Product Description
The automotive wiring harness is a critical component that connects various electrical systems within a vehicle, ensuring seamless communication between them. It consists of a collection of wires, connectors, and terminals that are carefully routed and bundled together for protection and organization. Designed to withstand harsh conditions such as temperature fluctuations, moisture, and vibrations, the harness offers long-lasting durability and reliability. Automotive wiring harnesses are custom-designed for each vehicle model, accommodating specific power, lighting, and control needs. High-quality insulation materials ensure safety by preventing short circuits and electrical failures. This essential product guarantees optimal performance of a vehicle’s electrical systems.
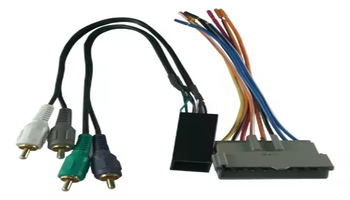
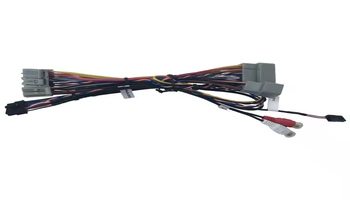
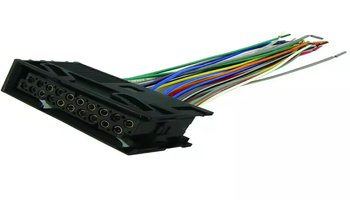
Product parameters
List | Details |
---|---|
Brand Name | OEM&ODM |
Application | Automobile |
Length | Customized Length |
Wire Gauge | Customizable |
Material | pure cooper, customizable |
Service | OEM/ODM service |
Certification | IATF16949 ISO9001 UL |
Lead time | It depends on the complexity of the harness |
Custom Process
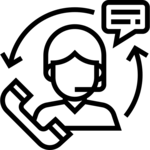
1. Send inquiries
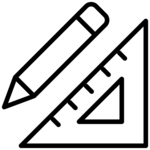
2.Drawings or samples
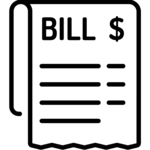
3. Quotation
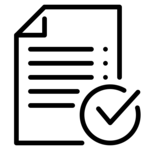
4.Customer confirmation
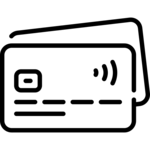
5. Places order and pays
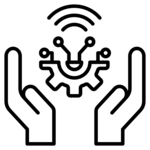
6.Mass production
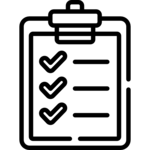
7.Test before packaging
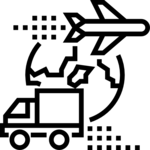
8.Shipping & confirmation
Process Type
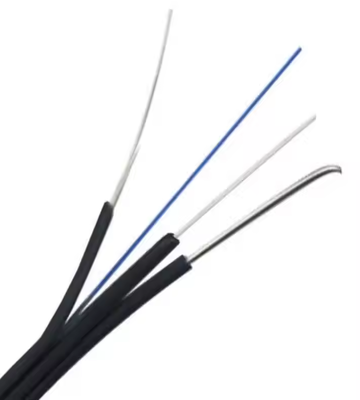
Cable wire
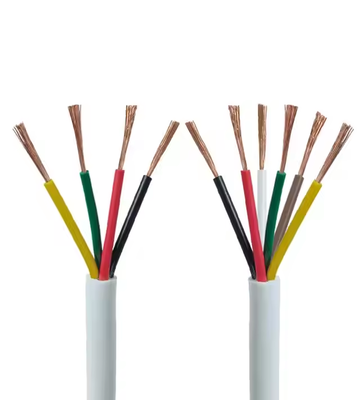
Optical fiber wire
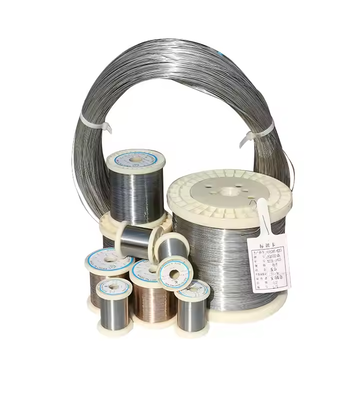
Bare wire
Material
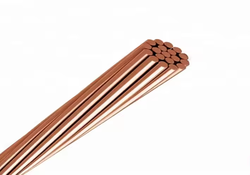
Bare copper
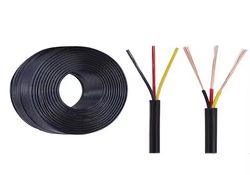
PVC PE
Quality Control
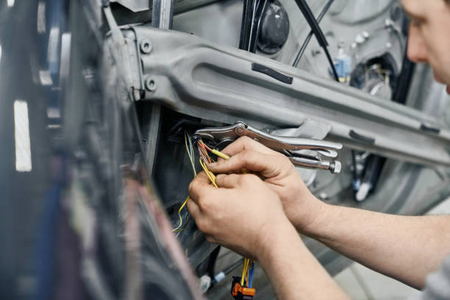
The Quality Control (QC) of automotive wiring harnesses ensures the highest standards of safety, performance, and durability. Each harness undergoes visual inspections to check for any defects in the wires, connectors, and insulation. Electrical testing is performed to verify proper conductivity and to ensure there are no short circuits or power loss. Environmental stress tests, including heat, cold, and vibration testing, ensure the harness can withstand harsh conditions. Crimping and soldering are carefully inspected for secure, reliable connections. Finally, the finished product is checked for proper assembly, labeling, and compliance with industry regulations.
Processing capability
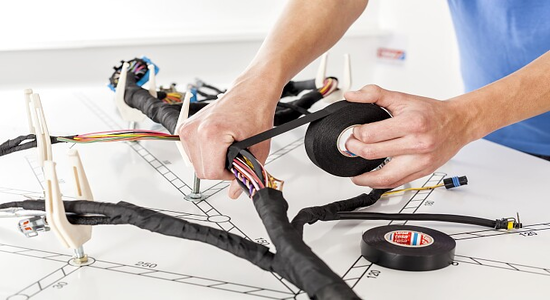
The processing capability of automotive wiring harnesses involves advanced manufacturing techniques to ensure precision, durability, and optimal performance. The process starts with the careful selection of high-quality wires and connectors, followed by automated cutting, stripping, and measuring to precise specifications. Wires are then routed and bundled together, often using specialized machines, to prevent tangling and ensure organized assembly. Connectors and terminals are securely attached through crimping or soldering techniques, ensuring a strong and reliable electrical connection.
To enhance durability, the wiring harness is insulated using materials like PVC, Teflon, or rubber, which protect against heat, abrasion, and moisture.
Additional processes
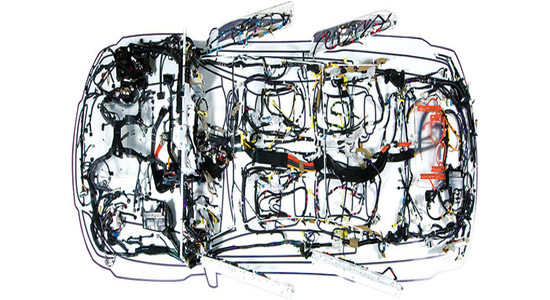
Harnesses are customized to meet the specific electrical requirements of different vehicle models, supporting functions such as power distribution, lighting, and control systems. Each harness undergoes rigorous electrical testing, including continuity and resistance checks, to ensure there are no faults, short circuits, or signal loss.
Automated machines and skilled labor work together for precise assembly, with advanced equipment used for functions like laser marking and terminal insertion. The harnesses are subjected to environmental testing, such as vibration, temperature cycling, and exposure to harsh conditions, to ensure long-lasting reliability in real-world automotive environments. Finally, every harness is visually inspected for defects, and compliance with industry standards is confirmed before shipment. This comprehensive approach ensures that automotive wiring harnesses are of the highest quality, capable of meeting the rigorous demands of the automotive industry.