Product Description
The coreless mini DC motor is a miniaturized form of DC motor. Unlike traditional core motors, it does not have an obvious iron core as the main part of the magnetic circuit. Its main structure includes a stator and a rotor. The stator is usually a permanent magnet and is used to generate a magnetic field. The material of permanent magnet can be NdFeb and other high-performance magnetic materials, which can provide a strong magnetic field and magnetic stability. The rotor is mainly composed of windings, which are generally wound with enamelled wire. These windings generate a magnetic field when the current passes through them, which interacts with the stator's magnetic field and drives the motor to rotate.
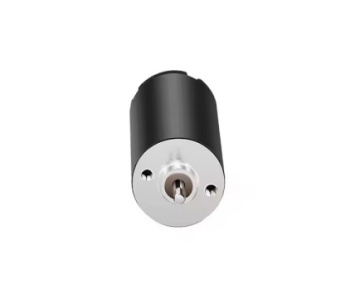
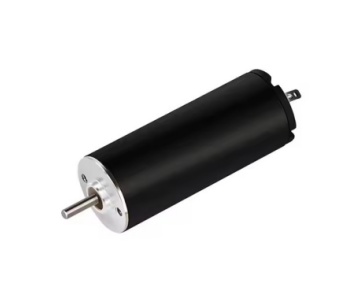
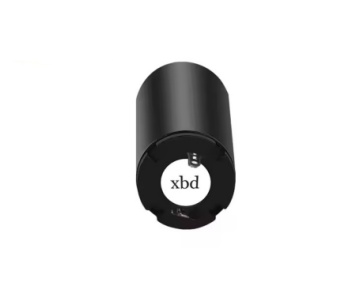
Product parameters
Motor parameter | Motor type | ||||
---|---|---|---|---|---|
name | unit | XBD12300 6135HJ- 15070 | XBD12301 2114HJ- 15070 | XBD12301 5135HJ- 15070 | XBD12302 4150HJ- 15070 |
Rated voltage | V/DC | 6 | 12 | 15 | 24 |
Rated speed | rpm | 10800 | 9120 | 10800 | 12000 |
Rated current | A | 0.4 | 0.2 | 0.2 | 0.2 |
Rated torque | mi | 1.4 | 1.5 | 1.8 | 2.7 |
No-load speed | rpm | 13500 | 11400 | 13500 | 15000 |
No-load current | mA | 22 | 16 | 15 | 8 |
Maximum efficiency | % | 78.5 | 77.7 | 79.9 | 80 |
Rotational speed | rpm | 12150 | 10203 | 12218 | 13575 |
Electric current | A | 0.2 | 0.1 | 0.1 | 0.1 |
torque | mNm | 0.7 | 0.8 | 0.9 | 1.3 |
Maximum power | W | 2.5 | 2.3 | 3.3 | 5.3 |
Rotational speed | rpm | 6750 | 5700 | 6750 | 7500 |
Electric current | A | 0.9 | 0.4 | 0.5 | 0.5 |
torque | mNm | 3.5 | 3.8 | 4.6 | 6.7 |
Locked-rotor current | A | 1.69 | 0.78 | 0.89 | 0.9 |
Locked-rotor moment | mNm | 7 | 7.6 | 9.2 | 13.4 |
Motor impedance | Ω | 3.55 | 15.38 | 16.85 | 26.67 |
Inductive reactance of motor | mH | 0.25 | 0.59 | 0.65 | 0.98 |
Torque constant | mNm/A | 4.19 | 9.91 | 10.49 | 15.11 |
Speed constant | rpm/V | 2250 | 950 | 900 | 625 |
Revolution/torque constant | rpm/mNm | 1932.1 | 1495.9 | 1462.3 | 1115.5 |
Mechanical time constant | ms | 5.7 | 4.3 | 4.5 | 3.2 |
Rotor inertia | gcm2 | 0.28 | 0.27 | 0.29 | 0.27 |
Technological Innovation
High speed and easy to control
The coreless mini DC motor can achieve higher speed. This is because without the limitation of the iron core, the moment of inertia of the rotor is small, and under the same electromagnetic drive, it can accelerate faster to a higher speed. At the same time, the speed of the motor can be easily controlled by changing the input voltage or current. This speed control characteristic makes it widely used in devices requiring precise speed regulation, such as small precision power tools or focusing devices in optical instruments.
Product Display
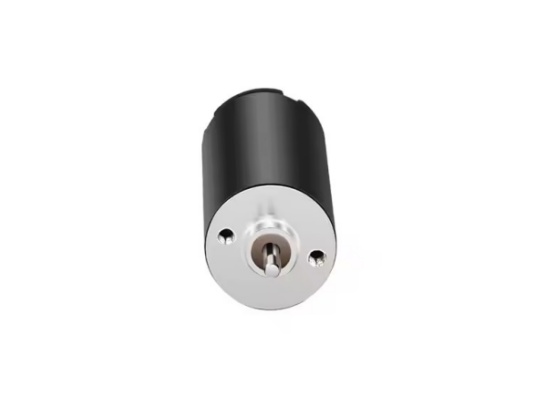
Compact and light
The size of the coreless mini DC motor is very small, which makes it a great advantage in equipment with strict space constraints. For example, in some micro-robots, small electronic toys or portable medical devices, it can be easily installed in a limited space. And its weight is also very light, will not add too much burden to the device, is conducive to the portability and flexibility of the device.
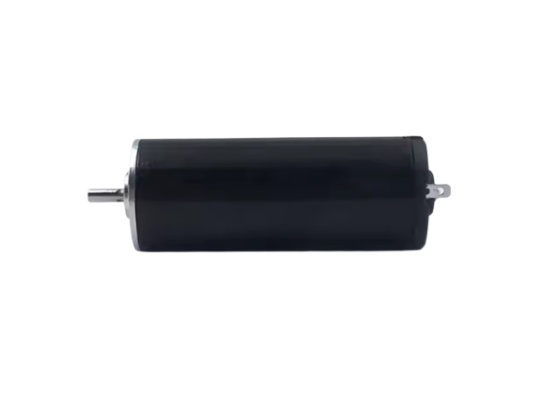
High efficiency and energy saving
Since there is no iron core, the hysteresis loss and eddy current loss of the motor are relatively small. Hysteresis loss is due to the energy loss caused by the repeated magnetization process of the iron core, and eddy current loss is due to the heat loss caused by the induced current in the iron core. Without these losses, the motor is able to more effectively convert electrical energy into mechanical energy, thereby improving the efficiency of the motor, and also reduce heat during operation, reducing energy waste.
Size & Interface
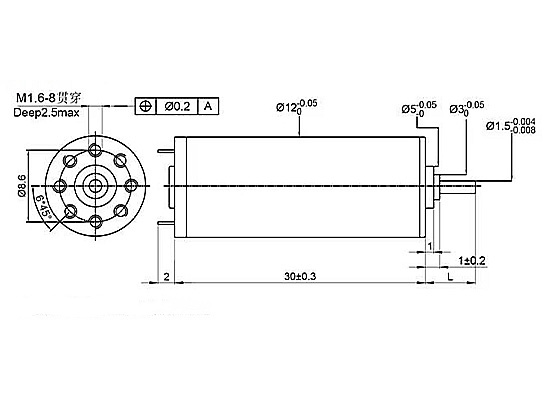
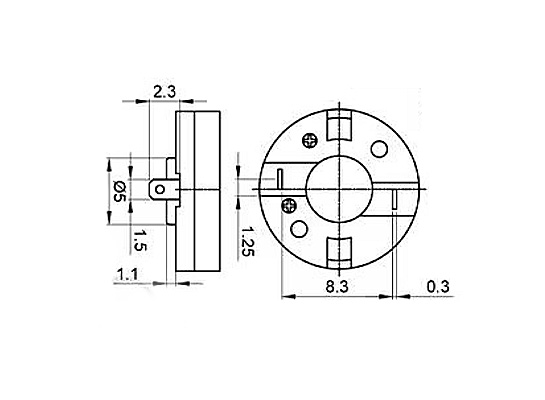
Quality Control
Assembly link control: tight seam
The assembly process of the motor is like a precise jigsaw puzzle, where every component must be fitted into place without error. Our assembly workers are professionally trained, have rich experience and a high sense of responsibility. When assembling the hollow cup rotor, ensure that its position in the stator is accurate and the clearance with the brush and commutator is just right. The tightening torque of each screw is precisely calculated and strictly controlled to prevent the overall performance of the motor from being too tight or too loose. After the assembly is completed, the appearance of the motor is also carefully checked to ensure that no parts are loose, scratched or improperly assembled.
Performance testing: Comprehensive inspection
We have a set of perfect performance testing system, for each hollow cup brush motor for comprehensive and strict inspection. In terms of electrical performance detection, the starting current, no-load current, rated power, speed and torque of the motor are measured by high-precision test equipment to ensure that these parameters are within the specified tolerance range and meet the design requirements. For the mechanical properties of the motor, we simulate the actual working environment and carry out long-term operating tests to observe the vibration, noise level and heating degree of the motor. Only motors that are fully qualified in all performance indicators will be labeled as qualified in quality and enter the market.
Durability test
In order to ensure the reliability and life of the motor, we will carry out a long time durability test on the motor. In the simulation of various actual working conditions, the motor is continuously run for hundreds of hours, during which the performance indicators of the motor are continuously monitored, such as temperature changes, vibration conditions, electrical parameter stability, etc. Only motors that pass the durability test and have no significant degradation in performance will be considered qualified products.
Quality traceability system: Tracing to the source
In order to ensure the continuous stability of quality, we have established a sound quality traceability system. Each hollow cup brush motor has a unique identity, from the procurement batch of raw materials, all aspects of the production process data to the final test report, are recorded in detail. Once a quality problem is found, it can be quickly traced back to the root of the problem, and effective corrective measures can be taken to avoid the recurrence of similar problems.
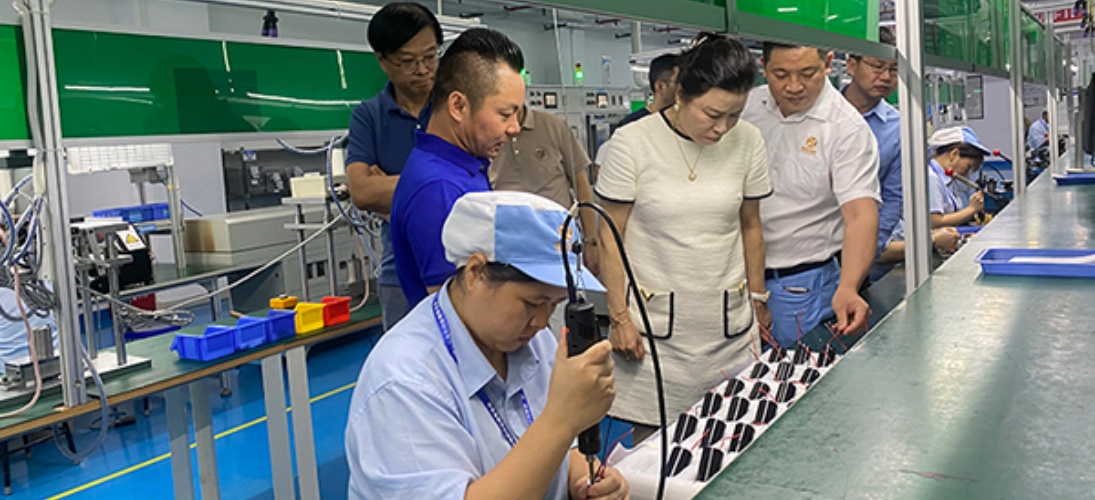
Application Cases
The application of motor in the fields of aviation model equipment, aerospace probe, high altitude camera and agricultural UAV has fully demonstrated its excellent performance and wide adaptability. They have not only promoted the technological development in these fields, but also provided solid power support for human exploration of the sky, understanding of the universe and the development of modern agriculture.
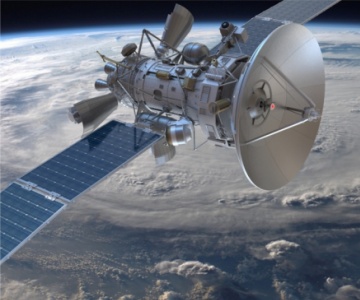
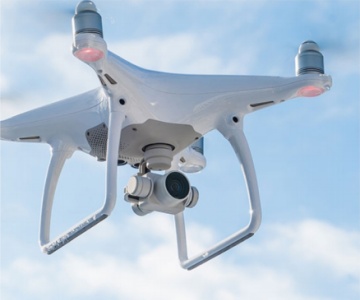
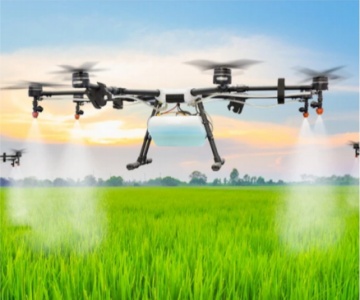
Cooperative partner

Service
Training and knowledge sharing
We not only solve problems, but also focus on supporting your team with knowledge. We can carry out training courses for your operators and maintenance personnel, covering the basic operation of the motor, daily maintenance points, common fault identification and prevention. Through this training, your team can better use and maintain the motor and reduce the incidence of failure. At the same time, we will also regularly share the latest development of motor technology and maintenance experience, maintain close technical exchanges with you, and help you improve your ability in motor use and maintenance.