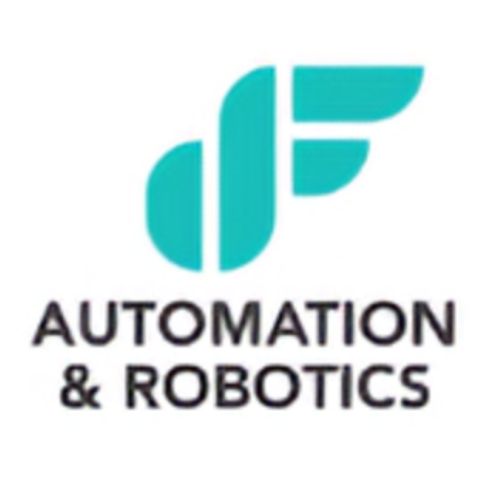

Company Infomation
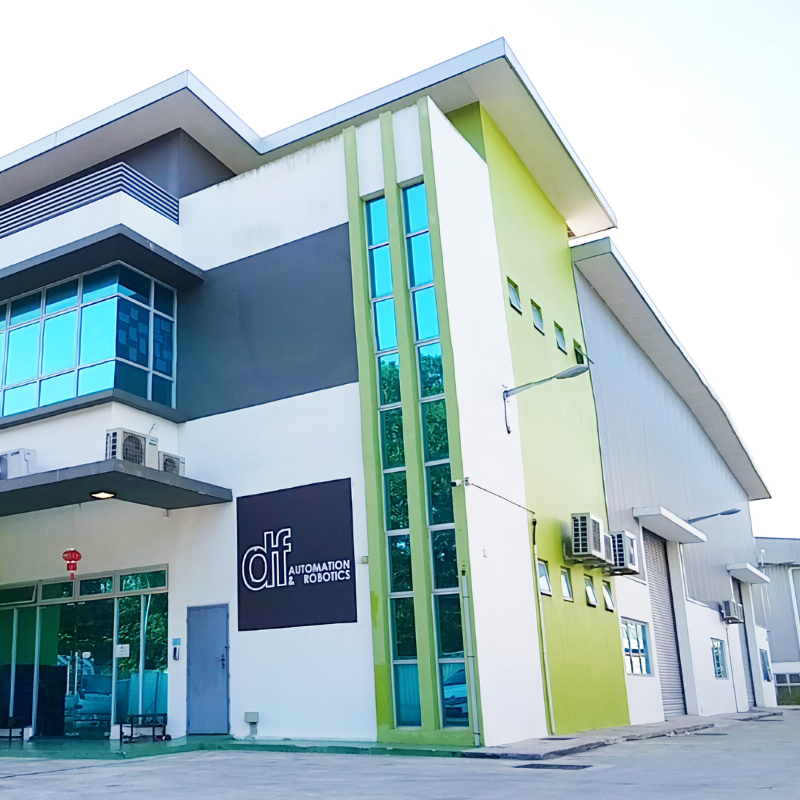
DF Automation Robot (DF) is a pioneering Malaysian company founded by a group of dedicated Malaysians, committed to advancing the global automation and robotics landscape. The company specializes in designing, manufacturing, and deploying Autonomous Mobile Robots (AMRs) and Automated Guided Vehicles (AGVs). These innovative robots are engineered to solve key challenges in industries ranging from manufacturing to logistics, healthcare, retail, and beyond. DF’s robots play a vital role in helping businesses increase production capacity, improve accuracy, boost efficiency, and minimize downtime. By leveraging automation, DF helps customers significantly reduce operational costs, leading to a more competitive and streamlined operational environment. The company’s cutting-edge solutions are not only transforming industries but also providing businesses with the tools to excel in an increasingly fast-paced, automated world.
DF’s commitment to continuous innovation is evident in its extensive Research and Development (R&D) efforts. The company is focused on advancing its robotics solutions to keep pace with the evolving demands of the global market. By integrating both track-based and trackless laser-guided navigation systems, DF offers a highly flexible range of products that can be adapted to the unique needs of its clients. In addition to this, DF emphasizes customization to address specific challenges faced by its customers. Whether it’s overcoming complex logistical obstacles or streamlining production processes, DF works closely with its clients to provide tailored solutions that enhance overall performance and operational efficiency. This proactive approach to problem-solving ensures that DF’s robots are not just tools, but intelligent solutions that evolve with the specific requirements of each customer.
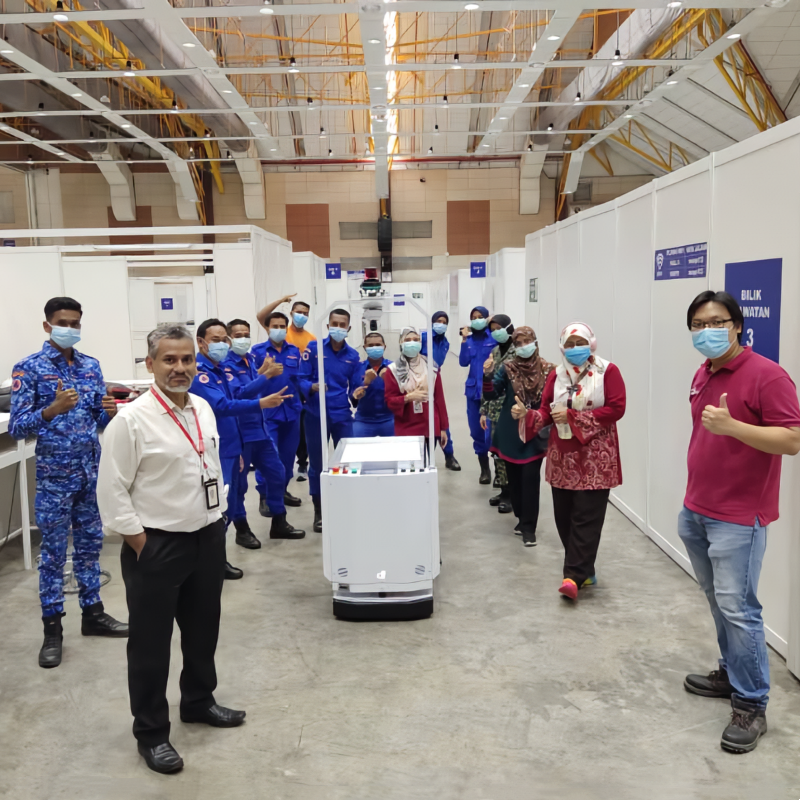
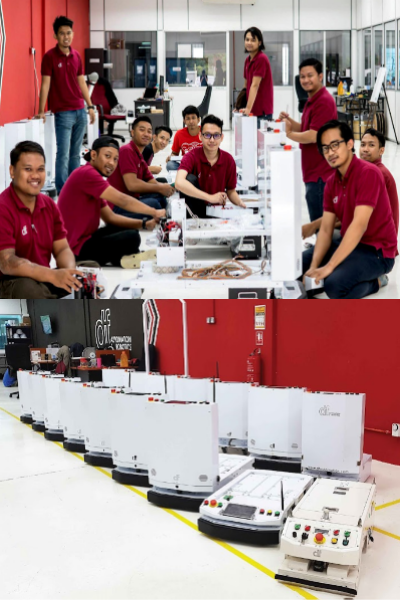
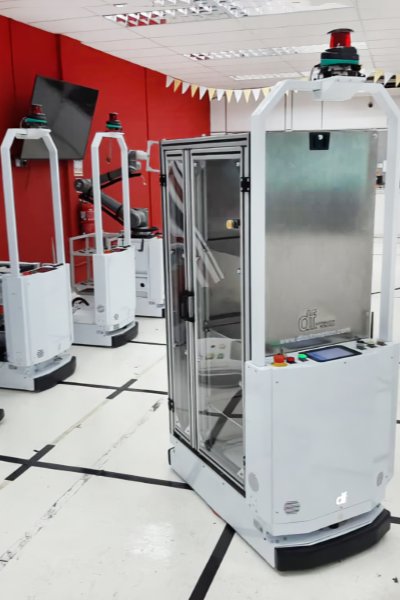
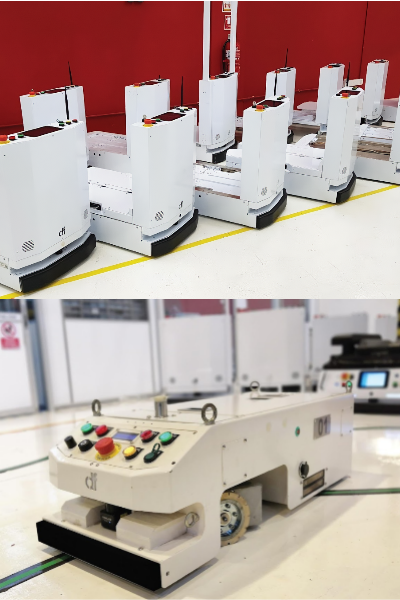
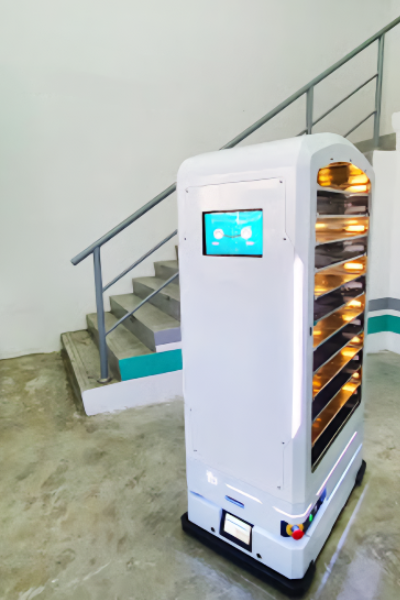
Company Certificate
Company Case
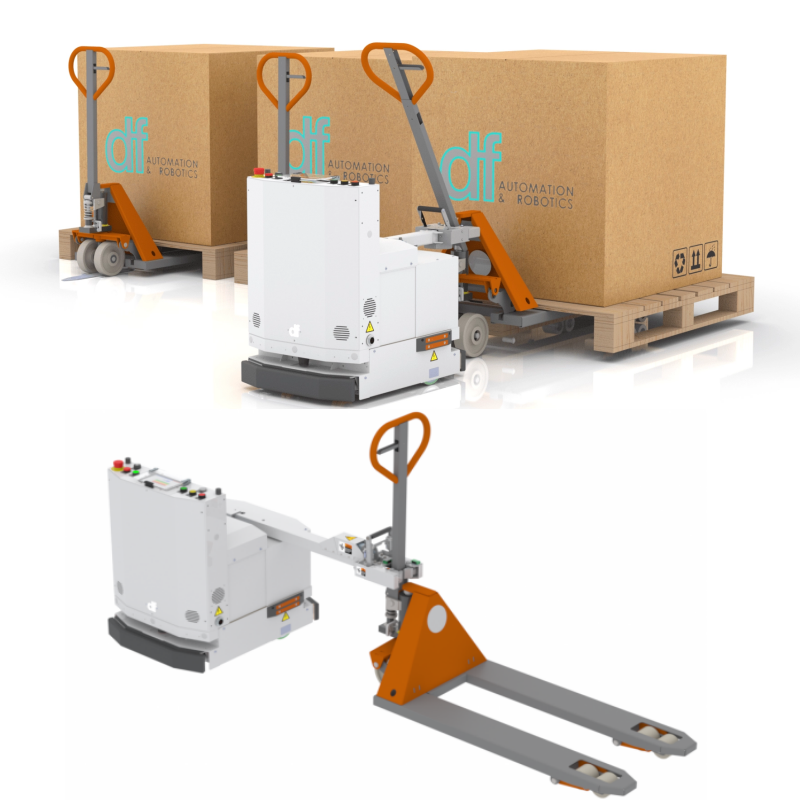
Automated Pallet Jack Transferring Zalpha Standard with Towing Clamp
2021.12.31
One 3C manufacturing company, which specializes in consumer electronics and other similar products, is seeking an automation solution to optimize the transportation of finished goods from the production line to the packaging stations, with minimal disruption to their existing operations. The challenge lies in efficiently moving products, each weighing up to 300kg, without requiring significant modifications to the current production infrastructure. To streamline the process, the company envisions a system that integrates a button-type call button with Remote I/O, which would allow workers to easily summon an automated vehicle or robot to transport the goods between the two critical areas. This solution would not only reduce the reliance on manual labor but also improve overall efficiency by eliminating unnecessary delays and ensuring that goods are moved swiftly and safely from production to packaging, ready for shipment with greater consistency and reliability.
Previously, they are sending their finish goods pallet using manual pallet jack. This led to several issues such as:
lShortage of manpower
lUnattended Finish Goods to be send to packaging station
lPotential of Finish Goods damaged during the transfer
After implementing the AMR system, customer only require to put the Finish Goods with Pallet Jack at predefined station and call for the AMR using a call button for automatic delivery to the packaging station.
Automated Pallet Transferring Zalpha Lowbed with Lifter
2022.1.3
One plastic pallet manufacturer has significantly enhanced its production process by installing the Zalpha Lowbed with Lifter system, an advanced automation solution, to transport pallets from the production line to the packaging station. This move is aimed at reducing reliance on manual labor, improving overall efficiency, and addressing workplace safety concerns. By incorporating this automobile robot system, the company can now automate the previously labor-intensive task of transferring finished pallets, thus minimizing the need for human intervention. As a result, the process becomes more streamlined, with tasks performed more quickly and consistently. The reduction in human involvement also lowers the likelihood of workplace injuries associated with manual handling and forklift use.
The Zalpha Lowbed with Lifter utilizes a precise linear actuator mechanism to transfer pallets from the molding machine to a designated platform for further processing. This automation ensures that pallets are transported with speed and accuracy, significantly improving throughput in the manufacturing process. The pallets are stacked on the platform, and the system is designed to manage the height of the stacks. Once the pallets reach a predetermined height, a limit switch is triggered, signaling the completion of the task and prompting the next steps in the workflow. This level of automation not only boosts efficiency but also eliminates potential errors that could occur if the process were still carried out manually.
The installation of the automobile robot into the production line represents a major leap forward in optimizing production operations. With no manual labor required for the transfer of pallets, the process becomes more reliable and cost-effective over time. Additionally, this system reduces the risks typically associated with transporting heavy pallets using forklifts, such as collisions or accidents. By automating the pallet transfer, the manufacturer creates a safer, more efficient work environment where employees can focus on higher-value tasks while the robotic system handles the heavy lifting. Ultimately, this innovation not only enhances productivity but also ensures that the company can meet increasing demand with greater consistency and reliability.
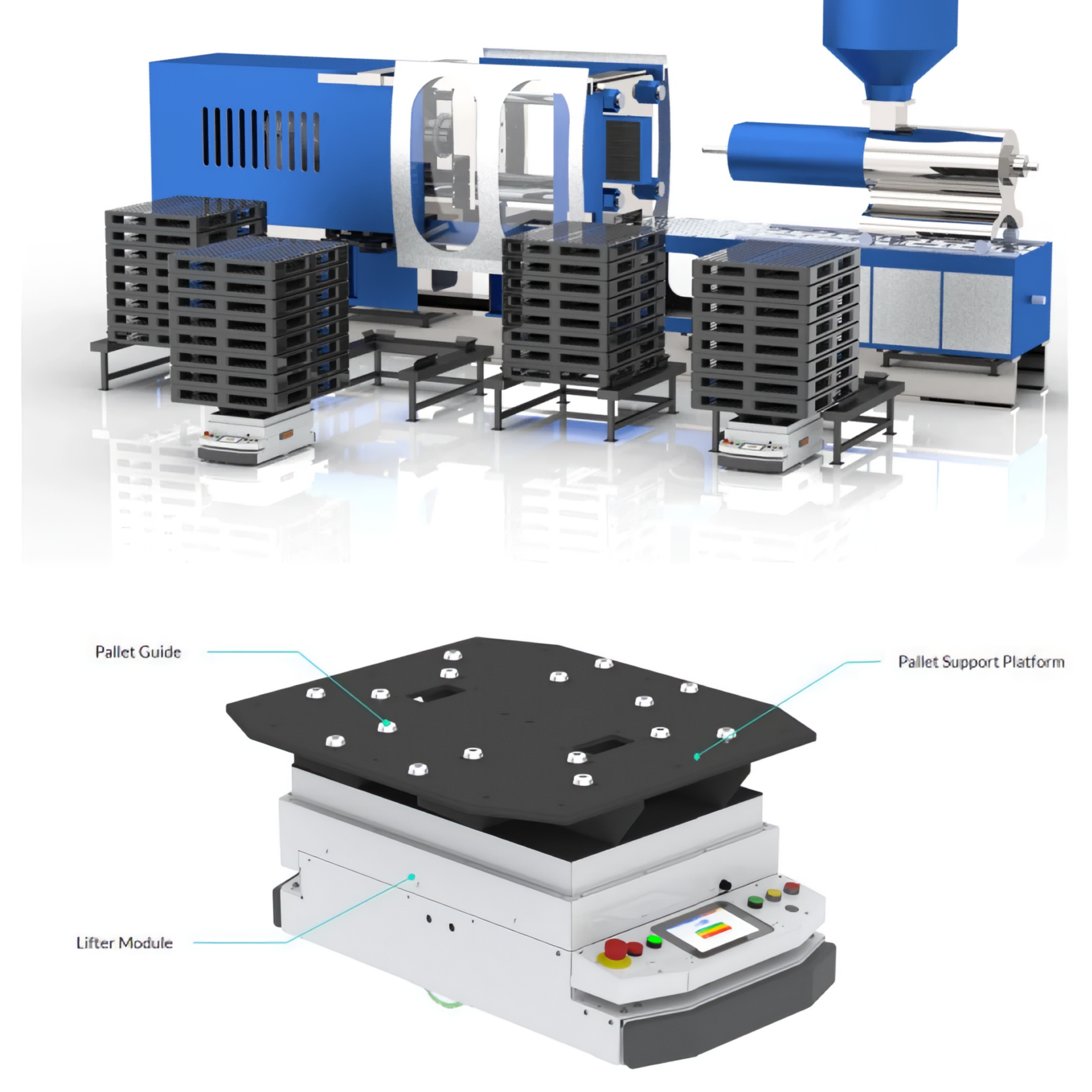
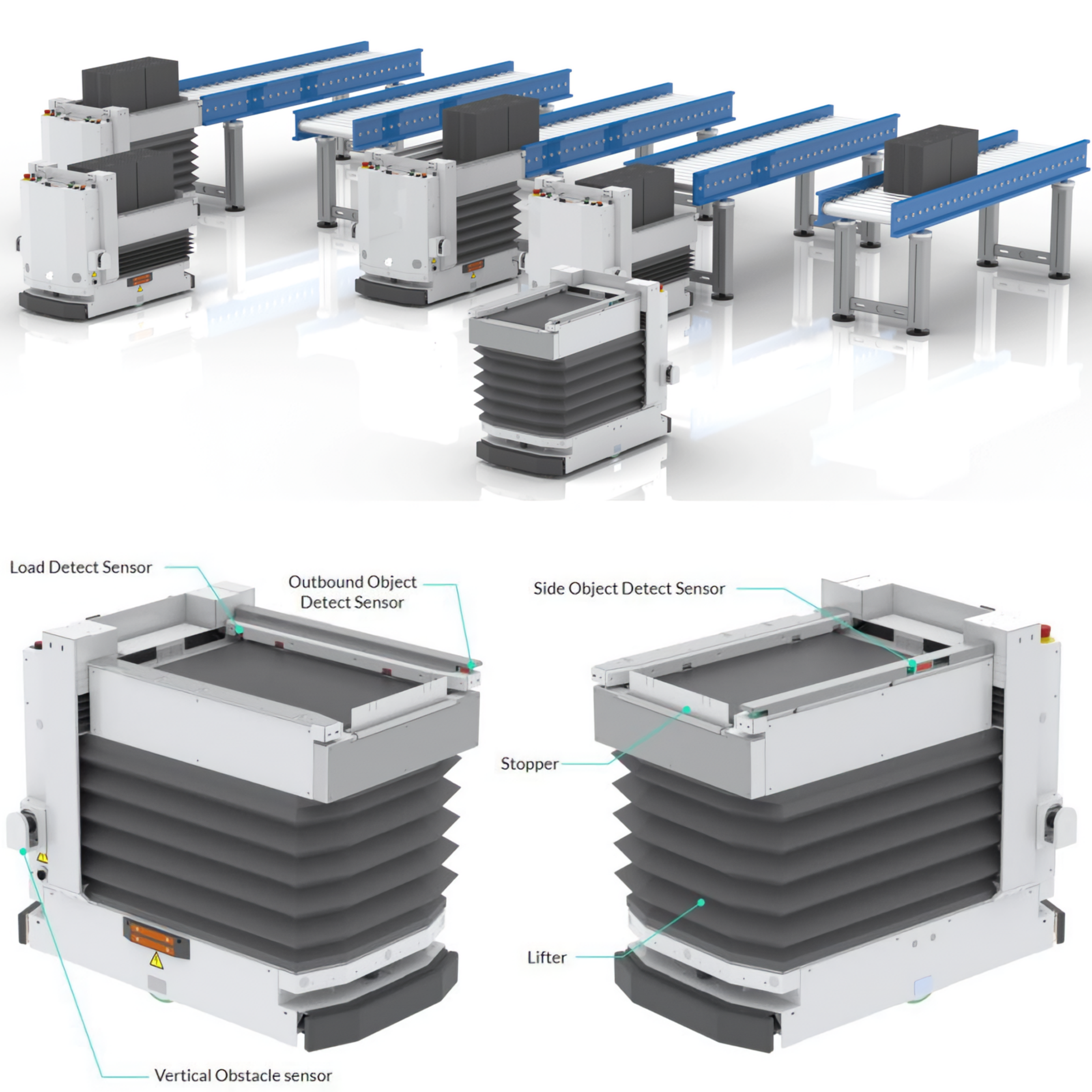
Automated Magazine Transferring Zalpha Extend with Lifter Conveyor
2022.1.6
One semiconductor manufacturer integrated the Zalpha autonomous mobile robots (AMRs) extended with conveyor lifters into their production line to streamline operations and reduce reliance on human labor. These robots are specifically designed to transport IC trays—used for inspection, transport, and shipping of semiconductor packages—between different stations in the clean room. By automating this process, the manufacturer was able to reduce the number of personnel required in these critical areas. This not only increased operational efficiency but also minimized the risk of contamination in the clean room, which is essential for maintaining the high-quality standards of semiconductor production.
With the introduction of these AMRs, the customer was able to optimize their workforce.
l By cutting down on manual labor in the clean room, employees could be redirected to more value-added tasks, contributing to overall productivity gains.
l The automation of the IC tray transportation process freed up personnel to focus on higher-level responsibilities, improving the workflow and reducing the potential for human error.
l In addition, the integration of conveyor lifters with the robots enabled smoother material handling, ensuring that the entire production line ran more seamlessly and with minimal disruption.
This transformation not only improved efficiency but also supported a safer and more hygienic working environment.
Our Products
Cooperative partner
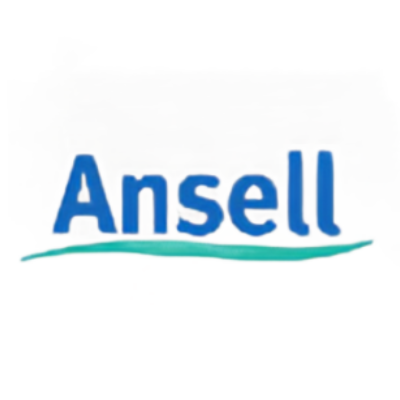
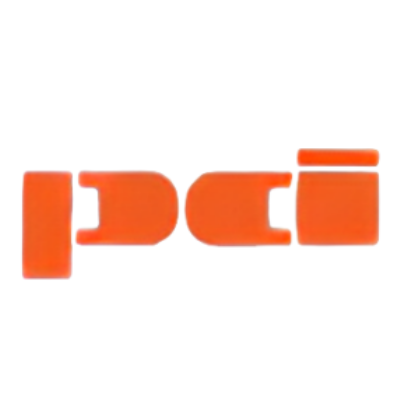
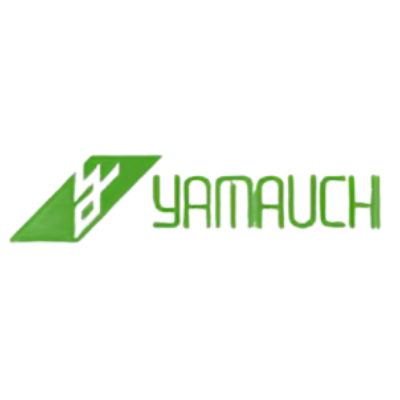
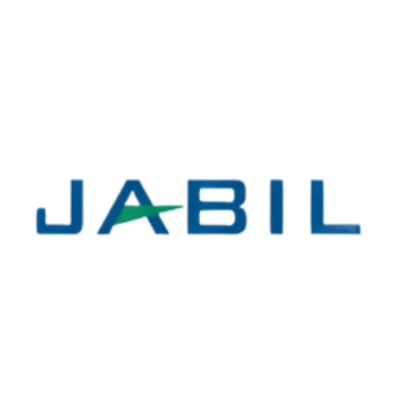
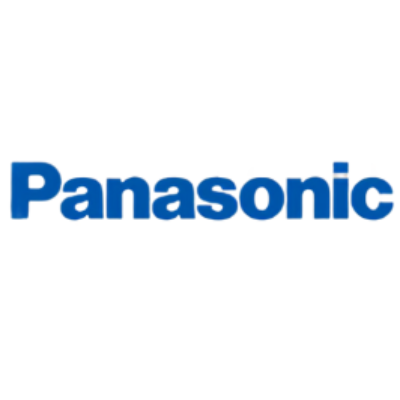