Product Description
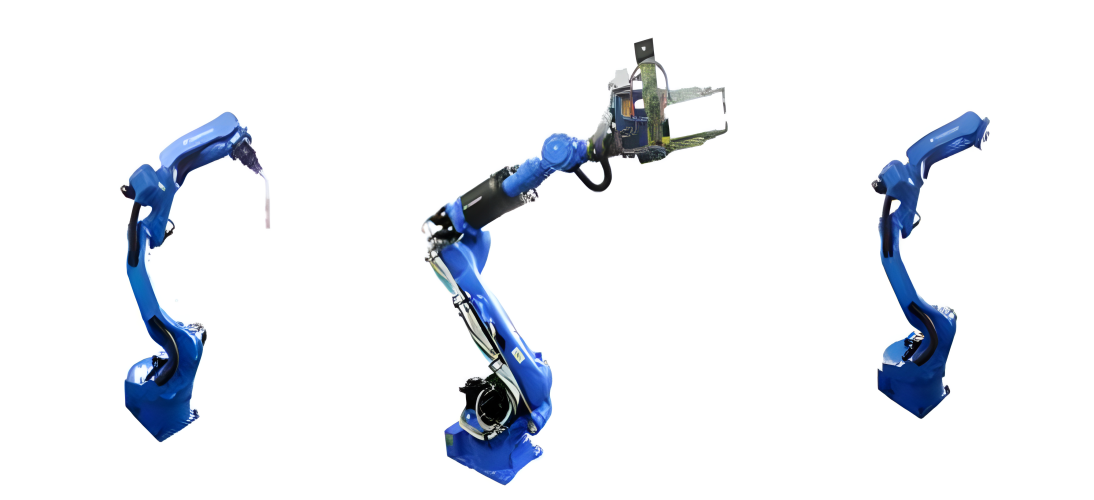
The VersaWeld™ Collaborative Robotic Spot Welding Platform is a next-generation automated welding solution designed to deliver unmatched precision, flexibility, and safety in modern manufacturing environments. Integrating collaborative robots from Universal Robots, smart vision inspection, customizable tooling, and linear actuator-supported 7th axis movement, VersaWeld™ is engineered to streamline spot welding operations across various industrial sectors.
This modular and scalable solution empowers manufacturers with high precision pick-and-place capabilities, real-time performance monitoring, and post-weld inspection, making it ideal for complex assemblies, multi-line production environments, and Industry 4.0 readiness.
Applications
Industry | Use Case | Benefits |
Automotive | Spot welding body panels, seat frames, brackets | Consistent weld quality, safety-certified cobots |
Electronics | Welding of metal enclosures and grounding components | High precision in small assemblies |
Home Appliances | Spot welding internal metal structures (ovens, washers) | Modular for multiple product lines |
Metal Fabrication | Custom fixture-based welding for small batch runs | Easy-to-reprogram for new parts |
Aerospace Components | Precision spot welding on lightweight alloys | Vision-guided alignment, high repeatability |
Product Features
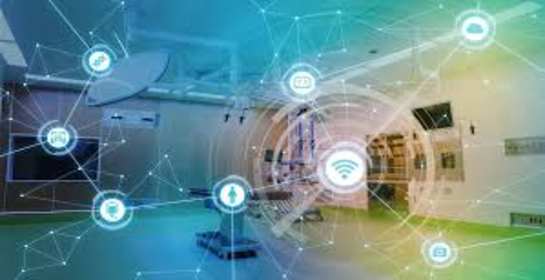
Smart Vision-Based Calibration & Inspection
Equipped with an arm-mounted camera and post-welding inspection system, VersaWeld™ ensures each weld is placed with pinpoint accuracy and then automatically verified. This dual-stage vision integration:
Reduces manual inspection time
Guarantees quality compliance
Minimizes rework by identifying inconsistencies instantly
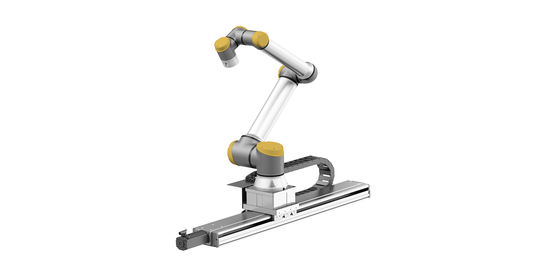
7th Axis Linear Motion Integration
With cobots mounted on linear actuators, the system gains a 7th axis for expanded reach and flexibility. This feature is particularly useful in:
Accessing multiple weld points across large workpieces
Servicing multiple fixtures along a production line
Improving cycle time by reducing repositioning steps
Product parameters
Parameter | Value |
Cobot Payload Options | 3.5 kg / 10 kg |
Repeatability | Up to 30 microns |
UPH (Units Per Hour) | 200 |
Product Loading Formats | Tray, Cassette, Magazine, Custom Racks |
Vision Accuracy | ±0.6 mm |
Power Requirement | 220–240 VAC, Single Phase, 50/60Hz |
Compressed Air Requirement | 0.6 MPa (Clean Dry Air) |
Welding Configuration | On-station welder / Cobot-mounted welder |
Customer Case
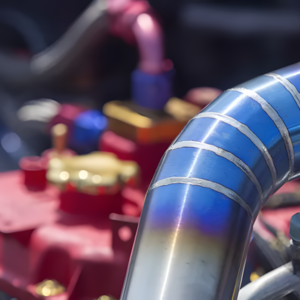
Automotive Seat Frame Welding
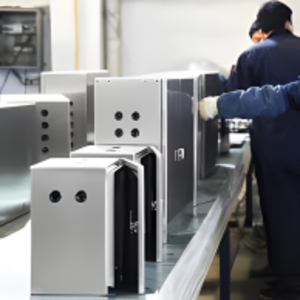
Consumer Electronics Enclosure Assembly
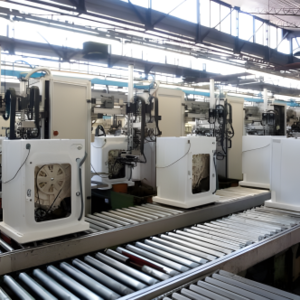
Appliance Manufacturing
FAQ
1. Can VersaWeld™ be integrated into existing production lines?
Yes, its modular design supports retrofitting and integration into existing lines with minimal disruption.
2. What types of materials can be spot welded using this system?
The system supports various conductive metals such as mild steel, stainless steel, aluminum, and coated materials.
3. Is operator training required to use the system?
Basic training is recommended, but UR cobots are user-friendly with intuitive programming interfaces. Support and training packages are available.
4. How does the real-time utilization monitoring work?
Through secure cloud-based software, the system reports utilization metrics, cycle time, and maintenance alerts accessible from remote dashboards.
5. What safety features are in place for human-robot collaboration?
All cobots include force-limiting sensors, emergency stop functions, and are ISO 10218-1 and ISO/TS 15066 compliant for collaborative workspaces.