Description

AGV-CDD16 Stacker Autonomous Forklift
Intelligent unmanned forklift is a logistics handling equipment that integrates advanced technologies such as artificial intelligence, automatic control, and laser navigation. It extends the management system to the intelligent forklift through the Internet of Things technology and data collection technology, realizing the intelligentization and automation of warehousing operations.
Product Features
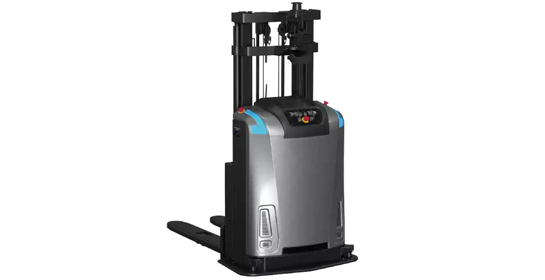
Support multi-machine collaboration
Can seamlessly access Wanwei intelligent forklift dispatching software system to achieve flexible collaboration of multiple models and improve work efficiency.
High-precision navigation is optional
Supports four navigation methods: SLAM, QR code, reflector, and NFL, covering navigation needs of various scenarios.
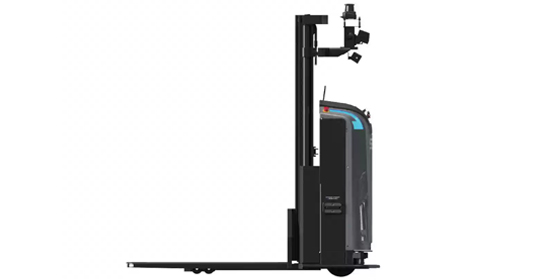
Modular industrial design
Multi-modular industrial design, such as operation panel, sensor bracket, wiring harness, etc., is easier to disassemble and maintain.
Can identify non-standard pallets
Wide-angle high-precision recognition, accurate and fast, ensures handling efficiency, supports national standard, European standard and non-standard pallet recognition.
Structure Diagram
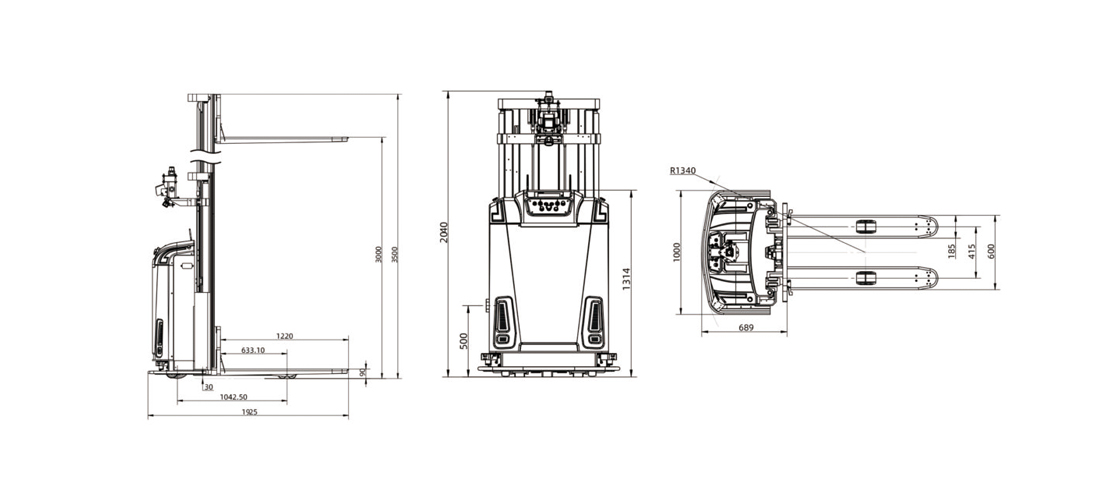
Product Params
Product model | AGV-CDD16 | |
Basic parameters | Product name | Laser SLAM Stacker Autonomous Forklift |
Operation type | Automatic navigation, by manual control device | |
Navigation type | Laser SLAM | |
Pallet type | Open pallet | |
Rated load capacity | 1600 kg | |
Load centre distance | 600 mm | |
Weight (with battery) | 1090 kg | |
Standard lifting height | 3000 mm | |
Forklift dimensions: L x W x H | 1925 x 1000 x 2040 mm | |
Fork dimensions: L x W x H | 1220 x 185 x 55 mm | |
Fork outer width | 550 / 600 / 685 mm | |
Minimum turning radius | 1340+200 mm | |
Ambient temperature and humidity range | TEMP: 0°C to 50°C / RH: 10% to 90%, no compression, no condensation |
Performance parameters | Driving speed: full load / no load | 2 / 2 m/s |
Passability (slope / step / gap) | <5% / 5 mm / 15 mm | |
Navigation position accuracy | ±10 mm | |
Navigation angle accuracy | ±0.5° | |
Battery parameters | Battery specifications | 24 V / 173 Ah (lithium iron phosphate) |
Comprehensive battery life | 8 to 10 h | |
Charging time (10% to 80%) | 2 h | |
Charging method | Manual / Automatic |
Function configurations | Lidar number | 1 (H1) + 3 (C2) |
Wi-Fi roaming | Standard | |
3D obstacle avoidance | Optional | |
Pallet recognition | Optional | |
Cage stack | Optional | |
High shelf pallet recognition | Optional | |
Pallet stack | Optional | |
HMI display | Standard | |
Safety configurations | E-stop button | Standard |
Sound and light indicator | Standard | |
Braking distance: 1 m/s / 1.5 m/s | ≤30 cm / ≤50 cm | |
360° laser protection | Standard | |
Bumper strip | Standard | |
Fork height protection | Standard | |
Certifications | EMC | Standard |
UN38.3 | Standard |
Company Introduction
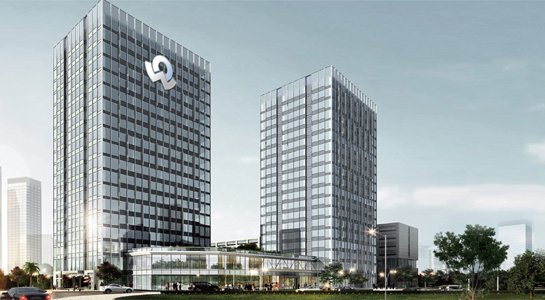
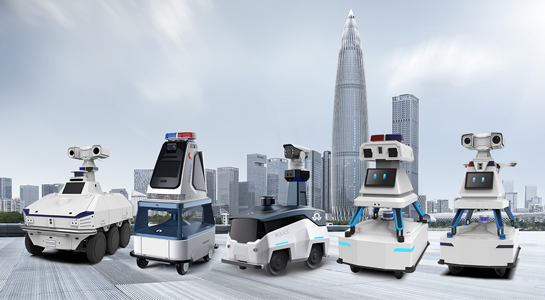
Changsha Oneway Robotics Co., Ltd. was founded by former members of the National University of Defense Technology’s robotics team. The company focuses on security patrol robots and inspection robots and system solutions, aiming to enhance operational efficiency in security tasks through the use of security robots and control systems. The company possesses advanced technology in robot chassis control, low-speed unmanned driving, and image processing algorithms. It has vertically applied these technologies in areas such as park security, port patrols, specialized industry inspections, industrial distribution, and military applications. Meanwhile, Oneway robotics, under its main robot business, has incubated two internal sectors—Oneway Intelligent Control and Oneway IoT (Internet of Things), forming a business line with Oneway Robotics at its core and Oneway Intelligent Control and Oneway IoT as complementary components.
Certificate Honor
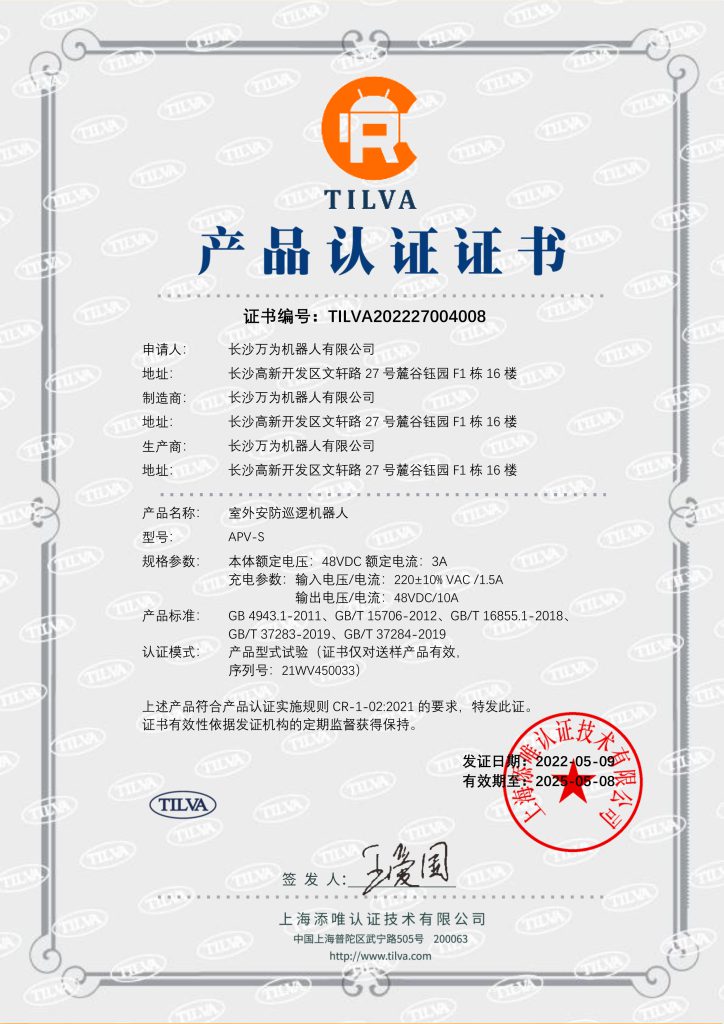
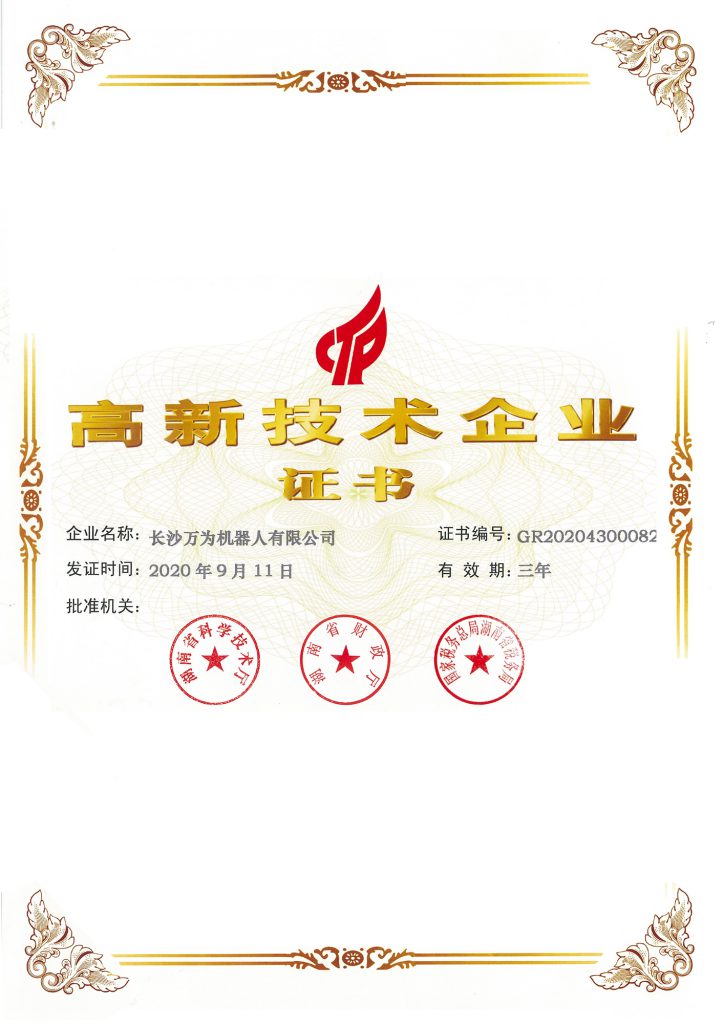
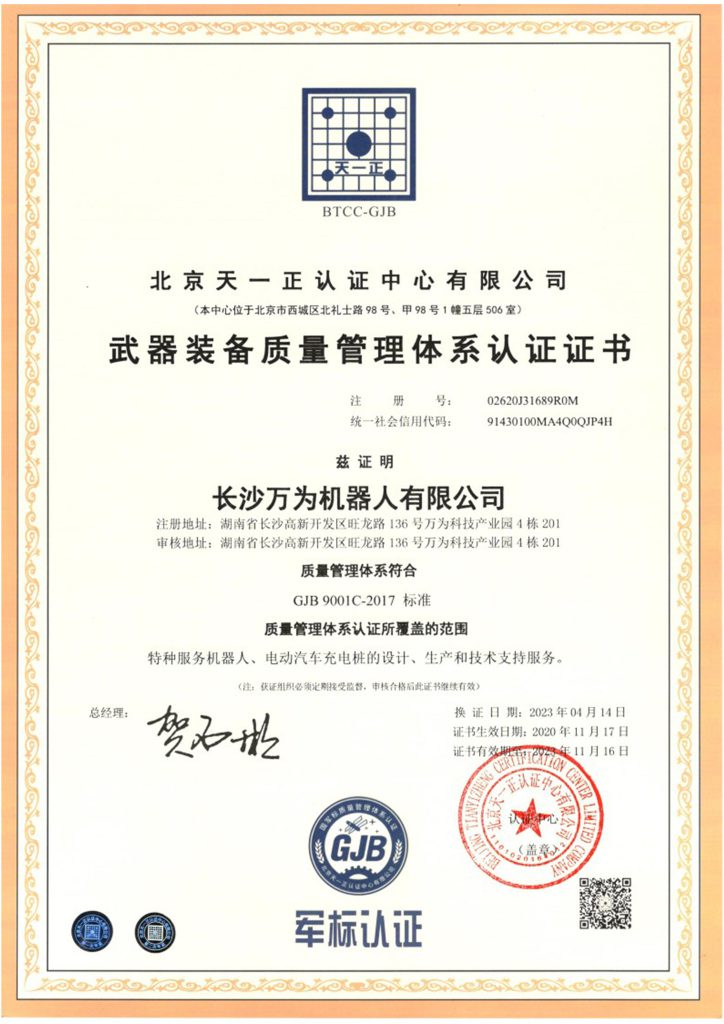