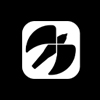

Fruit and vegetable picking robot
Agricultural picking robot robotic arm fruit and vegetable picking and handling robot customization
- Motor Power:2*600W
- Load:200kg
- Navigation accuracy:±20 mm
- Maximum travel speed:1m/s
- Working life:3h
- Remote control distance:100m
USD: Price Inquiry
ablity:Monthly Output200
- Product Description
- Product Params
Product Description
Fruit and vegetable picking robot
The fruit and vegetable picking robot is a highly collaborative automated system that integrates artificial intelligence and multi-sensor technology and uses a deep learning-based vision algorithm to guide the robotic arm to complete identification, positioning, grabbing, cutting, and placement tasks. It can solve the problem of fruit and vegetable selectivity under natural conditions. Harvest problem is an iconic product of smart agriculture.
The fruit and vegetable picking robot consists of a chassis system, a visual servo system and a picking execution system. The chassis system adopts wheel-type and track-type crawler type composite traveling mechanisms based on the road conditions, which can adapt to the planting scenarios of greenhouse hardened roads, tracks, and outdoor ground. Among them, the track-type chassis adopts dual steering wheels combined with track wheel traveling mechanism to meet various facility agricultural application scenarios such as smooth road surface, automatic rail loading and unloading, automatic rail changing, etc. It uses a laser SLAM algorithm and combines a variety of sensors to make it more suitable for high-end facility greenhouse environments; the visual servo system uses AI+ deep stereo vision recognition technology to achieve information acquisition and processing of tomato size, color, shape, maturity and picking location. processing, and at the same time, through real-time planning and obstacle avoidance of the robotic arm's motion trajectory, the trajectory guidance of visual servo picking is completed; the picking execution system uses a 6-degree-of-freedom cooperative robotic arm combined with a lifting column and chassis to complete the task through reasonable picking posture and decision-making planning. Tasks such as automatic picking and automatic placement of fruits and vegetables.
Parameters of crawler-type fruit and vegetable picking robot
—— -
Picking robot development platform TSCZ-5 | Structure type | Crawler |
Motor Power | 2*600W | |
Load | 200kg | |
Navigation accuracy | ±20 mm | |
Maximum travel speed | 1m/s | |
Minimum turning radius | 1m | |
Control method | Remote control/automatic | |
Remote control distance | 100m | |
Obstacle avoidance range | 0.1-1m | |
Working life | 3h | |
Charging time | 6h | |
Walking speed | 0-1m/s | |
Maximum climbing angle | 15° | |
Anti-collision function | Ultrasound | |
Protection level | IP67 | |
Operating temperature | -40℃~+85℃ |
Agricultural robot vision and execution system TSCZ-5-ZX | Robotic arm freedom | 6 freedom |
Positioning accuracy | When the measurement distance is less than 1m, the error of the X and Y axis ≤8mm, the error of the Z axis (vertical) ≤10mm | |
Scope | Within 1M working distance, not less than 700 × 500mm | |
Load capacity | 3kg | |
Navigation camera resolution | 320*240, 30 frames/second | |
Light range | 4300lux - 8400lux | |
Colorful space | RGB, HIS, YCBCR visual navigation software based on the Windows platform | |
Deep camera viewing angle | 87° × 58° | |
Color camera resolution | 1920 × 1080 | |
Color camera viewing angle | 69°× 42° |
Picking robot software (tomato) TSCZ-5-ZX-RJ | Identification method | Deep learning |
Navigation System | Relying on multi-sensor fusion algorithm to build navigation map | |
Fruit and vegetable positioning methods | 3D vision positioning algorithm |
Product Features
—— -
Precise fruit harvesting
· Accurately determine the size, color, shape, maturity and picking location of pickable fruits and vegetables through intelligent deep learning algorithms, 2D and 3D vision algorithms.
Flexible grabbing control
· The flexible picking hand uses adaptive control to capture the fruit and vegetable picking positions without damaging the fruit.
Multi-terrain operations and navigation
· In view of the diversity of agricultural terrain and materials, a variety of crawler, wheeled or track walking systems and driving methods are provided to meet the requirements of different scenarios.
Application scenarios
—— -
Venue type Facility agriculture (suitable for track wheel type), non-facility agriculture scenarios (suitable for crawler type) | ![]() |
Types of fruits and vegetables Single-fruit tomatoes, bunch tomatoes, grapes, cucumbers, strawberries, oranges, kiwis, etc. | ![]() |
*This model is customized, the parameters are for reference only, please contact the merchant for details.
Recommended products
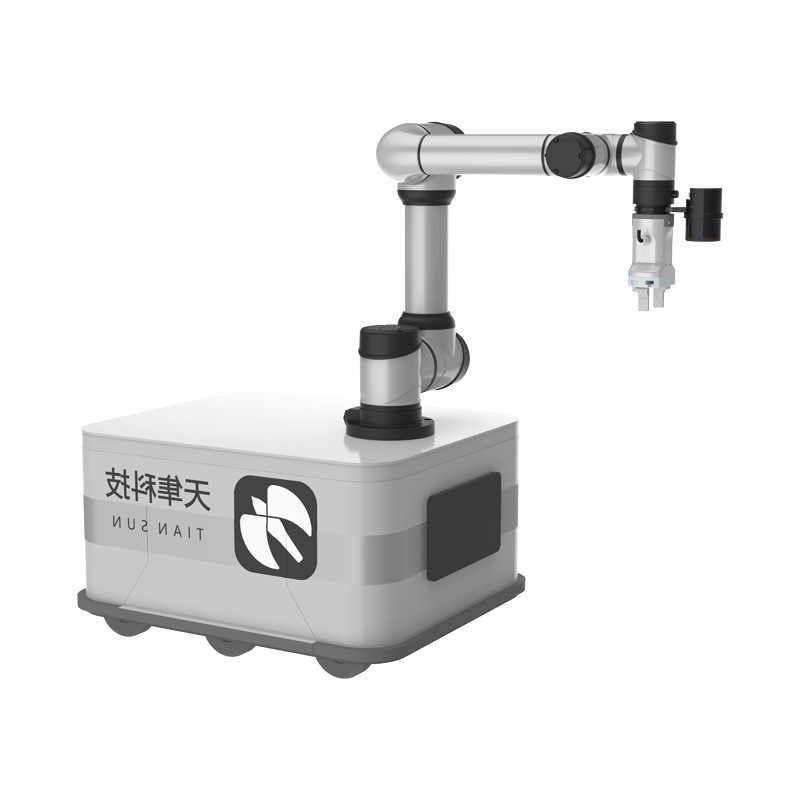
Mobile Grasping Composite Robot
The integrated design of collaborative robot and camera light source + mobile chassis constitutes a composite robot
collect:0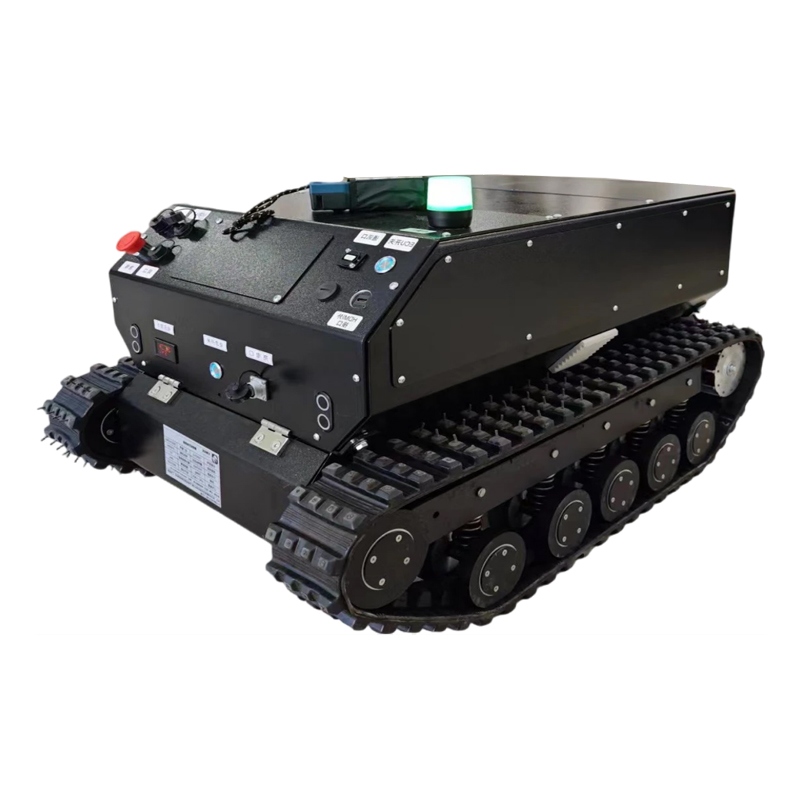
Crawler traveling chassis TSRDP-5
Crawler chassis modular design crawler chassis robot platform
collect:0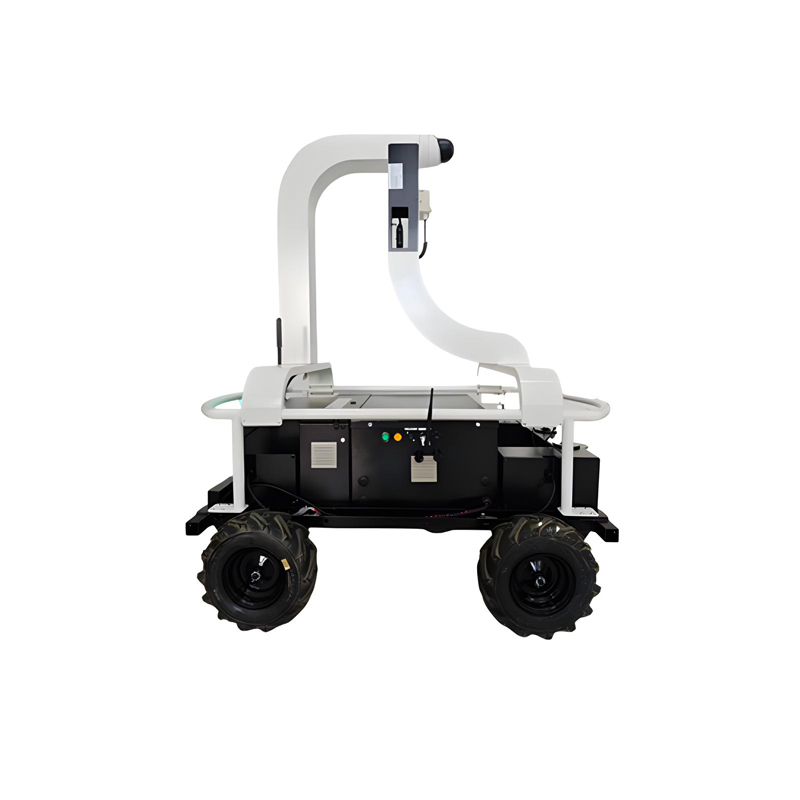
Inspection robot
Agricultural inspection robot autonomous navigation satellite positioning intelligent agricultural robot
collect:0