24 hours online customer service


Company Infomation
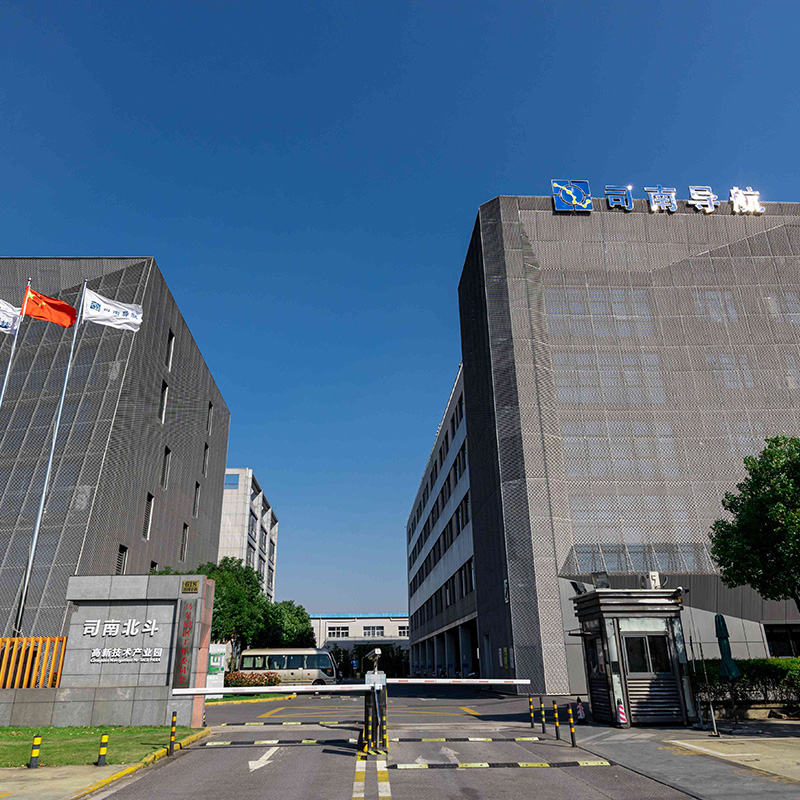
Company overview
Sinan Navigation integrates the great achievements of China's high-precision GNSS technology, has a local R & D team specializing in high-precision GNSS core technology for many years, and more than 40 main technical backbone has won provincial and ministerial science and technology awards. Under the leadership of industry leader Dr. Wang Yongquan, Sinan Navigation has broken many foreign technical barriers, broken through the key technical bottlenecks of high-precision GNSS core algorithms, chips, boards, receivers, applications and industrialization, and developed a number of mature high-precision multi-mode and multi-frequency GNSS boards and receivers, filling the gaps in the field of high-precision GNSS at home and abroad for several times. At the same time, it is also the first satellite navigation enterprise that truly realizes the industrial application of Beidou in China.
Following the trend of compatibility and interoperability of the world's four major satellite navigation systems, Sinan Navigation flexibly meets the differentiated needs of users in different industries. Its business covers traditional surveying and mapping, geographic information, intelligent transportation, fine agriculture, machinery control, safety engineering, industrial measurement and other high-precision application fields, and its sales network covers more than 20 countries and regions around the world.
Sinan Beidou Industrial Park, with a total construction area of about 26,000 square meters invested by Sinan Navigation, is planned to be officially put into use in 2015, as the main research and development, production and application center of Beidou high-precision GNSS board in China, and will become a Beidou industrialization base that drives Shanghai, radiates the whole country and affects the world.
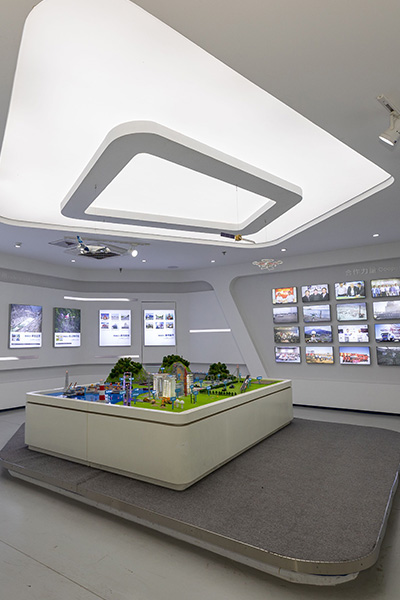
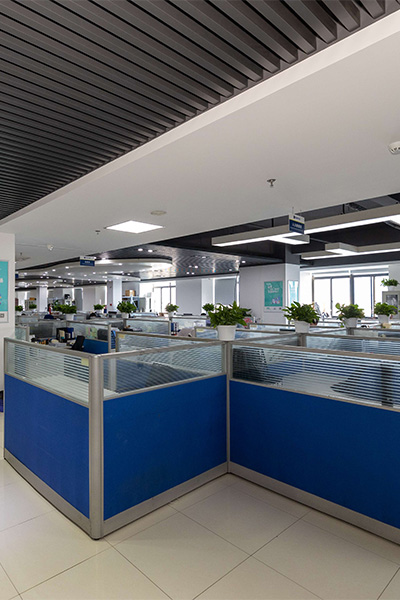
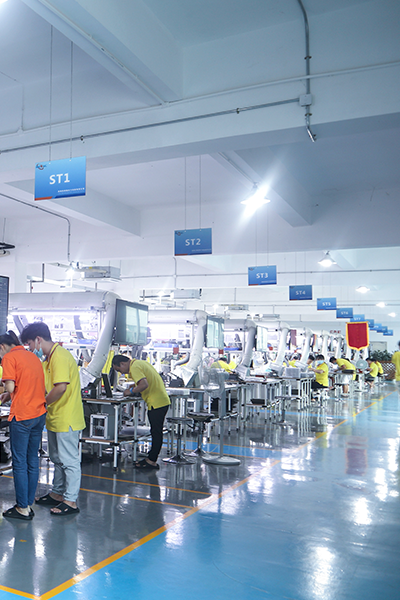
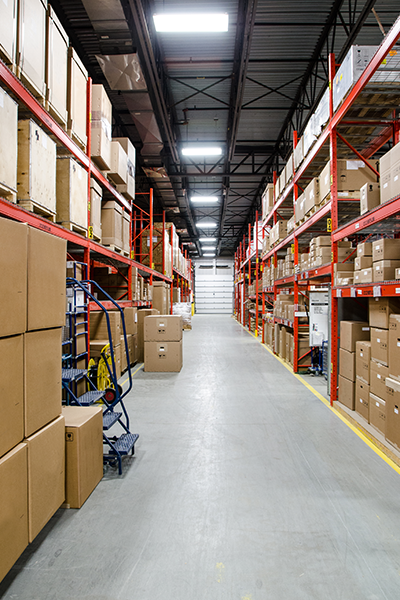
Company Certificate
Company Case
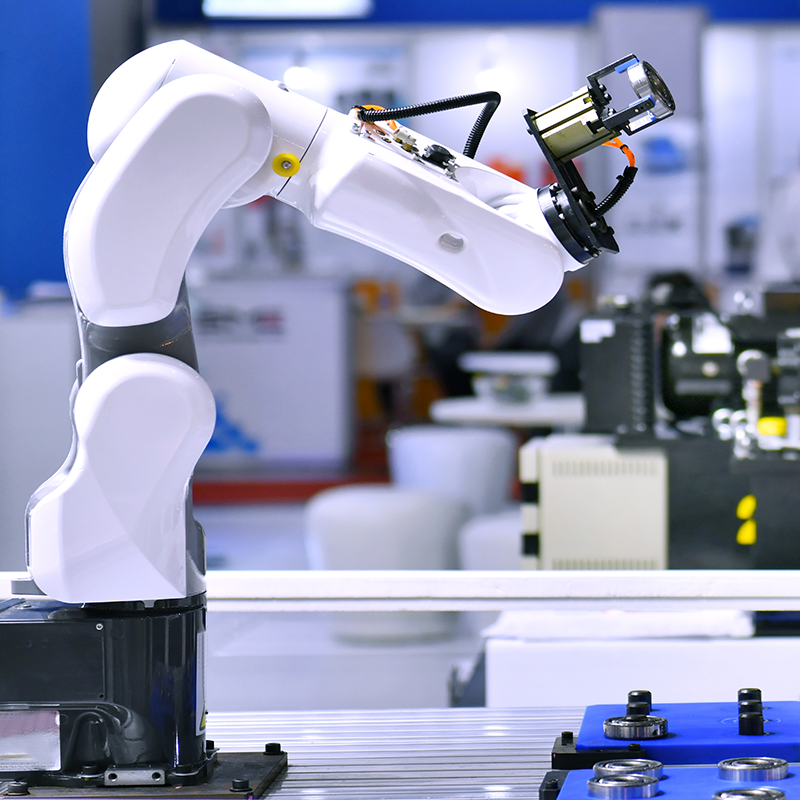
Mechanical control
Case:
In the automotive production line, the robotic arms used for automotive body welding need to complete complex welding tasks with high precision. For example, in the production workshop of a well-known automobile brand, the robot arm undertakes the work of accurately welding the body parts together, completing hundreds of welding operations every day, and the position accuracy and welding quality of the welding contact are extremely high.
Working mode:
The robotic arm is equipped with a navigation module based on LiDAR and a joint encoder. The LiDAR scans the work area in real time, creating a high-precision three-dimensional map that accurately identifies the position and attitude of the body parts. The joint encoder precisely measures the rotation Angle and displacement of each joint of the manipulator and feeds back to the control system. When receiving the welding task instruction, the control system calculates the motion trajectory of each joint of the robot arm through kinematic algorithm based on the data of LiDAR and joint encoder, guides the welding tool at the end of the robot arm to reach the welding point accurately, and performs welding operations according to the preset welding parameters and paths to ensure the stable and reliable quality of each welding point. The error is controlled within the millimeter level, thus ensuring the overall structural strength and safety of the car body.
Intelligent robot (track chassis as an example)
Case:
In the mine mining scenario, an intelligent robot for ore transportation uses a tracked chassis design to drive autonomously on complex and rugged mine roads, transporting mined ore from the mining area to the designated stacking site. For example, in a large open-pit iron mine, this intelligent robot effectively improves the efficiency of ore transportation, reducing labor costs and transportation risks.
Working mode:
The robot's track chassis is equipped with a variety of navigation devices, including inertial navigation system (INS), global Positioning System (GPS) and vision sensors. The inertial navigation system uses gyroscope and accelerometer to monitor the robot's attitude and acceleration changes in real time, and calculates its own position and driving direction. GPS provides the approximate position information of the robot in the global coordinate system, which is used to correct the accumulated error of the inertial navigation system. Vision sensors collect and analyze images of the surrounding environment to identify features such as road boundaries, obstacles and target stacking areas. During the driving process, the robot's control system uses advanced path planning algorithms, such as A * algorithm or Dijkstra algorithm, according to the data provided by these navigation modules to plan an optimal driving path from the current position to the target position. At the same time, by adjusting the speed and steering Angle of the track in real time, the robot can drive stably along the planned path, automatically avoid obstacles, and successfully complete the ore transportation task. Even in the harsh conditions such as dust and turbulence in the mining environment, it can maintain high positioning accuracy and driving stability, and the positioning error is usually within a few meters, meeting the actual needs of mining operations.
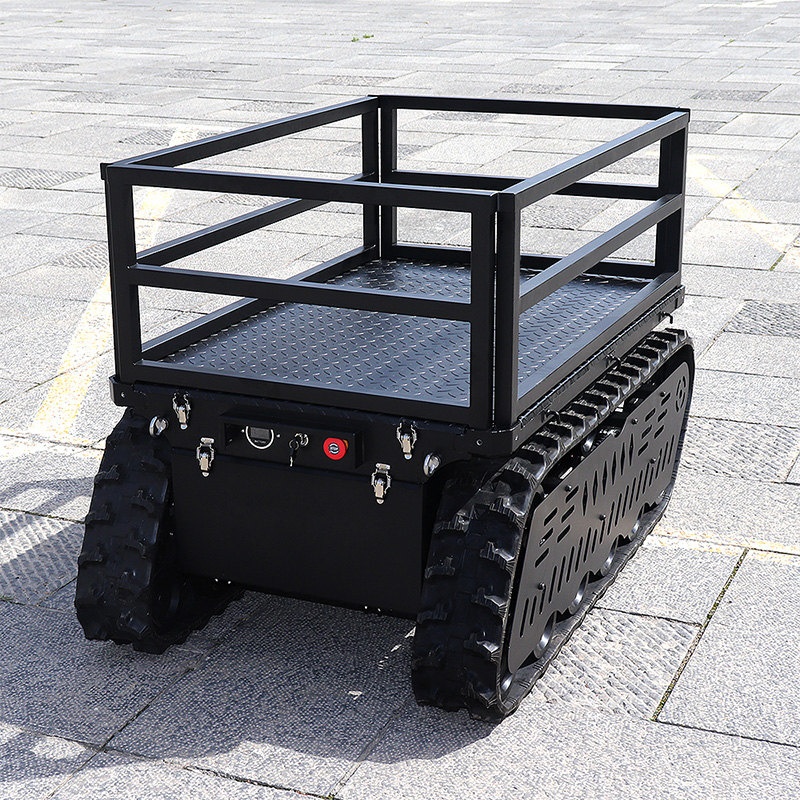
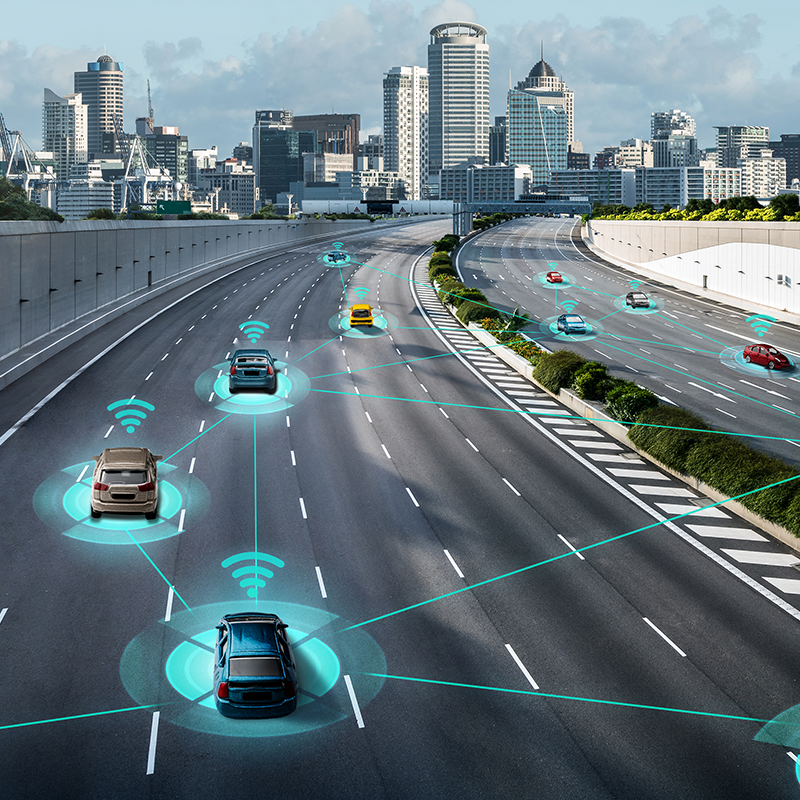
Intelligent driving (car driverless)
Case: Driverless cars are tested and operated on urban roads to provide travel services for residents, increase mileage and improve safety, and can cope with complex urban traffic scenarios.
Working mode: The car is equipped with LiDAR, millimeter wave radar, camera, GPS and high-precision map equipment. Laser radar constructs three-dimensional point cloud map to measure object information; Millimeter wave radar monitors speed and distance; The camera uses deep learning algorithm to identify traffic elements; GPS location, high precision map provides road details. During driving, the control system integrates sensor data to sense the environmental state, uses decision-making algorithms (rules or machine learning), and controls the power, steering and braking systems through ECU to achieve automatic driving. If the red light is stopped in advance, the intersection can be accurately controlled, the driving compliance can be improved, and the travel experience and technology development application can be improved.
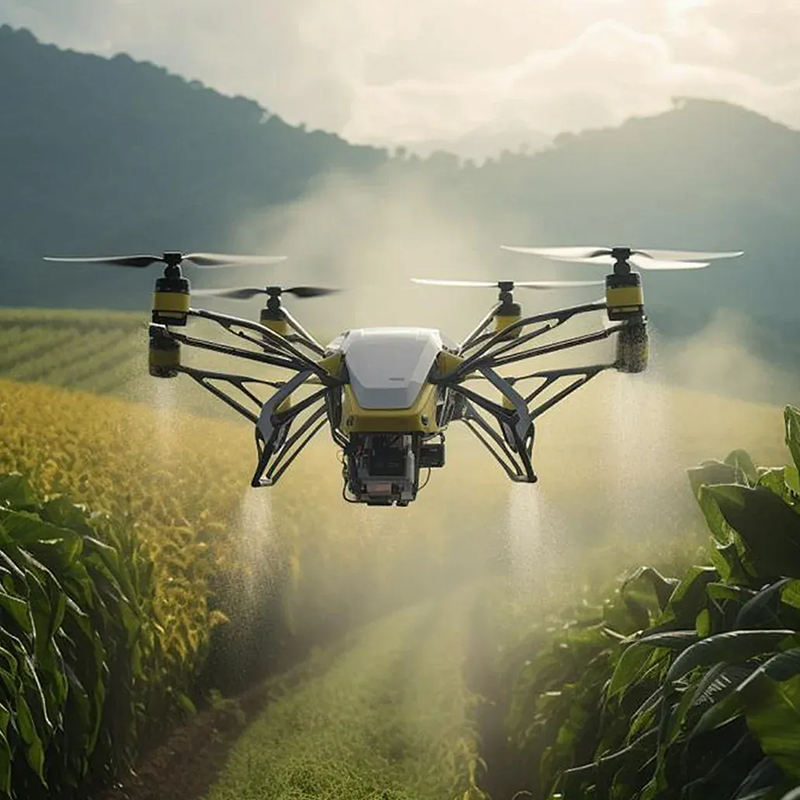
drone
Case: DJI's agricultural plant protection drones fully demonstrate the importance of navigation modules in farm operations.
Working mode: These drones use a combination of GPS navigation and visual navigation. Before the operation, the operator plans the operation area and flight path of the farmland on the map through the ground control station. After the UAV takes off, the navigation module guides the UAV to fly according to the scheduled route according to the satellite positioning information. At the same time, the visual navigation system uses the camera to capture ground images, identify and locate crop rows in the field, further correct the flight path, ensure the stability and accuracy of the UAV in the flight process, so that pesticides or fertilizers can be evenly and accurately sprayed on the crops, improve agricultural production efficiency, reduce labor intensity and cost. And reduce the waste of pesticides and environmental pollution.
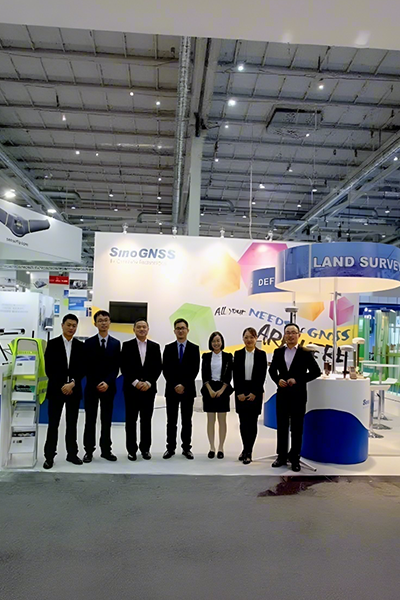
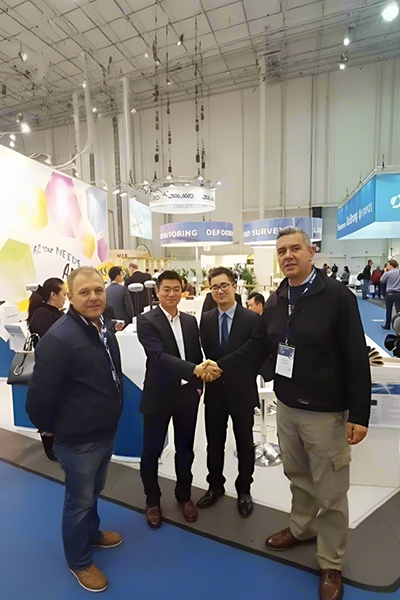
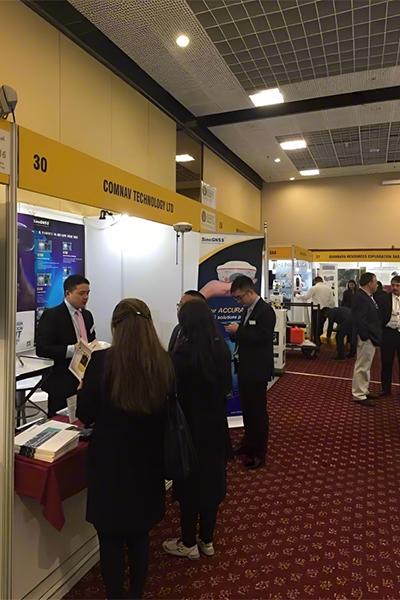
Our Products
Our Services
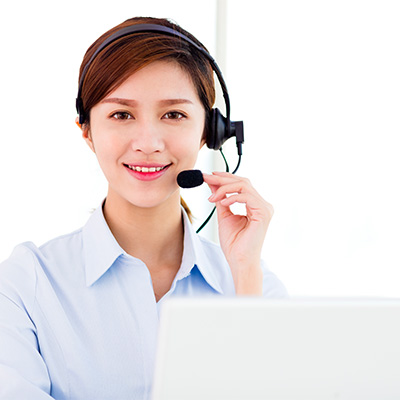
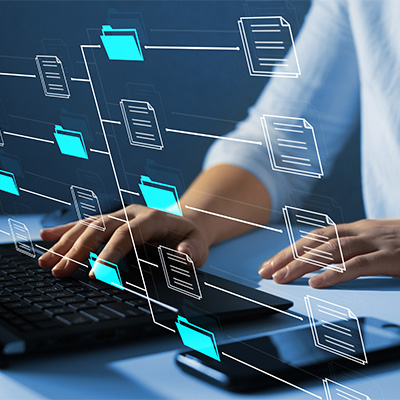
Professional technical support
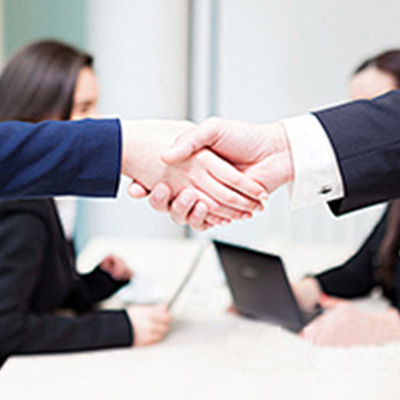
Honesty and win-win cooperation
Cooperative partner
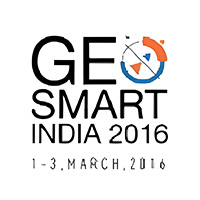
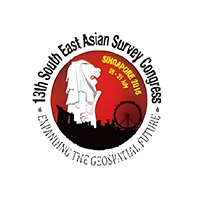

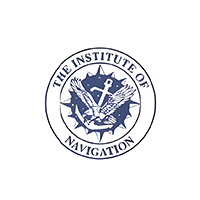

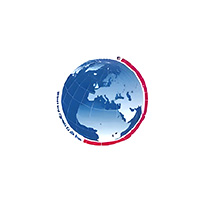
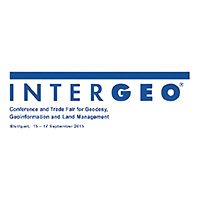
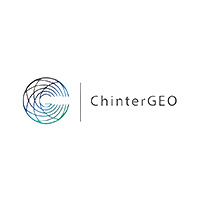
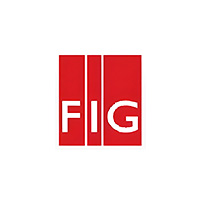
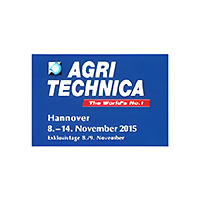