After Sales - Services


Company Infomation
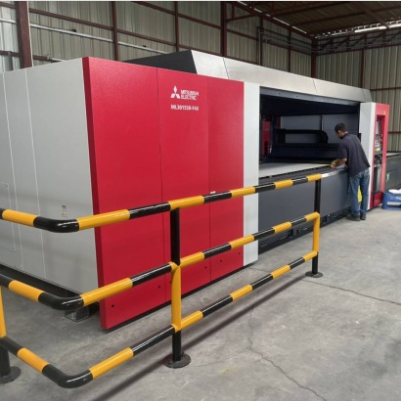
We are fully equipped to provide high-quality services with tools and equipment such as laser machines, bending machines, rolling machines, punching machines, lathes, welding machines, and other essential tools. Our team of experienced and skilled technicians is ready to deliver fast and efficient service, whether for factory work, large-scale projects, or urgent tasks. Meeting our customers' needs is a top priority, particularly in terms of quality and production timelines.
We offer marking, laser cutting of metal, laser engraving, and laser cutting on various materials such as steel, stainless steel, and galvanized metal, using high-performance Mitsubishi CNC Laser Cutting Machines. We accept urgent orders, large volumes, and no minimum order requirements, providing step-by-step guidance throughout the production process to ensure that the work meets the exact specifications and quality desired by our customers. We guarantee precision in every order.
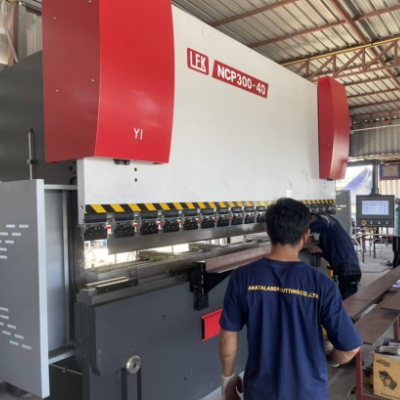
Company Case
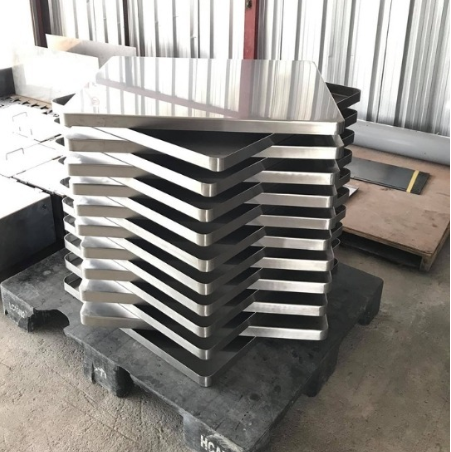
Design and Programming
- CAD Design: The box is designed using computer-aided design (CAD) software, specifying the dimensions, features, and tolerances.
- Laser Cutting Program: The design is then converted into a laser cutting program (G-code) to guide the CNC laser cutting machine.
Laser Cutting
- Material Preparation: A metal sheet (usually steel, stainless steel, or aluminum) is selected and positioned on the laser cutting machine bed.
- Laser Cutting: The CNC laser cutting machine uses a high-powered laser to precisely cut the metal sheet along the design lines. The laser melts, burns, or vaporizes the material to create clean, precise cuts. It can cut complex shapes, holes, and edges with high accuracy and minimal waste.
Sheet Bending (Optional)
- Bending: After cutting, the individual parts of the box (such as side panels, top, and bottom) are bent into the desired shapes using a CNC press brake or other bending equipment, if necessary.
Welding
- Assembly: The cut and bent metal parts are arranged and aligned to form the shape of the box.
- Welding: The parts are welded together using a welding process such as MIG (Metal Inert Gas), TIG (Tungsten Inert Gas), or spot welding, depending on the material and design. This process fuses the edges of the metal sheets to create strong, permanent joints.
- Finishing Welds: Any excess weld material is cleaned up, and the welds are smoothed for a neat finish.
Post-Processing
- Surface Treatment: The welded box may undergo additional surface treatments like powder coating, painting, or galvanizing for corrosion resistance and improved aesthetics.
- Inspection: The final product is inspected for dimensional accuracy, weld quality, and overall finish.
Final Assembly and Packaging
- The finished metal box is inspected for quality control, and any additional components (like screws or hinges) are added. It is then ready for shipment or further industrial use.
This process allows for the efficient production of custom metal boxes with high precision and strength, suited for various industrial applications.
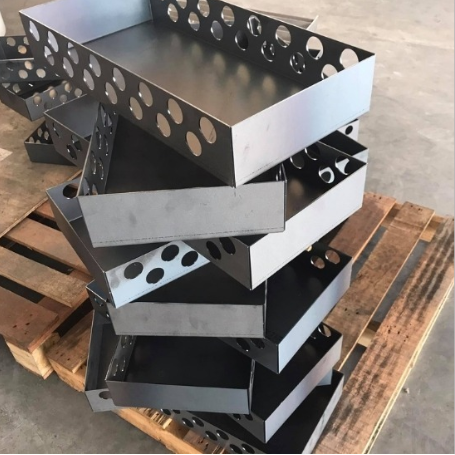
Our Services
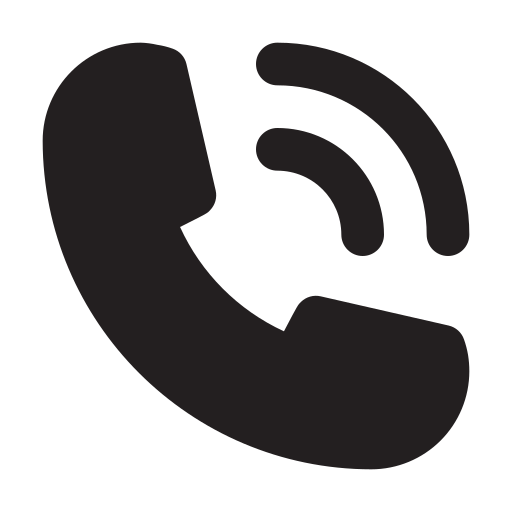
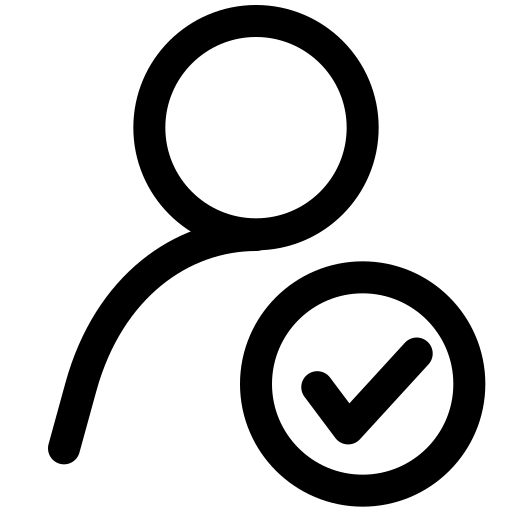
Warranty
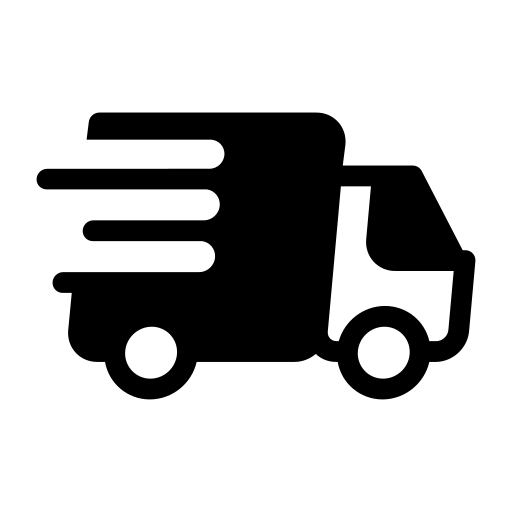
Transportation Service
Cooperative partner
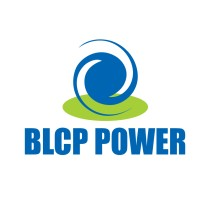
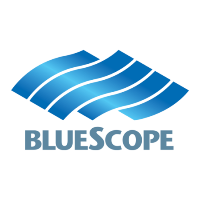
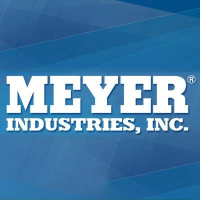
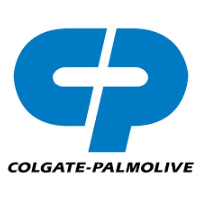
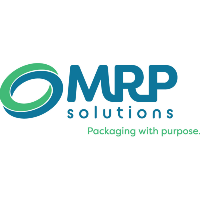