Product Description
Our Anodized Aluminum Custom Parts are designed and manufactured to meet your exact engineering and aesthetic requirements. Through anodized oxidation treatment, the aluminum surface is transformed into a durable, corrosion-resistant, and decorative oxide layer. These parts are suitable for critical applications in aerospace, automotive, medical devices, electronics, and precision machinery.
We provide end-to-end services—from design consulting, anodizing treatment, quality inspection, to packaging and delivery.
Key Benefits
Durable and Long-Lasting | Anodized aluminum has a much longer lifespan than untreated aluminum, especially in outdoor or high-wear environments. |
Custom Appearance | Color anodizing allows for a premium, consistent finish in black, silver, red, gold, blue, or custom shades. |
High Precision | Every part is produced with tight tolerances and professional machining, ensuring seamless integration into your final product. |
Eco-Friendly Process | Anodizing uses non-toxic chemicals, creates no harmful byproducts, and produces recyclable waste |
Improved Adhesion | The anodized layer allows better adhesion for paints, adhesives, and lubricants, making it ideal for secondary processes |
Functional Features
Type II – Decorative Anodizing
Key Advantages:
| |
Type III – Hardcoat Anodizing
Key Advantages:
|
Product Display
Application
Automotive Engine components, interior trim, nameplates | Aerospace Fuselage parts, brackets, housings, fasteners | Electronics Device enclosures, heat sinks, connectors |
Medical Surgical tools, casings for medical equipment | Construction Window frames, railing hardware, fixtures | Consumer Products Laptop covers, sports equipment, furniture components |
Product parameters
Attribute | Specification |
Material Options | 6061, 7075, 5052, 2024 Aluminum |
Surface Finish | Clear, Black, Red, Blue, Gold, or Custom |
Anodizing Type | Type II (Standard), Type III (Hardcoat) |
Dimensional Tolerance | ±0.01 mm |
Max Machined Size | Up to 1200 mm x 800 mm |
Min Wall Thickness | 0.5 mm (depending on material) |
Coating Thickness | 5–25 µm |
RoHS/REACH Compliant | Yes |
Pre-Treatment
Step | Purpose |
Degreasing / Cleaning | Removes oils, machining fluids, and contaminants from the surface |
Etching | Uses caustic solution to clean and slightly roughen the aluminum |
Desmutting | Removes non-aluminum residues (e.g., copper, silicon) after etching |
Anodizing Process
Parameter | Type II (Standard Anodizing) | Type III (Hard Anodizing) |
Electrolyte | Sulfuric acid (15–20%) | Sulfuric acid (15–20%) with stricter controls |
Voltage | 12–20 V | 40–100 V (depending on part size and material) |
Temperature | ~20°C (68°F) | 0°C to 5°C (32°F to 41°F) |
Time | 20–30 minutes (depending on desired thickness) | 30–90 minutes (longer for thicker coatings) |
Coating Thickness | 5–15 µm | 20–25 µm or more |
Color Dyeing (optional) | Dye applied before sealing for colored finishes | Usually dark natural color; dyeing limited |
Post-Treatment
Step | Purpose |
Sealing | Closes microscopic pores in the anodized layer to improve corrosion resistance and dye stability (can use hot water, steam, or nickel acetate) |
Rinsing | Thorough water rinse to remove residual chemicals |
Drying | Air dry or oven dry depending on part and volume |
Custom Process
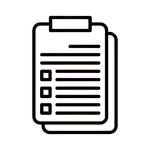
Initial Inquiry
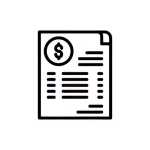
Quotation
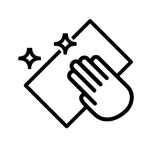
Surface Preparation
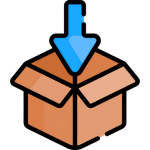
Packing & Delivery
Quality Control
Our QA system ensures consistency and reliability in every production batch:
Incoming Material Inspection
In-process Dimensional Checks using CMM and calipers
Post-anodizing Adhesion and Thickness Test
Salt Spray Test for corrosion resistance
Color Matching and Finish Uniformity Review
Final QC Report with photos and measurements available
Machine & Equipment List
Equipment | Description |
Automatic Anodizing Line | Type II & III anodizing with color options |
CMM (Coordinate Measuring Machine) | High-accuracy dimensional inspection |
Spectrophotometer | Ensures color consistency and quality |
Salt Spray Chamber | Corrosion resistance testing |
Surface Roughness Tester | Measures Ra values for functional surfaces |
Ultrasonic Cleaning Machine | Pre-treatment before anodizing |
FAQ
Question | Answer |
What industries typically use anodized aluminum parts? | These parts are widely used in aerospace, electronics, marine, medical equipment, architectural components, and robotics. |
How do you ensure color consistency in anodized parts? | We use calibrated spectrophotometers and batch control during anodizing to ensure color uniformity, especially for large volume orders. |
Can you handle both prototyping and mass production? | Yes, we specialize in both. Whether you need 1 prototype or 10,000+ units, we adjust our production line to suit your needs. |
What file formats do you accept for quotations or production? | We accept STEP, IGES, STL, DWG, DXF, PDF, and other common CAD formats. |
What is your standard lead time? |
|