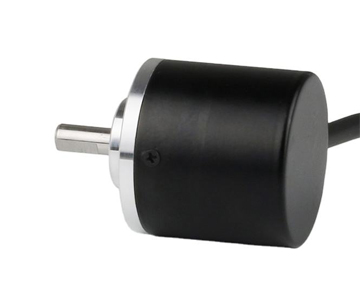
Product parameters
Basic parameters
Angle measurement range | 0~360° | Number of digits | 8-15 bits | ||||
---|---|---|---|---|---|---|---|
Wiring Instructions | |||||||
Color Protocol | Red | Black | Blue | Green | Yellow | Gray | Shielded |
RS485/ | VCC | GND | A | B | G | ||
Modbus | |||||||
RS422 | VCC | GND | TXD+ | TXD- | RXD+ | RXD- | G |
SSI | VCC | GND | DATA+ | DATA- | CLOCK+ | CLOCK- | G |
CAN | VCC | CANH | CANL | G |
Electrical parameters
Working voltage | DC5V/10-30V | Current consumption | 0.3A |
---|---|---|---|
Output interface | RS485/422/CAN/modbus/SSI | Output code | Natural Binary/Gray Code |
Output mode | Bus mode, timed transmission mode, pulse trigger mode, clear mode | ||
Serial protocol (optional) | 115200bps(1KHz)/57600(500Hz)/38400bps(300Hz)/ 19200bps(200Hz)/9600bps (100Hz) CAN baud rate: 250K/500K/1M SSI: Communication clock: 1M/2M Data update: 10K | ||
Note: The power supply voltage and line sequence correspond to the device connection to ensure the normal operation of the encoder. Do not overlap the signal line and the power line when the power is on. When the working voltage is DC5V±5%: ① The power line length shall not exceed 2 meters ② The power supply current limit shall not be less than 1A ③ The power supply ripple is less than or equal to ±50mV. When the working voltage is 10-30V: ① The power supply current limit shall not be less than 0.5A ② The power supply ripple is less than or equal to ±50mV |
Usage Environment
Vibration | 3g | Working temperature | -40°C~+65°C |
Shock | 20g | Storage temperature | -50°C~+70°C |
Mechanical parameters
Maximum allowed mechanical revolutions | Starting torque (25℃) | Maximum shaft load | Moment of inertia | Allowable angular acceleration | Weight | |
---|---|---|---|---|---|---|
600r/min | 5x10-3N.M | Radial | Axial | 4x10-8N.M.S | 1x104rad/s | 150g |
200N | 10N |
Product Display
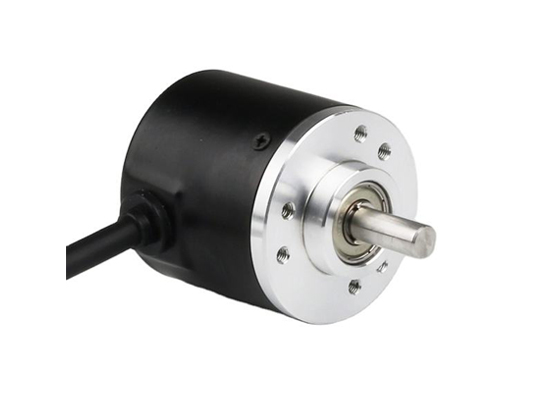
High-precision positioning
Magnetic-free absolute encoders can provide high-precision position information. They accurately determine the rotation angle or linear displacement through non-magnetic measurement principles, such as photoelectric or capacitive methods. For example, in some high-precision photoelectric non-magnetic absolute encoders, the resolution can reach a very high level and can distinguish extremely small angle changes, which is very important for robots to accurately control joint movements. When robots perform delicate operations such as assembly and welding, they need to know the position of each joint accurately. Magnetic-free absolute encoders can meet this high-precision positioning needs.
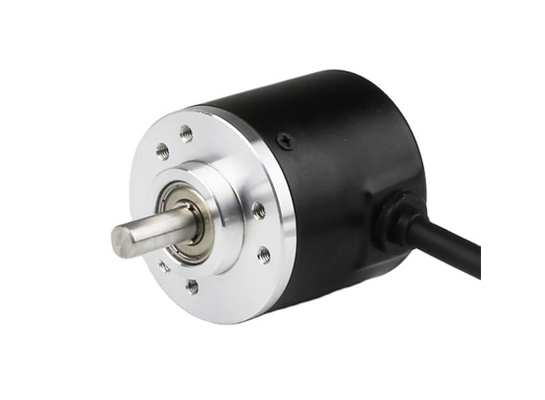
Strong anti-interference ability
Because it does not rely on magnetic fields for measurement, non-magnetic absolute encoders are insensitive to external magnetic field interference. In industrial environments, there may be various electromagnetic interference sources around the robot, such as magnetic fields generated by motors, transformers and other equipment. Magnetic encoders may experience signal distortion or increased errors in such environments, while non-magnetic absolute encoders can effectively avoid these problems and ensure stable and accurate position feedback signals, thereby ensuring the normal operation and operating accuracy of the robot.
Size & Interface
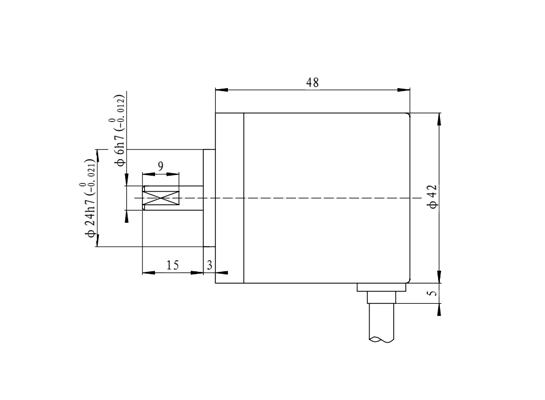
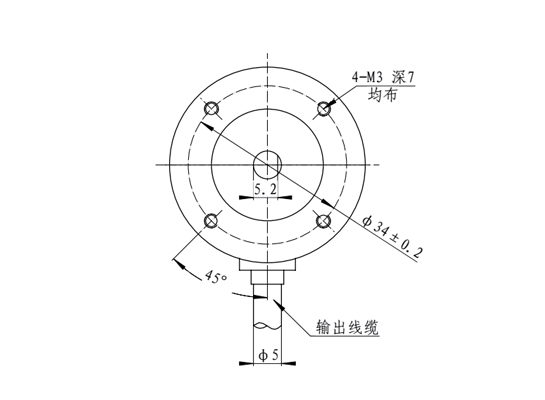
Application Cases
- Industrial robots: Non-magnetic absolute encoders provide high-precision position feedback for the joints of industrial robots to ensure their precise movement and operation.
- CNC machine tools: Applied to the axis motion control of CNC machine tools to achieve precise positioning of tools and precision machining of complex parts.
- Warehousing and logistics automation: In the stacking machines and conveying equipment of automated warehouses, the storage and handling positions of goods are precisely controlled.
- Medical equipment: In equipment such as medical robots and CT scanners, it helps achieve precise positioning and motion control, and improves the accuracy of medical diagnosis and treatment.
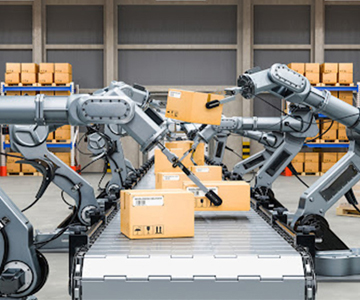
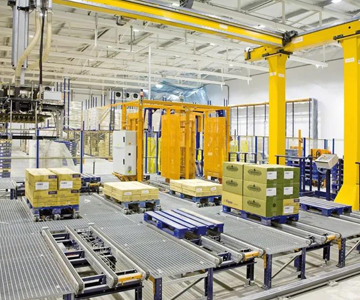
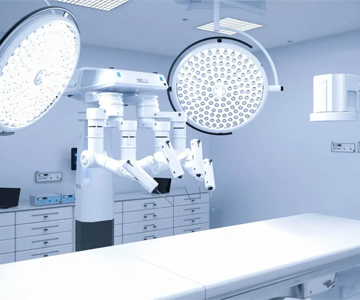