Product Description
Spray Processing Treatment
Industrial-Grade Surface Coating Solution for Various Materials
Spray Processing Treatment is an advanced surface finishing technology that involves spraying a coating material onto the surface of components such as plastics, metals, or composites using high-pressure spray systems. This process creates a uniform, well-adhered film that enhances both functionality and appearance. It improves durability, visual appeal, and can add specific properties such as scratch resistance or surface gloss.
Designed to meet the needs of industries such as automotive, electronics, appliances, and premium packaging, Spray Processing Treatment is a key step in enhancing product value and overall quality.
Functional Features
1. Air Spray (Conventional Spray)
Description: Uses compressed air to atomize and spray the coating onto the surface.
Advantages: Fine atomization, good for smooth finishes.
Applications: Decorative coatings, glossy finishes, consumer electronics.
2. Airless Spray
Description: Forces coating material through a high-pressure nozzle without air, creating a fan-shaped spray pattern.
Advantages: High transfer efficiency, ideal for thicker coatings.
Applications: Industrial machinery, automotive parts, heavy-duty protection.
3. Electrostatic Spray
Description: Applies an electric charge to the paint particles, which are attracted to the grounded workpiece.
Advantages: High coverage efficiency, reduced overspray.
Applications: Automotive body panels, plastic casings, appliance surfaces.
4. HVLP (High Volume Low Pressure)
Description: Delivers a high volume of air at low pressure for fine atomization with minimal overspray.
Advantages: Precise control, better finish quality, eco-friendly.
Applications: High-end consumer products, cosmetic packaging, custom parts.
5. Robotic or Automated Spray Systems
Description: Uses programmable robotic arms to perform consistent, repeatable spray patterns.
Advantages: High consistency, efficient for large-scale production.
Applications: Mass production lines in automotive, electronics, and home appliances.
Product Display
Application
Paint or Primer Application for Finishing
In some CNC workflows, spray systems apply primers, paints, or other finishes directly to the machined part. This prepares components for final assembly or enhances aesthetics and corrosion resistance.
Industry | Automotive | Constucture |
Product parameters
Definition | A process that uses spray-based techniques for cooling, coating, cleaning, or finishing. |
Purpose | To improve surface quality, extend tool life, enhance material properties, or prepare parts for further processing. |
Types of Sprays | Coolants, lubricants, paints, primers, abrasive media, ceramic or metal powders. |
Common Tools Used | Spray nozzles, MQL systems, thermal spray guns, plasma torches, air jets. |
Types & Applications
Spray Type | Process Name | Purpose | Typical Materials/Media | Applications |
Coolant Spray | Flood Cooling / MQL | Reduce heat/friction during machining | Water-based coolant, oil mist | Milling, drilling, turning, grinding |
Abrasive Spray | Abrasive Jet Machining / Deburring | Remove burrs or clean surfaces | Sand, glass beads, aluminum oxide | Surface finishing, post-machining cleanup |
Thermal Spray | Plasma Spray / HVOF | Apply hard coatings | Tungsten carbide, ceramics | Aerospace, automotive (e.g., engine parts) |
Paint/Primer Spray | Automated Painting System | Aesthetic or corrosion protection finishes | Primer, industrial paints | Metal fabrication, enclosures |
Benefits of Spray Processing
Tool Life Extension | Cooling and lubrication reduce wear on cutting tools |
Improved Surface Finish | Proper spraying avoids overheating and surface burning |
Enhanced Material Properties | Thermal spray coatings add hardness, wear and corrosion resistance. |
Time & Cost Efficiency | Reduces need for secondary processes like polishing or manual deburring. |
Industries Using Spray Processing
Aerospace | Coating turbine blades, cooling precision parts |
Automotive | Engine component treatment, surface finishing |
Electronics | Fine component cooling and anti-corrosion coating |
Medical Devices | Clean, burr-free tools; biocompatible surface coatings |
Custom Process
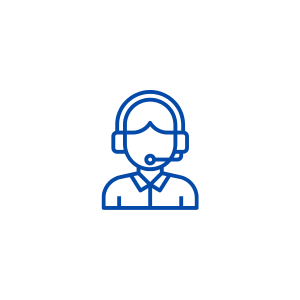
Contact
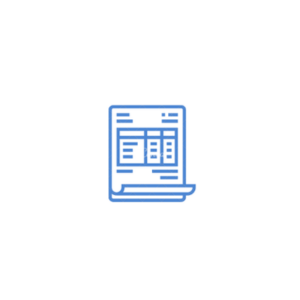
Negotiation
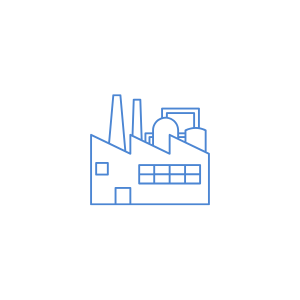
Mass Product
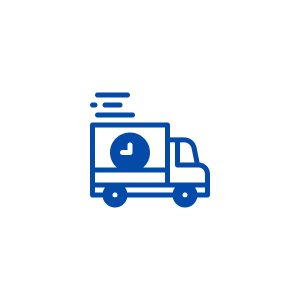
Transport
Quality Control
Stage | Inspection Method | Standards Followed | Tools Used |
Incoming Material Check | Visual + Chemical Analysis | ISO 9001 | Spectrometer, Caliper, Microscope |
Pre-Treatment Inspection | Surface Cleanliness | Internal Standard QC-01 | White cloth test, Tape test |
In-Process Monitoring | Thickness, Temperature | ISO 2063 / ISO 12944 | Digital Thickness Gauge, IR Thermometer |
Final Inspection | Coating Thickness, Adhesion | ISO 2409, ASTM D3359 | Elcometer, Cross Hatch Cutter |
Corrosion Test (optional) | Salt Spray Test (SST) | ASTM B117 | Salt Spray Chamber |
Documentation | Full QC Report for Each Batch | Customer & ISO Documentation | ERP/QC Management System |
Machine & Equipment List
Machine/Equipment | Specification | Function |
Spray Coating Booth (Manual) | 2.5m × 3.0m | Manual coating for complex parts |
Automatic Spray Line | Up to 6m part length | High-volume production, uniform coating |
Sand Blasting Machine | Pressure: 0.6–1.0 MPa | Surface cleaning and roughening |
Powder Coating Oven | Max Temp: 250°C, Size: 3m x 2m x 2m | Curing of powder-coated parts |
Thickness Measurement Gauge | 0–1500 µm (digital) | Measure coating thickness |
Salt Spray Test Chamber | ASTM B117 Standard | Corrosion resistance testing |
Surface Roughness Tester | Ra 0.05–40 µm | Measure treated surface finish |
CNC Part Holder/Fixture Machine | Custom build | Hold parts for uniform spray |
Air Compressor System | 10–15 bar | Provides air pressure for spraying |
FAQ
Question | Answer |
When is spray processing used | It is used during or after machining, such as to reduce heat (during milling or turning) or to coat/clean parts after machining is completed. |
How is it different from traditional coolant methods | Spray processing, such as MQL, uses minimal amounts of lubricant but is highly effective, producing less waste and is more suitable for high-precision work than traditional coolant methods. |
Can it be used with all materials | Yes, it can be used with most materials, such as metals (steel, aluminum), plastics, and even ceramics, depending on the type of spray and the material being sprayed. |
Does it require specialized equipment | Yes, specialized equipment is needed, such as spray nozzles, pressure control systems, storage tanks for lubricants, or thermal spray guns, depending on the type of spraying used. |
Does surface coating affect the accuracy of the part | If not controlled properly, it can affect the part's size or surface. However, when using precise techniques like plasma spray or HVOF, the impact is minimal and can be controlled effectively. |