Product Description
EX single-coil S series has multiple optional models: S4-3, S6-7, S6-40, S8-25; rated torque range: 1.5N.m~10N.m. High speed, high dynamic response and high torque density. Suitable for robotic arms/humanoid robots/exoskeleton robots/quadruped robots/RGV, etc.
Adopting advanced high-purity bearing steel, the bearing life is up to 80%, and it can withstand high temperatures of 200 degrees. It provides host computer parameter adjustment/testing/firmware upgrade, real-time data reading control, simple and easy to use, and supports microprocessor to send commands directly.
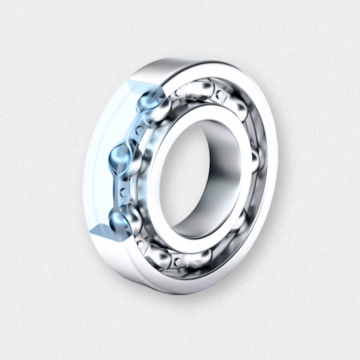
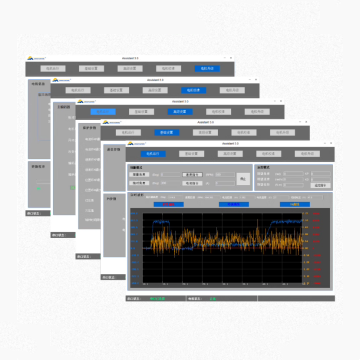
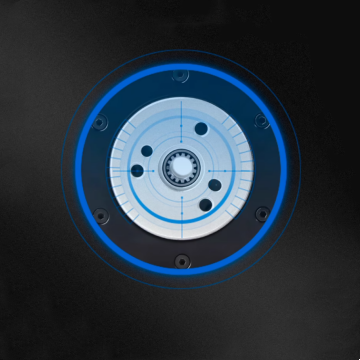
Functional Features
Supports installation of a second encoder
Higher control accuracy
The second encoder records the absolute position
The first encoder records the multi-turn position
No need to worry about the angle changing again after power failure
Suitable for robot arm application scenarios
High-density brushless motor
Safe, quiet and precise control
Adopt the latest MC-100 drive, compact and powerful
Application
The EX single-branch series planetary reduction module adopts a compact planetary gear structure with high torque density, low backlash (≤1 arc minute) and excellent impact resistance, and is suitable for precision transmission scenarios with limited space. It is widely used in industrial robot joints, collaborative robotic arms, 360° cameras, pod PTZs, and filming to achieve high-precision positioning and smooth power transmission. Its modular design supports rapid integration, adapts to servo/stepper motors, and significantly improves the dynamic response and energy efficiency of equipment, especially suitable for lightweight and high-load automation needs.
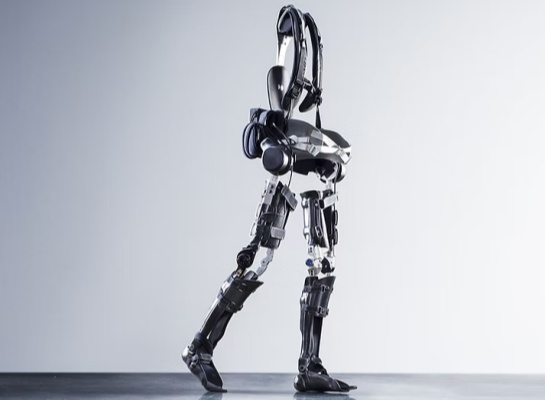
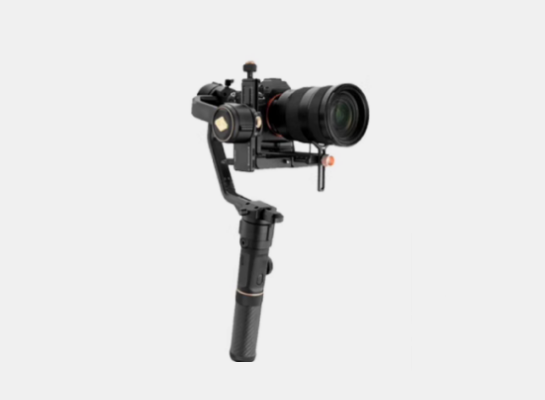
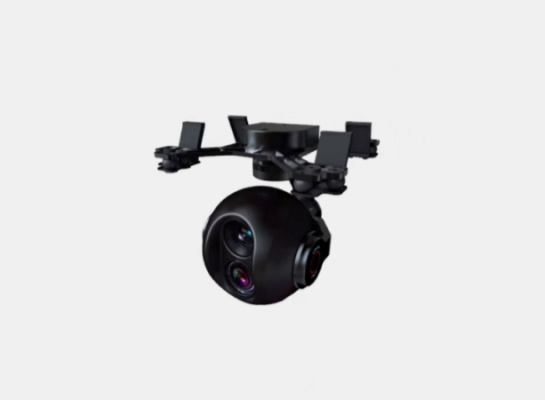
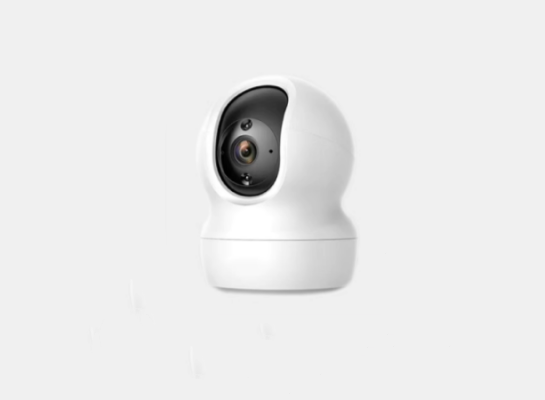
Product parameters
1. The standard motor does not support brakes, which can be customized if needed.
2. The standard motor does not support waterproofing, which can be customized to IP54 if needed.
3. The standard motor supports CAN BUS and RS485.
Parameters | Unit | S 4-3 | S 6-7 | S 6-40 | S 8-25 |
Reduction ratio | 一 | 6 | 6 | 36 | 9 |
Input voltage | V | 24 | 48 | 48 | 48 |
Rated speed | RPM | 200 | 400 | 90 | 110 |
Rated torque | N.m | 1.5 | 3.5 | 18 | 10 |
Rated power | w | 30 | 150 | 170 | 125 |
Rated current | A | 2 | 4 | 5.2 | 3.2 |
Peak torque | N.m | 3 | 7 | 40 | 25 |
Peak current | A | 4 | 9 | 10.5 | 8 |
Efficiency | % | 60 | 70 | 70 | 80 |
Number of pole pairs | 一 | 14 | 14 | 14 | 21 |
Back drive torque | N.m | 0.06 | 0.08 | 0.91 | 0.61 |
Backlash | Arcmin | 10 | 10 | 15 | 10 |
Axial load | N | 300 | 775 | 775 | 985 |
Radial load | N | 550 | 1250 | 1250 | 1250 |
Moment of inertia | Kg.cm² | 1.2 | 4.8 | 28.8 | 30.6 |
Encoder type | bit | 18 | 18 | 18 | 18 |
Communication method | 一 | CAN:1M/RS485:115200/500K/1M/2.5M | |||
Weight | kg | 0.3 | 0.35 | 0.59 | 0.71 |
Rated torque test method:
When the ambient temperature is 24 degrees Celsius (no other heat dissipation methods), the test is performed at the rated speed. The motor torque reaches temperature balance under the condition of a temperature rise of 60 degrees Celsius, and the long-term working point is the rated torque value of the motor.
Installation diagram and motor characteristic diagram
EX S-4-P6-3-X-N
EX S-6-P6-7-X-N
EX S-6-P36-40-X-N
EX S-8-P9-25-X-N