Product Description
Coreless design
The tattoo machine coreless brush DC motor abandons the core structure of the traditional motor. This design reduces the hysteresis and eddy current losses caused by the iron core, and the efficiency of the motor is significantly improved. At the same time, the coreless structure also reduces the weight and volume of the motor, making the tattoo machine more portable and easy for the tattoo artist to operate for a long time without fatigue.
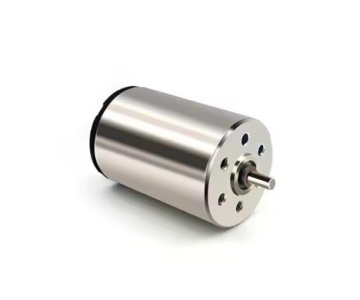
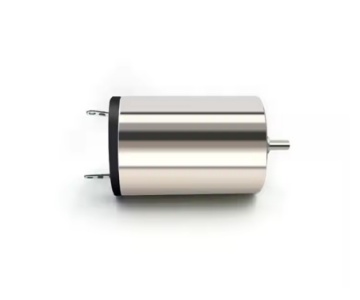
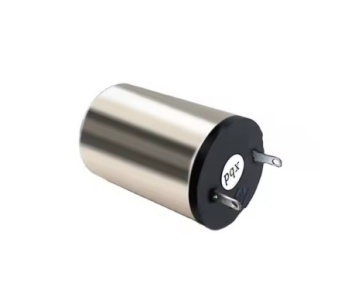
Product parameters
Motor parameter | Motor type | ||||
---|---|---|---|---|---|
name | unit | XBD19280 6090HJ- 20100 | XBD19280 9100HJ- 20100 | XBD19281 2100HJ- 20100 | XBD19282 4152HJ- 20100 |
Rated voltage | V/DC | 6 | 9 | 12 | 24 |
Rated speed | rpm | 7965 | 8850 | 8000 | 12160 |
Rated current | A | 0.5 | 0.5 | 0.6 | 0.9 |
Rated torque | mi | 2.9 | 4.1 | 7.1 | 13.7 |
No-load speed | rpm | 9000 | 10000 | 10000 | 15200 |
No-load current | mA | 40 | 30 | 20 | 35 |
Maximum efficiency | % | 81 | 83.8 | 84.7 | 83.3 |
Rotational speed | rpm | 8280 | 9200 | 9250 | 13680 |
Electric current | A | 0.4 | 0.4 | 0.3 | 0.5 |
torque | mNm | 2 | 2.8 | 2.7 | 6.8 |
Maximum power | W | 5.9 | 9.3 | 9.3 | 27.2 |
Rotational speed | rpm | 4500 | 5000 | 5000 | 7600 |
Electric current | A | 2 | 2.1 | 1.6 | 2.3 |
torque | mNm | 12.4 | 17.8 | 17.8 | 34.2 |
Locked-rotor current | A | 4 | 4.2 | 3.2 | 4.6 |
Locked-rotor moment | mNm | 24.8 | 35.6 | 35.6 | 68.3 |
Motor impedance | Ω | 1.51 | 2.14 | 3.81 | 5.22 |
Inductive reactance of motor | mH | 75 | 155 | 260 | 510 |
Torque constant | mNm/A | 6.3 | 8.53 | 11.39 | 14.96 |
Speed constant | rpm/V | 1500 | 1111.1 | 833.3 | 633.3 |
Revolution/torque constant | rpm/mNm | 362.5 | 281 | 280.6 | 222.5 |
Mechanical time constant | ms | 8.7 | 6.7 | 6.7 | 5.3 |
Rotor inertia | gcm2 | 2.29 | 2.29 | 2.29 | 2.29 |
Technological Innovation
Brushed system
The motor is equipped with a brush system including a brush and a commutator. Brushes are generally made of conductive materials such as graphite, which is in close contact with the commutator. The commutator is composed of a plurality of electrically conductive pieces insulated from each other and installed on the rotating shaft of the motor. During the operation of the motor, the brush conducts the current of the external power supply to the commutator, and then the commutator distributes the current to the rotor winding, and changes the direction of the current in a timely manner to ensure the continuous and stable rotation of the motor.
Product Display
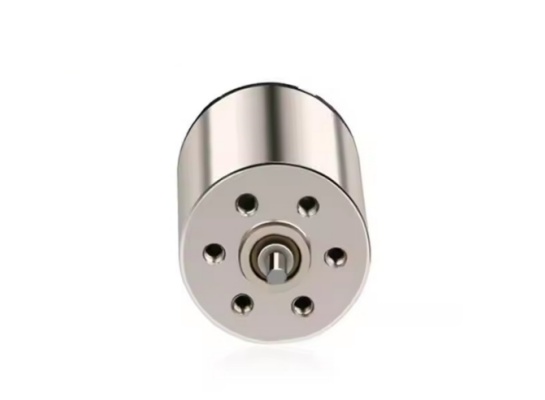
Low noise and vibration
The noise and vibration generated by the coreless brushless DC motor are relatively small in operation. During the tattoo process, a quiet operating environment is very important for both the tattoo artist and the customer. The low vibration characteristics also help to improve the stability of the operation of the tattoo machine, so that the tattoo artist can more accurately control the placement and movement of the tattoo needle, reducing the deviation of the tattoo pattern caused by vibration.
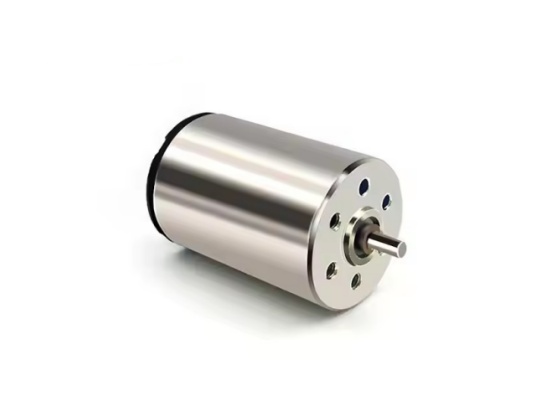
Stable power output
The motor provides stable power to the tattoo machine, ensuring that the tattoo needle exerts even force when piercing the skin. This is essential to ensure the quality of the tattoo, whether drawing fine lines or filling in large areas of color, the stable power output enables the tattoo needle to evenly inject pigment into the skin, making the tattoo pattern full of color and smooth lines.
Size & Interface
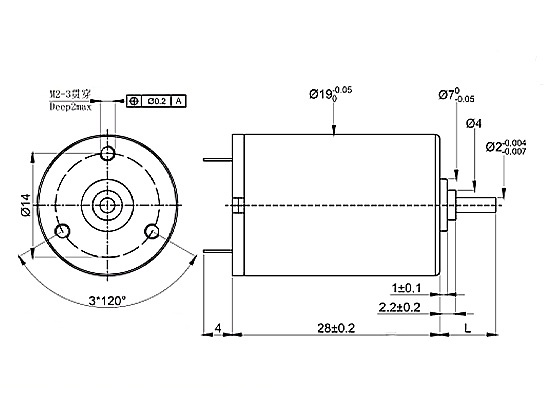
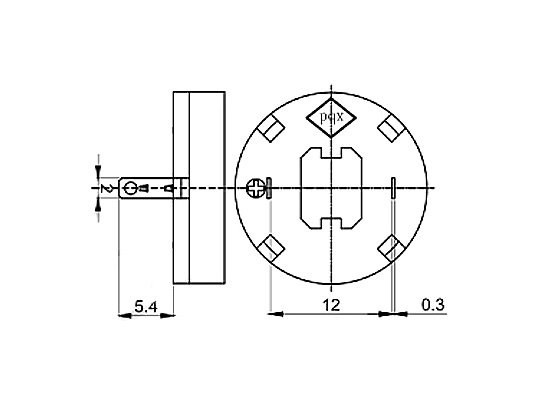
Quality Control
Assembly link control: tight seam
The assembly process of the motor is like a precise jigsaw puzzle, where every component must be fitted into place without error. Our assembly workers are professionally trained, have rich experience and a high sense of responsibility. When assembling the hollow cup rotor, ensure that its position in the stator is accurate and the clearance with the brush and commutator is just right. The tightening torque of each screw is precisely calculated and strictly controlled to prevent the overall performance of the motor from being too tight or too loose. After the assembly is completed, the appearance of the motor is also carefully checked to ensure that no parts are loose, scratched or improperly assembled.
Performance testing: Comprehensive inspection
We have a set of perfect performance testing system, for each hollow cup brush motor for comprehensive and strict inspection. In terms of electrical performance detection, the starting current, no-load current, rated power, speed and torque of the motor are measured by high-precision test equipment to ensure that these parameters are within the specified tolerance range and meet the design requirements. For the mechanical properties of the motor, we simulate the actual working environment and carry out long-term operating tests to observe the vibration, noise level and heating degree of the motor. Only motors that are fully qualified in all performance indicators will be labeled as qualified in quality and enter the market.
Durability test
In order to ensure the reliability and life of the motor, we will carry out a long time durability test on the motor. In the simulation of various actual working conditions, the motor is continuously run for hundreds of hours, during which the performance indicators of the motor are continuously monitored, such as temperature changes, vibration conditions, electrical parameter stability, etc. Only motors that pass the durability test and have no significant degradation in performance will be considered qualified products.
Quality traceability system: Tracing to the source
In order to ensure the continuous stability of quality, we have established a sound quality traceability system. Each hollow cup brush motor has a unique identity, from the procurement batch of raw materials, all aspects of the production process data to the final test report, are recorded in detail. Once a quality problem is found, it can be quickly traced back to the root of the problem, and effective corrective measures can be taken to avoid the recurrence of similar problems.
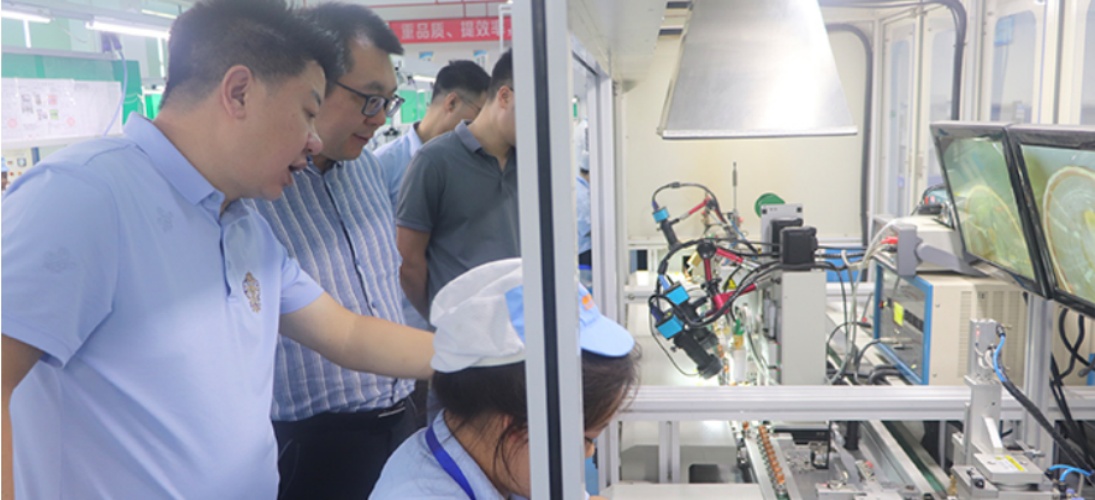
Application Cases
Coreless mini DC motor: Power star in beauty and medical field
In beauty and medical, two areas that require high precision, stability and safety, core-less mini DC motors are playing an irreplaceable role, becoming a powerful power support behind advanced instruments such as tattoo pens, dental equipment and magnetic resonators.
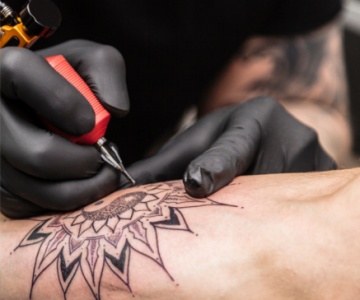
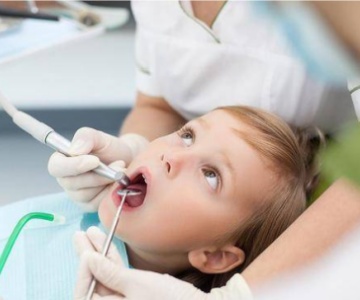
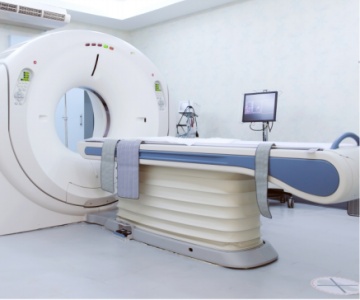
Cooperative partner
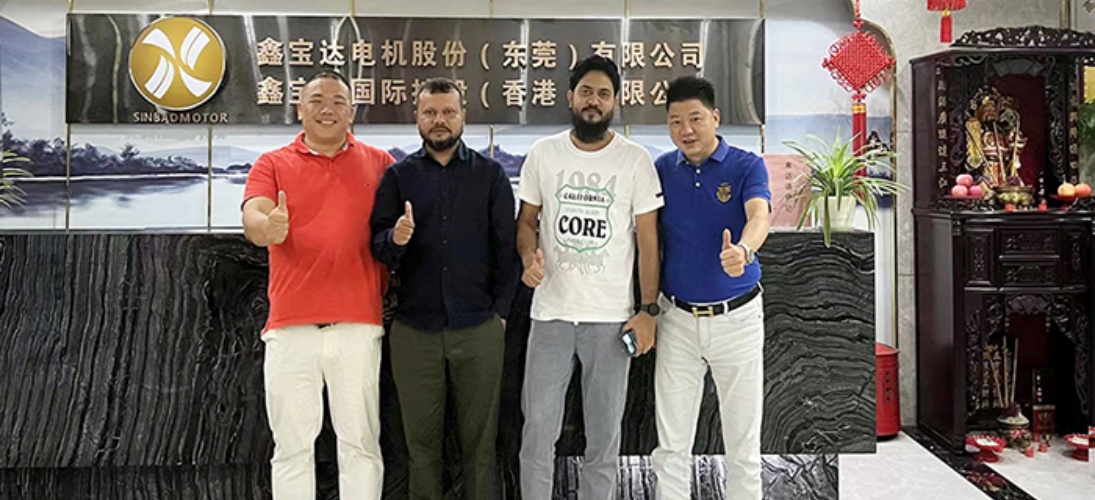
Service
Professional technical support
Our technical service team consists of a group of engineers with deep expertise and rich practical experience in the field of electrical machinery. They are familiar with the principle and structure of the hollow cup brush motor, whether it is the electromagnetic design of the motor, the hollow cup characteristics of the rotor, or the complex interaction between the brush and the commutator, they can be accurately analyzed. Whether it is a simple fault consultation or a complex technical problem, our engineers have the expertise to quickly provide accurate and effective solutions.