产品描述
这款关节模组配备100:1高精密减速比,提供大扭矩输出与精准定位。集成无刷电机、高效谐波减速器,具备高刚性、低背隙、长寿命特性,适用于工业机器人、自动化设备等高精度、高负载场景,支持模块化快速集成。
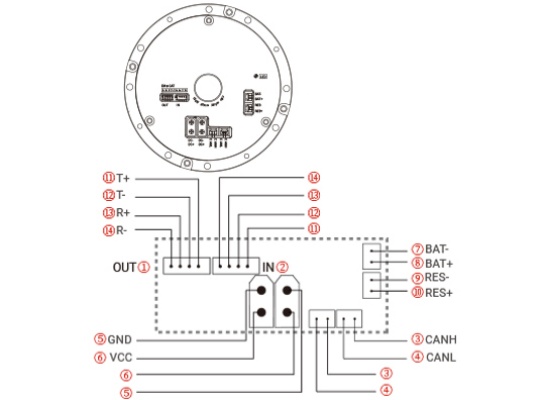
端口定义 | 端口说明 |
①EtherCAT_OUT | EtherCAT 输出 |
②EtherCAT_In | EtherCAT 输入 |
③CAN_H | CAN_H 网络信号端 |
④CAN_L | CAN_L 网络信号端 |
⑤GND | 电源负极 |
⑥VCC | 电源正极 |
⑦BAT- | 多圈电池负极 |
⑧BAT+ | 多圈电池正极 |
⑨RES- | 泄放电电阻口 |
⑩RES+ | 泄放电电阻口 |
⑪ T+ | 主站发送控制命令到模组 |
⑫ T- | 模组发送状态反馈到主站 |
⑬ R+ | 主站反射模组的状态数据 |
⑭ R- | 模组反射主站的控制命令 |
爆炸图
该产品体积紧凑,集成了FOC控制板,高精度多圈绝对编码器,无框转矩电机、精密谐波减速器等主要部件。
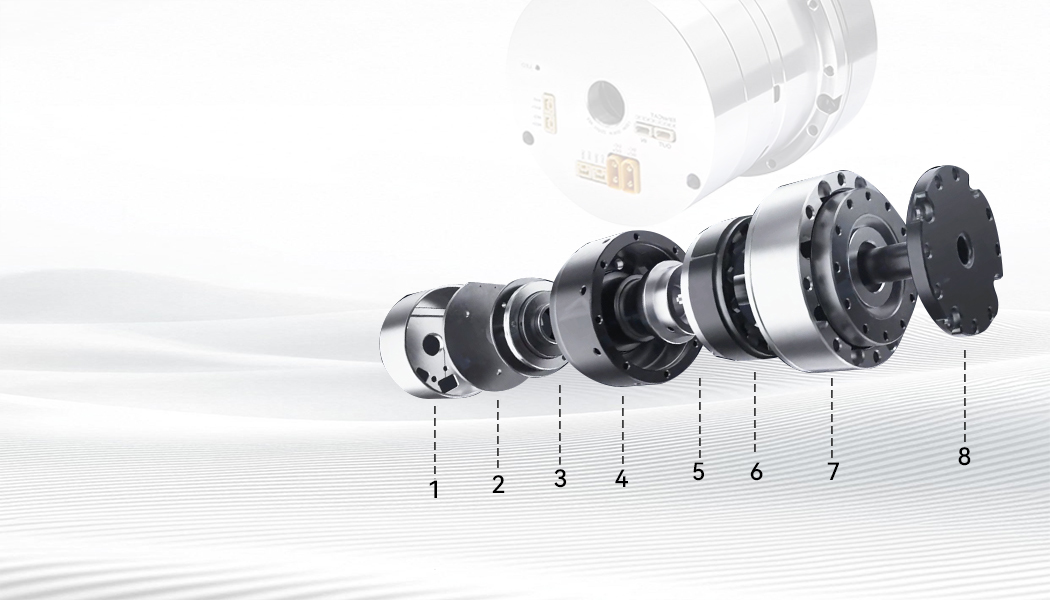
1.电机后盖
2.控制委员会
3.编码器
4.定子外壳
5.电动机转子
6.电机定子
7.谐波传动
8.柔性花键盖
谐波一体化关节交叉滚子轴承设计
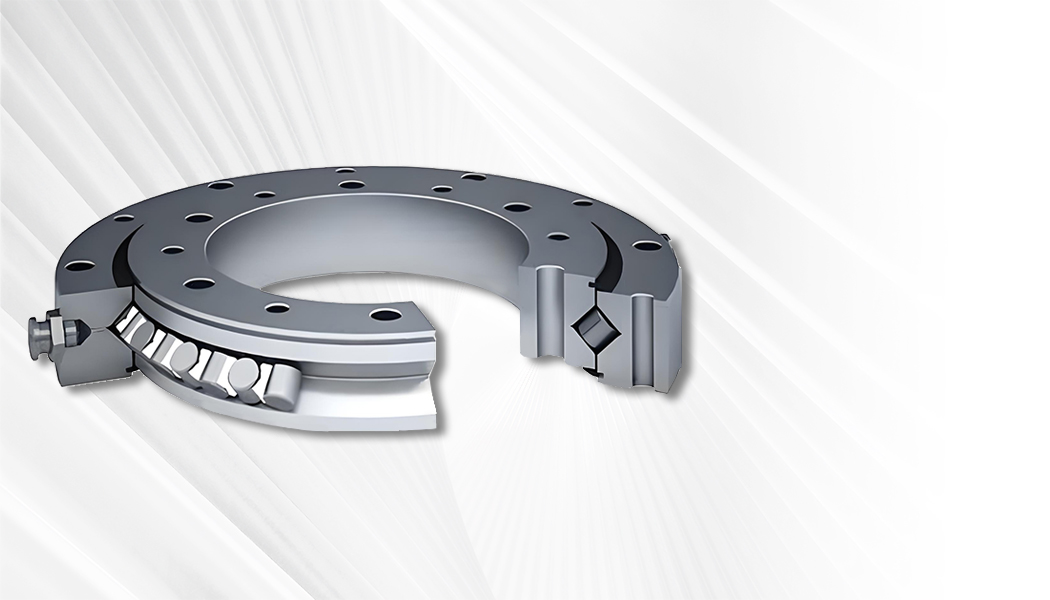
滚子呈90°交叉排列
使其可承受径向力、轴向力和倾覆力矩
具有高精度、高稳定性、高承载,高刚性的特点
双绝対值编码器
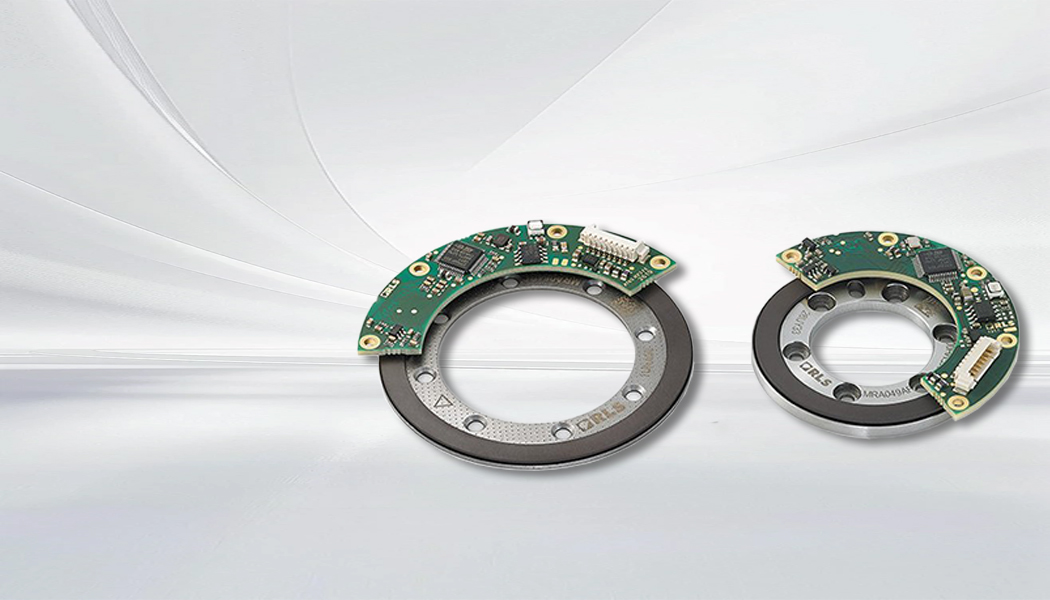
内置双绝对值编码器,全闭环控制
输出端采用17位绝对值编码器,重复定位精度小于0.01度,
可记忆单圈及多圈断电位置,全闭环控制,补偿传动误差,精度无磨损。
通讯协议
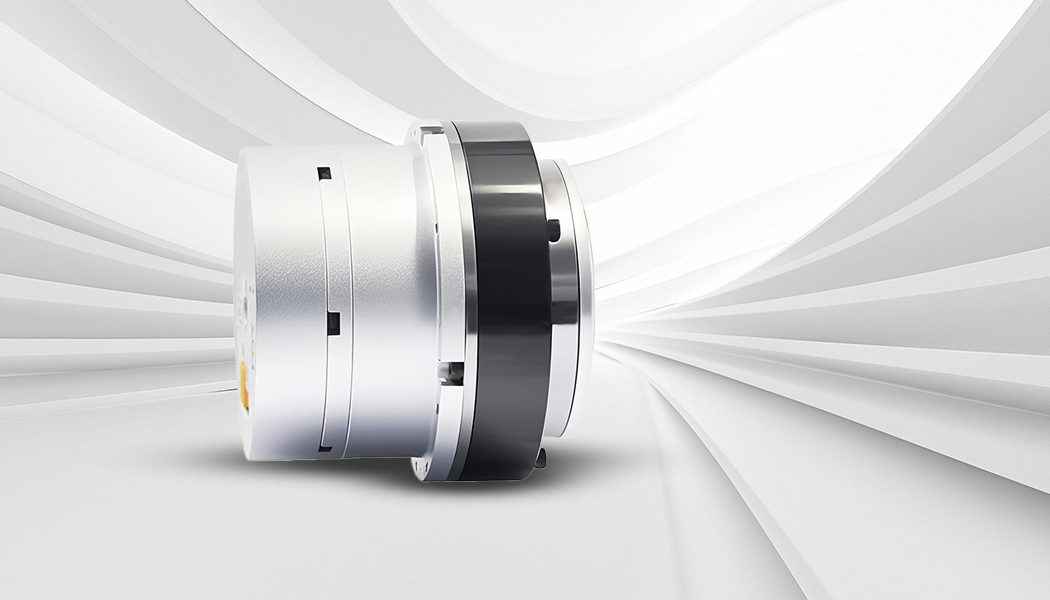
EtherCAT, CANopen通讯可选
位置,速度,电流回路PID实时可调
产品参数
参数 | 单位 | EHD - 14 | EHD-17 | EHD-20 | EHD-25 | EHD-32 |
减速比 | - | 100 | 100 | 100 | 100 | 100 |
输入电压 | V | 48 | 48 | 48 | 48 | 48 |
空载转速 | RPM | 30 | 30 | 30 | 30 | 20 |
空载电流 | A | 0.9 | 145 | 2.59 | 1.61 | 3.9 |
额定转速 | RPM | 25 | 25 | 25 | 25 | 18 |
额定转矩 | N.m | 11 | 35 | 50 | 108 | 150 |
额定功率 | W | 100 | 180 | 250 | 400 | 700 |
额定电流 | A | 6.5 | 9 | 13 | 16 | 20 |
峰值扭矩 | N.m | 28 | 54 | 80 | 157 | 229 |
峰值电流 | A | 16.25 | 13.86 | 20.8 | 23.2 | 33.44 |
反电势常数 | Vdc/kgm | 1.39 | 2.79 | 2.79 | 4.89 | 6.28 |
扭矩常数 | N.m/A | 0.02 | 0.04 | 0.04 | 0.07 | 0.09 |
线电阻 | Ω | 0.62 | 0.7 | 0.36 | 0.155 | 0.08 |
线电感 | mH | 0.43 | 0.47 | 0.51 | 0.33 | 0.18 |
极对数 | - | 10 | 10 | 10 | 10 | 10 |
接线方式 | - | Y | Y | Y | Y | Y |
背隙 | Arcsec | - | <20 | <20 | <20 | <20 |
编码器类型及接口 | - | Dual encoder/ABS - 17bit | Dualencoder/ABS-17bit | Dualencoder/ABS-17bit | Dualencoder/ABS-17bit | Dualencoder/ABS-17bit |
重复定位精度 | Degree | <0.01 | <0.01 | <0.01 | <0.01 | <0.01 |
通信方式 | - | CAN / EtherCAT | CAN /EtherCAT | CAN /EtherCAT | CAN/ EtherCAT | CAN /EtherCAT |
绝缘等级 | - | F | F | F | F | F |
堵转扭矩数据 | ||||
EHD-20 | 扭矩 | 温升 | 堵转时间 | 相电流 |
(N.m) | (℃) | (s) | (Arms) | |
75 | 12 | 15 | 10.5 | |
100 | 8 | 10 | 13.5 | |
125 | 15 | 8 | 18 |
*1.标准品电机只支持非抱闸。
*2.标准品电机支持CAN总线和EtherCAT。
*3.标准品电机没有防水功能,如需IP54请订单前联系销售。
*4.此产品还支持50:1的减速比,订购前请联系销售确定交期。
*5.额定扭矩测试方法:在环境温度摄氏24度(无其他散热方式)下,在额定转速下进行测试,电机扭矩在温升60度条件下达到温度平衡、可长时间工作点为该电机额定扭矩值。
尺寸图
应用
该关节模组是一款高性能的机电一体化驱动单元,集成了高扭矩无刷电机、精密减速器和智能控制系统,适用于机器人关节、自动化设备及工业机械臂等场景。其50N·m的额定扭矩和13A的电流输出,可满足中高负载需求,同时具备高精度、低噪音和长寿命特性。模块化设计支持快速安装与维护,广泛应用于协作机器人、医疗设备、物流分拣及智能制造领域,显著提升设备的动态响应与能效表现。
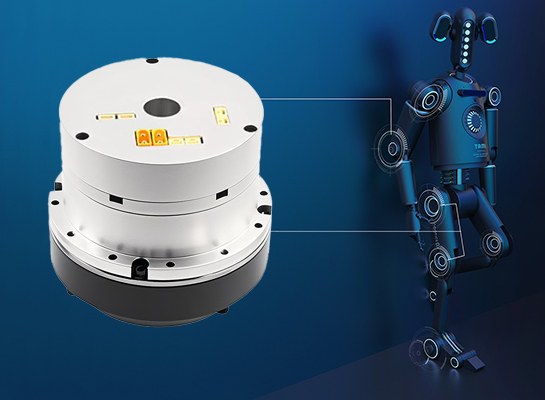
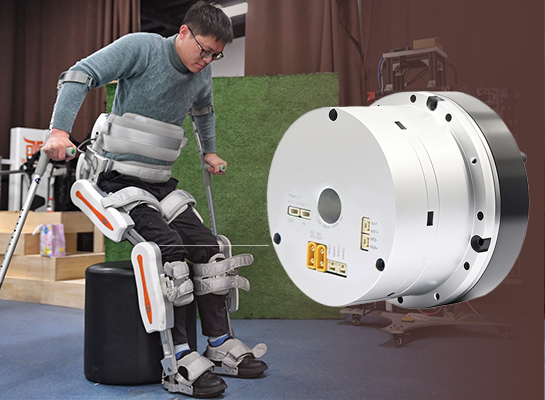
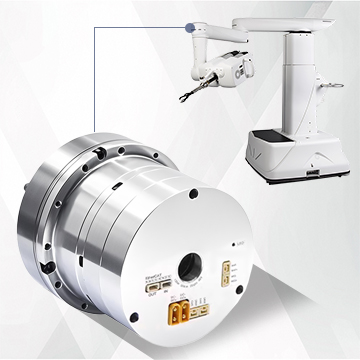
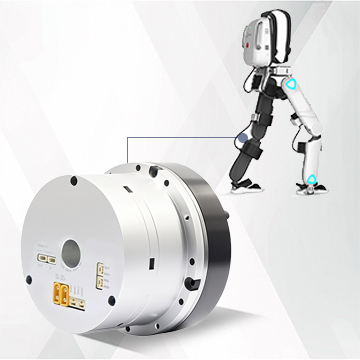
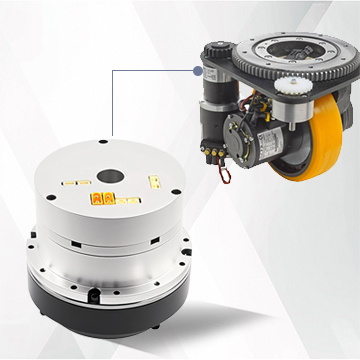
服务
1. 是否支持防水防尘?防护等级是多少?
是的,我们的关节模组可根据客户需求定制防水防尘功能。 标准款为室内应用型不防水,可选配IP54等级防护,适合一定的户外或潮湿环境使用。
如有更高防护需求(例如IP67),可联系定制。
2. 是否支持减速比定制?
支持。我们可以根据您的应用需求提供不同减速比的定制方案。
常规减速比范围覆盖:10:1 ~ 200:1,具体可根据负载、速度、扭矩要求匹配最佳组合。
3. 单编码器和双编码器版本有什么区别?
单编码器版本监测电机端转动,适用于一般精度要求场合;双编码器版本同时监测电机端和输出端,能有效补偿齿隙和弹性误差,适用于高精度控制和安全要求高的应用(如协作机器人、医疗设备)。
4. 关节模组可以支持哪些通讯接口?
标准版支持模拟量控制(电流/电压指令)或脉冲指令控制;
根据需求,可选配支持CANopen、EtherCAT、Modbus-RTU等工业总线协议(需定制)。
5. 是否支持驱控一体?可以直接连接控制器吗?
我们提供可选的驱控一体版关节模组,内置电机驱动器和位置伺服控制器,
用户可直接通过总线或脉冲接口控制,无需外接独立驱动器,简化布线和系统集成。
6. 有标准的3D模型文件可以下载吗?
有的。我们为所有型号提供STEP格式的三维模型文件,便于客户快速进行机械设计集成。
如需获取,请联系我们销售人员获取下载链接或资料包。
7. 工作温度范围是多少?
标准工作温度范围为:-10°C ~ +50°C。
如需耐低温或耐高温应用环境(如冷库、热作业环境),可以定制特殊温控方案。
8. 关节模组是否可以空心设计?能走线吗?
部分型号是空心轴设计,中心孔径可用于走线、走气管、水管等,便于实现复杂末端执行器的功能布局。
具体中心孔径尺寸请参考型号选型表或咨询客服。
9. 标准交期和定制交期多久?
标准型号交期:通常为7-14个工作日。
定制需求(如减速比定制、通讯协议定制等)交期根据具体要求而定,一般5-10周。
10. 质保期多长?售后服务如何?
所有关节模组产品提供12个月质保期(正常使用情况下)。
我们提供远程技术支持,故障诊断指导,以及快速备件供应服务。质保期外也可提供有偿维修和维护服务。
包装图
包装清单
1.电源线*2
2. CAN总线通讯连接线*4
3.120Ω终端电阻*1
4. EtherCAT通讯连接线*2