Product Description
Precision-engineered for durability and performance, the Cosmic Series Metal Stamping Shrapnel delivers advanced mechanical reliability for a wide range of electronic, automotive, and industrial applications. Crafted from high-quality stainless steel or custom alloy materials, this stamping component is designed to provide consistent elasticity, conductivity, and resistance to wear—even under extreme operating conditions.
Flat Spring Shrapnel (Cosmic-FS) | Dome Shrapnel (Cosmic-DS) | Type 3: Contact Shrapnel (Cosmic-CS) |
Functional Features
Material Options | Stainless steel, phosphor bronze, beryllium copper, and other alloys |
High Precision | Tolerances as tight as ±0.01mm for demanding design requirements |
Resilient Performance | Excellent spring-back characteristics for repeated use |
Corrosion-Resistant | Protective surface treatments available (plating, passivation, etc.) |
Customizable | Tailored shapes, sizes, and finishes to suit your design |
Product Display
Application
Connectors and terminals | Battery contacts and shields | Switches, sensors, and relay systems |
Automotive electronics | Aerospace components | Smart devices and wearable tech |
Product parameters
Parameter | Flat Spring (Cosmic-FS) | Dome (Cosmic-DS) | Contact (Cosmic-CS |
Material | Beryllium Copper / Bronze | Stainless Steel (301/304) | Copper Alloy / Tin Steel |
Thickness | 0.05 – 0.3 mm | 0.05 – 0.15 mm | 0.1 – 0.5 mm |
Width / Diameter | Custom (3 – 30 mm typical) | 4 – 15 mm (typical dome) | Custom (2 – 25 mm typical) |
Hardness | HRC 35 – 45 | HRC 40 – 50 | HRC 30 – 42 |
Surface Finish | Nickel / Tin / Gold Plated | Bright / Matte / Plated | Nickel / Gold / Tin Plated |
Tensile Strength | ≥ 600 MPa | ≥ 800 MPa | ≥ 400 MPa |
Operating Temperature | -40°C to +150°C | -20°C to +125°C | -40°C to +200°C |
Conductivity | High | Medium | High |
Tolerances | ±0.01 – ±0.05 mm | ±0.02 mm | ±0.03 mm |
Custom Process
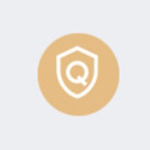
QUESTION
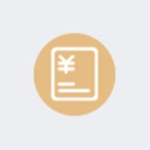
NEGOTIATION
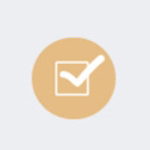
CONFIRM
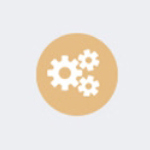
PRODUCTION
Quality Control
1. Incoming Material Inspection
Material Certification Review: Verify composition (e.g., Cu, Sn, Be content) per supplier CoA
Hardness Testing: Using Rockwell or Vickers scale
Surface Quality: Check for oxidation, scratches, or surface defects
Thickness & Flatness Check: Micrometer/gauge verification
2. In-Process Inspection
Stamping Accuracy Check: Ensure tolerance within ±0.01–0.05 mm
Burr & Edge Inspection: Optical or manual visual check to ensure safe, smooth edges
Dimensional Control: 100% sampling for high-tolerance parts using calipers or automated vision systems
Tool Wear Monitoring: Periodic check of die condition and wear marks
3. Surface Treatment Inspection
Plating Thickness Test: XRF (X-ray fluorescence) test for gold, tin, or nickel coatings
Adhesion Test: Tape or bending test to verify coating adherence
Corrosion Resistance Test: Salt spray test (ASTM B117 standard)
4. Final Product Inspection
Functional Testing: Conductivity, spring-back force, and insertion/removal force
Tactile Feedback Test: (For dome-type) Actuation force, rebound speed
Full Visual Inspection: 100% visual check for cracks, deformation, or discoloration
Packaging QC: Quantity, lot number, label accuracy, and ESD-safe packaging verification
5. Documentation & Compliance
Inspection Records: Maintained per ISO 9001:2015 or IATF 16949
RoHS / REACH Compliance Reports: Provided upon request
PPAP / FAI Reports: Available for OEM/automotive projects
SPC Charts: For critical dimension tracking
Service
FAQ
1. What materials are available for your metal stamping shrapnel?
We offer a wide range of materials including stainless steel (301, 304), beryllium copper, phosphor bronze, and custom copper alloys. Surface treatments such as nickel, gold, or tin plating are also available.
2. Can I request a custom design or shape?
Yes. We provide custom stamping services based on your drawings or technical requirements. We support prototyping, tooling, and full-scale production.
3. What is the typical tolerance you can achieve?
Our precision stamping process allows for tolerances as tight as ±0.01 mm, depending on the part geometry and material.
4. What are the typical applications for these shrapnel components?
Common uses include:
Battery contacts
Switches and keypads
PCB terminals
Automotive sensors
Consumer electronics
Smart devices
5. Are your products RoHS and REACH compliant?
Yes. All materials and finishes used comply with RoHS and REACH environmental standards. Certifications can be provided upon request.