Product Description
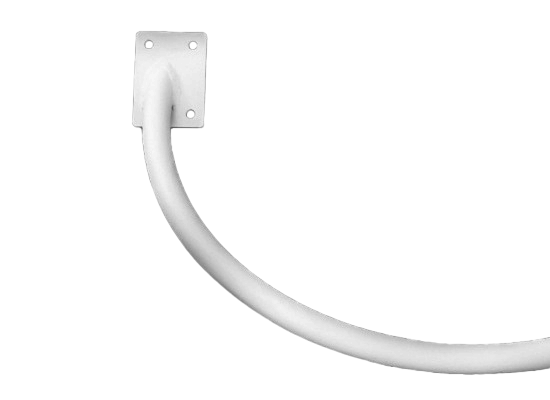
Welding is a process that permanently connects metal or thermoplastic materials through heating, pressurization or both. It includes arc welding, gas welding, laser welding and other methods. It is widely used in mechanical manufacturing, construction, automobiles, aerospace and other fields. It is characterized by high efficiency and firmness, but attention should be paid to deformation and safety hazards.
Preparation before welding
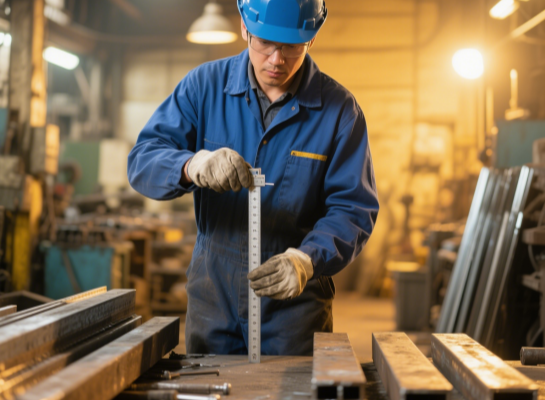
Material inspection
Confirm the model, thickness, and surface condition (no rust, oil, moisture, etc.) of the parent material (welded material).
Check whether the welding materials (electrodes, welding wires, flux, etc.) meet the process requirements.
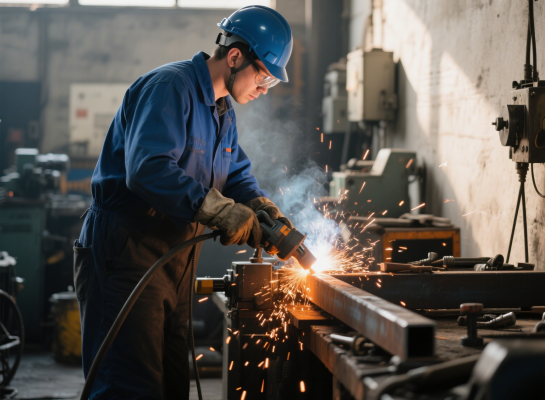
Groove processing
Process the groove (such as V-shaped, U-shaped, X-shaped, etc.) according to the thickness and welding method to ensure penetration and reduce welding stress.

Cleaning treatment
Remove oxides, oil stains and other impurities on the surface of the parent material with a grinding wheel, wire brush or chemical cleaning.
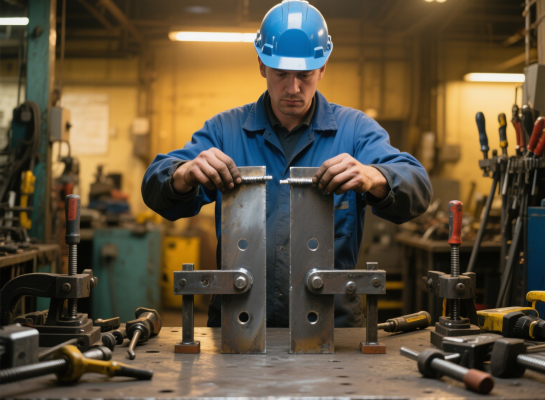
Assembly and fixing
Fix the workpiece with a clamp or spot welding (positioning welding) to ensure that the butt gap and misalignment meet the standards.
Production equipments
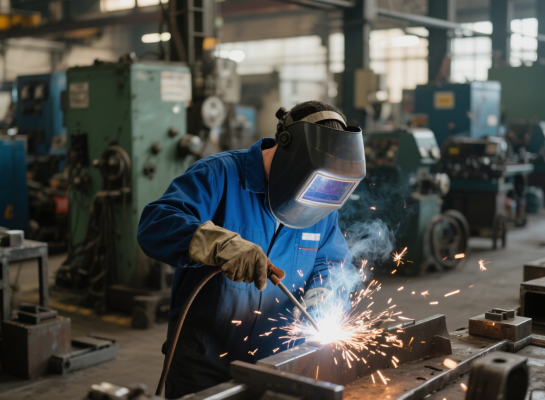
SMAW (manual arc welding): uses coated electrodes to melt metal through arc, suitable for a variety of materials, simple equipment, suitable for outdoor and maintenance welding, dependent on welder skills, low efficiency.
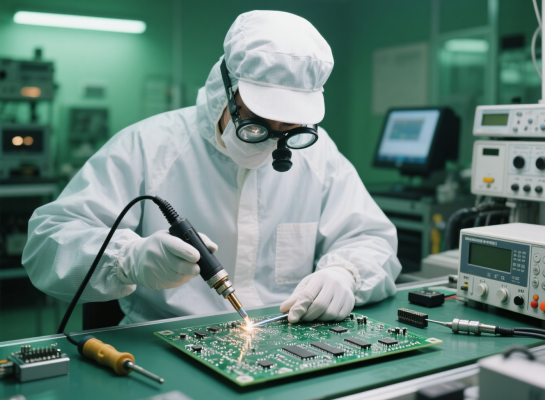
TIG welding (tungsten inert gas welding): uses non-consumable tungsten electrode, inert gas to protect the weld, suitable for high-precision welding of stainless steel, aluminum, etc., with pure and beautiful welds.
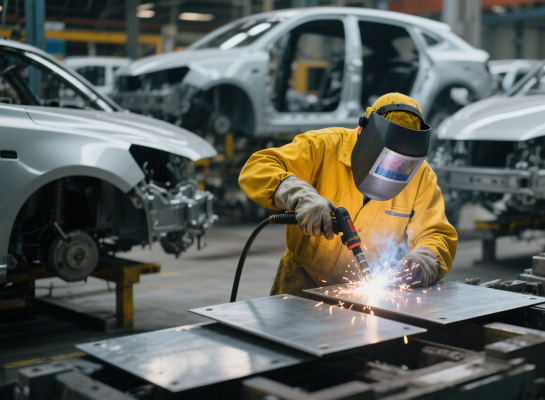
CO₂ shielded welding (MAG welding) uses CO₂ gas to protect the molten pool, and the welding wire is automatically fed. It is suitable for carbon steel and low alloy steel welding, efficient and energy-saving, and suitable for automated production.
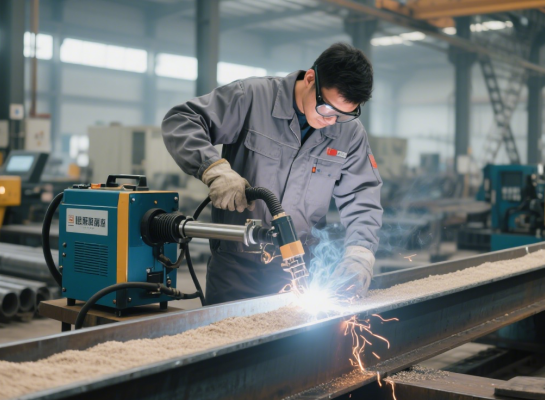
Submerged arc welding (SAW) is an efficient and automated welding method. The flux covers the arc, suitable for thick plates and long welds, with a high deposition rate and no spatter. It is mainly used in shipbuilding and pressure vessel manufacturing
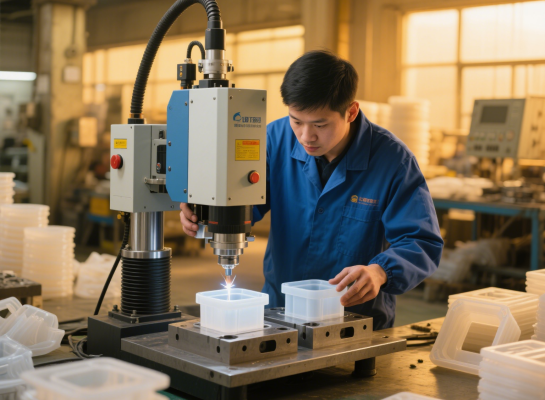
Ultrasonic welding: Use high-frequency vibration friction to generate heat to achieve non-melting welding and quick connection of plastic or metal sheets. No solder is required, energy-saving and efficient, and suitable for precision electronics and packaging industries.
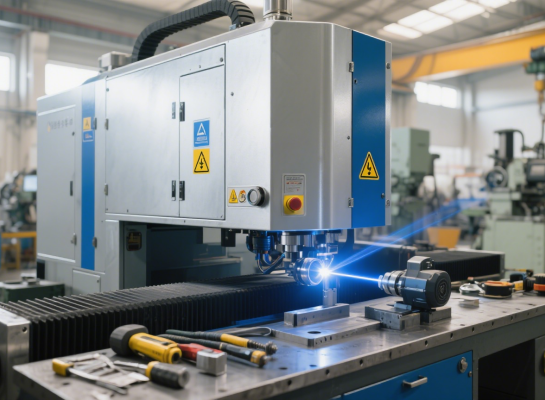
Laser welding equipment: uses high-energy laser beams to accurately weld metals, with high precision and low heat-affected zone, suitable for automated processing and widely used in electronics, automobiles and precision manufacturing industries.
Application
Welded parts are widely used in many fields. In the construction industry, steel beams in bridges and building structures are connected by welded parts to ensure overall stability. In mechanical manufacturing, various mechanical frames and parts are welded to give the equipment complete functions. In the automotive industry, body frame welding ensures safety and structural strength. In the aerospace field, high-precision welded parts are used in aircraft manufacturing to meet stringent performance requirements. In life, tables, chairs, kitchen utensils, etc. are also full of welded parts, providing convenience and support for daily life.
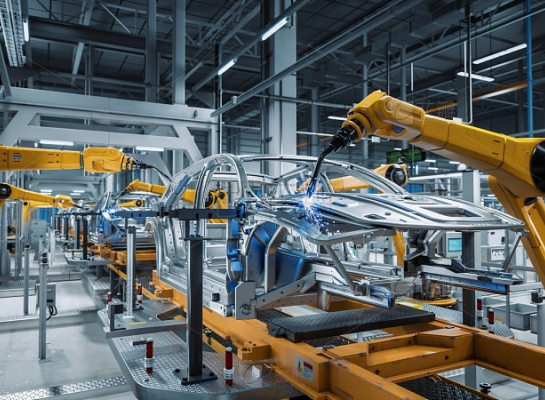
Automobile
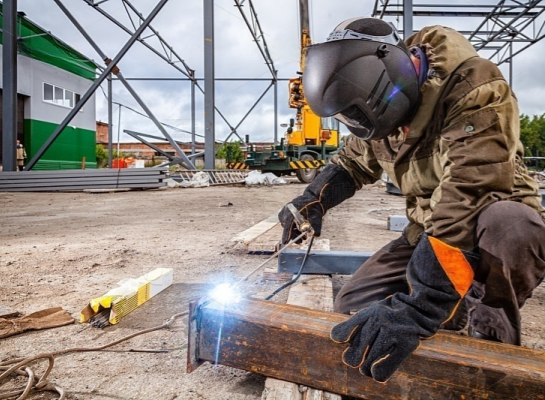
Construction
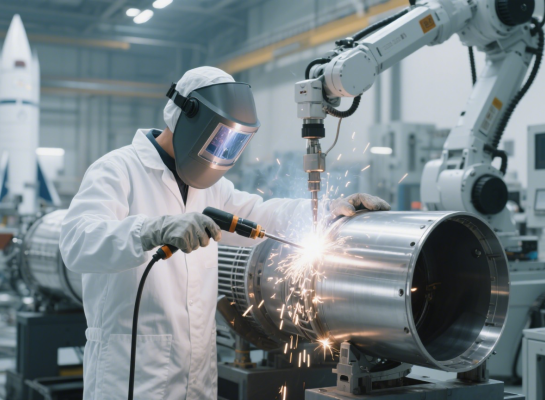
Aerospace
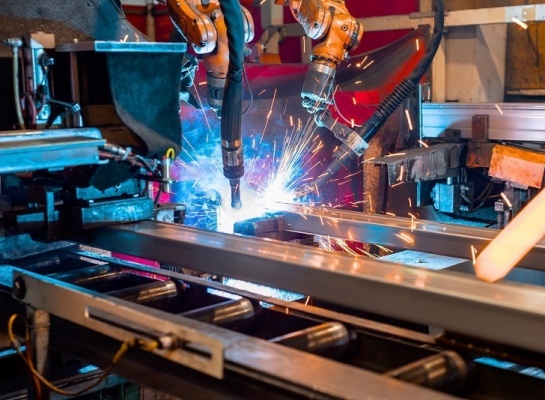
Equipment manufacturing
Product parameters
Production Technique | SMAW (manual arc welding) |
TIG welding (tungsten inert gas welding) | |
CO₂ shielded welding (MAG welding) | |
Submerged arc welding (SAW) | |
Ultrasonic welding | |
Laser welding | |
Raw Material | Stainless Steel,Carbon Steel,Aluminum Alloy,Titanium Alloy,Zinc Alloy, Copper Alloy, Plastic etc |
Inspection Equipment | Infrared thermal imager |
Laser 3D scanning | |
Ultrasonic detector | |
Industrial endoscope | |
X-ray flaw detector |
Material
Customized product materials: Stainless Steel, carbon Steel, Aluminum Alloy, Titanium Alloy, Zinc Alloy, Copper Alloy, Plastic etc.
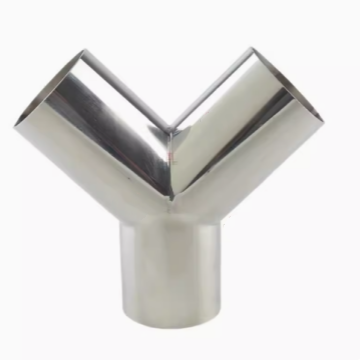
Stainless steel
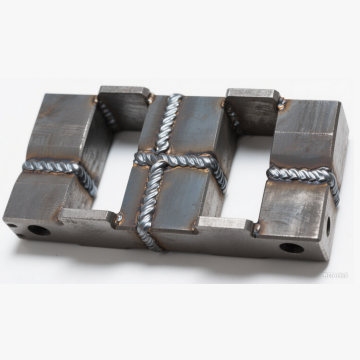
Carbon Steel
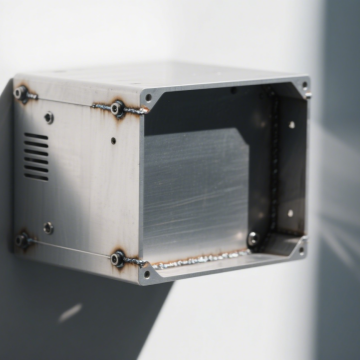
Aluminum Alloy
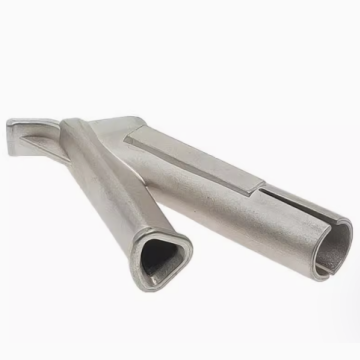
Titanium Alloy

Zinc Alloy
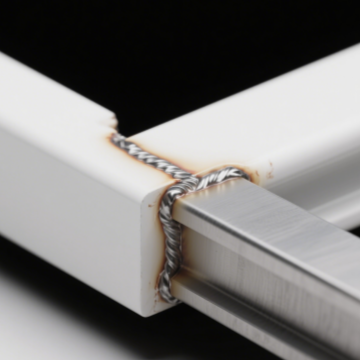
Plastic
Custom Process
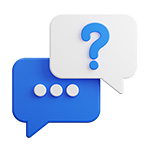
1. Send inquiries
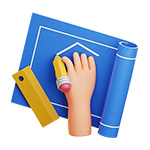
2. Drawing or samples
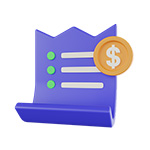
3. Quotation
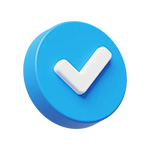
4. Customer confirmation
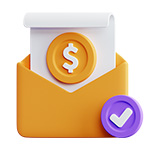
5. Places order and pays
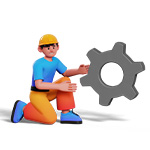
6. Mass production
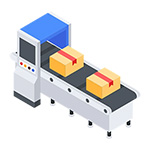
7. Test before packing
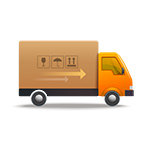
8. Shipping & confirmation
Quality Control
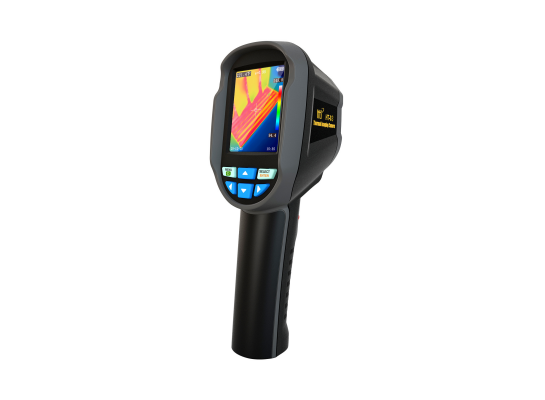
Infrared thermal imager
The infrared thermal imager performs quality inspection by capturing the difference in thermal radiation in the welding area. During the inspection, the instrument collects the temperature field distribution of the weld and the surrounding area in real time, and compares it with the normal welding heat conduction law, which can quickly identify defects such as incomplete penetration, poor fusion, and cracks. The defective area presents abnormal temperature color blocks due to abnormal thermal resistance. The inspection process is non-contact and visual, which can intuitively locate the hidden danger points and provide real-time thermal data basis for welding quality assessment.
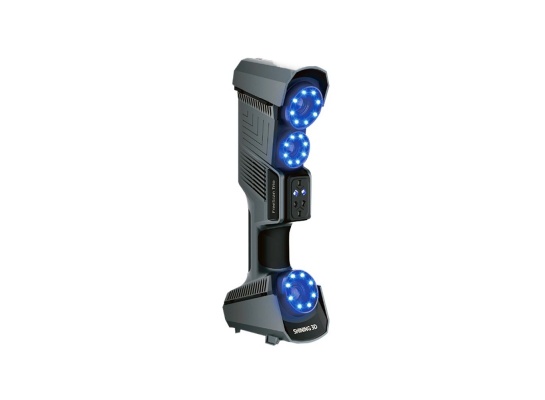
Laser 3D scanning
The laser 3D scanner scans the welding part by emitting a laser beam, captures the surface geometric information and constructs a 3D model. The system compares the preset standard data in real time, accurately detects the weld shape, dimensional deviation, surface defects and other problems, and locates and marks defects such as undercuts, pores, and incomplete penetration. The inspection is high in accuracy and speed, providing reliable data support for welding quality control.
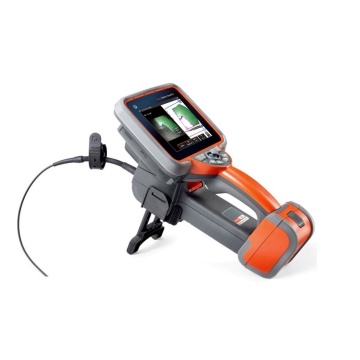
Ultrasonic detector
The ultrasonic detector emits high-frequency ultrasonic waves to the weld, and judges the quality by analyzing the time, amplitude and waveform of the reflected echo. It can accurately detect internal defects such as pores, slag inclusions, cracks, and lack of fusion, locate the position and size of defects according to the echo characteristics, with high detection sensitivity and strong penetration, providing reliable data for the internal quality assessment of welds.
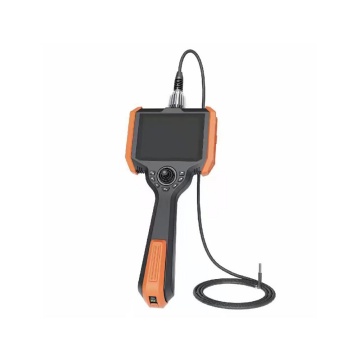
Industrial endoscope
The industrial endoscope penetrates deep into the weld or complex structure through the probe, and uses optical or electronic imaging technology to transmit the image of the detection area to the display terminal. The inspector can directly observe the surface cracks, lack of fusion, weld nodules and other defects of the weld, and accurately locate the subtle hidden dangers with the help of lighting and magnification functions, so as to achieve non-destructive and visual close-range quality assessment.
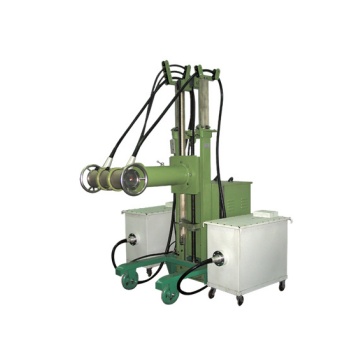
X-ray flaw detector
The X-ray flaw detector emits X-rays to penetrate the weld, and uses the difference in the absorption of rays by different materials to form an image. After the film or detector receives the transmitted rays, the internal defects such as pores, slag inclusions, cracks, and lack of penetration of the weld are displayed through images, and the nature and location of the defects are judged based on the image characteristics. The detection results are intuitive and accurate, which is an important means of internal quality inspection of welds.
Stock
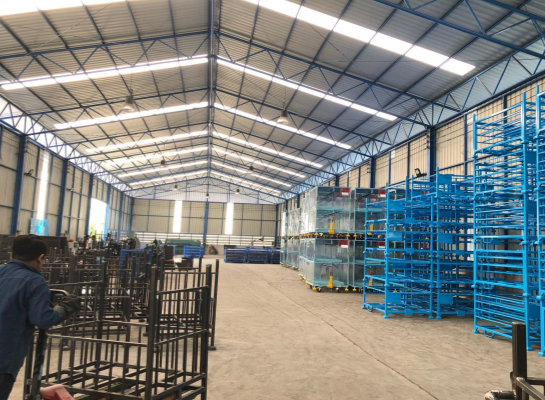
