Product Description
Laser cutting and welding components are ideal for precise cutting and joining, offering high precision, heat resistance, moisture resistance, and durability against harsh conditions. Unlike traditional methods, they provide better resistance to material deformation and high mechanical stress. These systems also handle thermal expansion effectively, ensuring part accuracy and integrity. This improves performance and extends the lifespan of finished components, making them perfect for complex industrial applications.
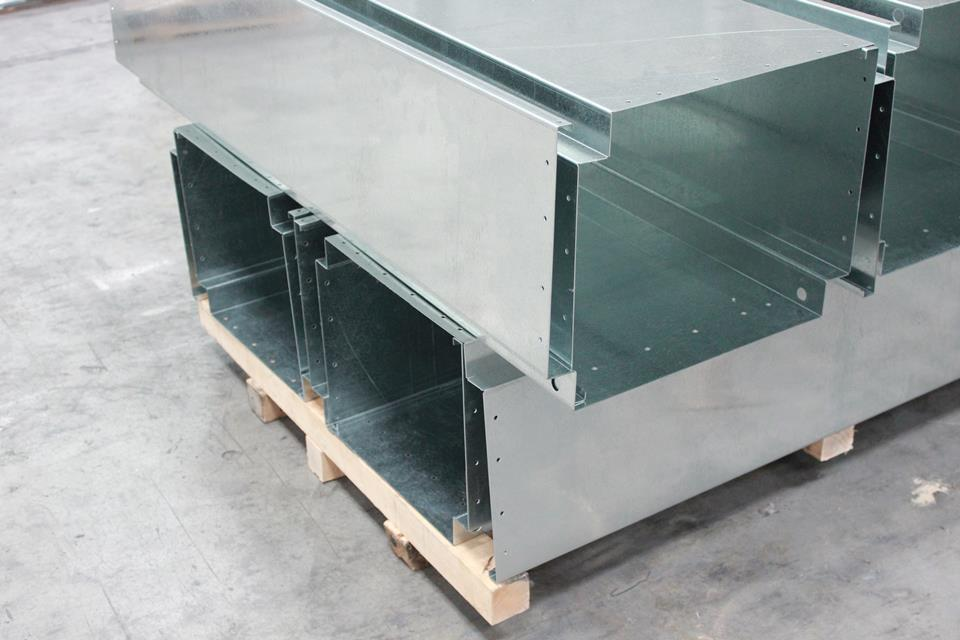
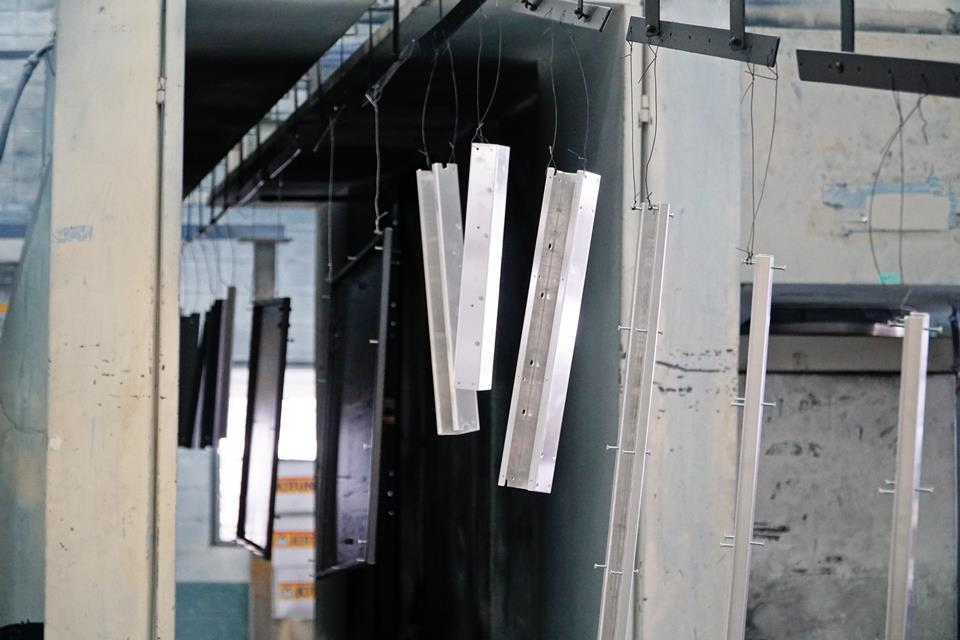
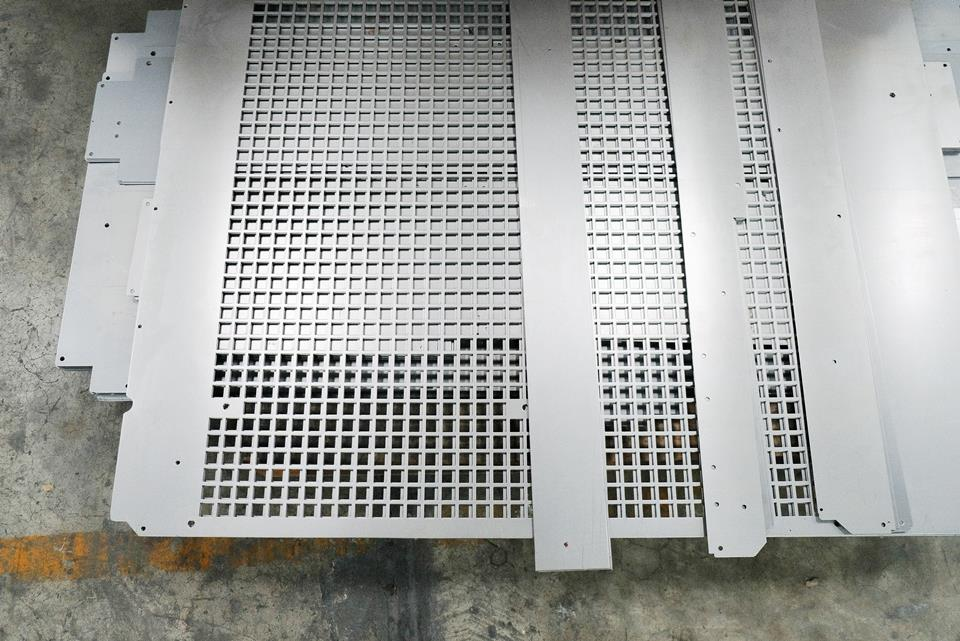
Product parameters
List | Details |
---|---|
Product name | Custom sheet metal fabrication Parts |
Thickness | 0.1mm-12mm |
Materials | Zinc, alunimum, copper, steel, powder coating, etc |
Surface treatment | Electric plating,powder coated,sand blasting,lacquer |
Process | Punching, stamping, bending, riveting, etc. |
Technology | Stamping , Laser cutting , Welding |
Service | Stainless steel part sheet metal stamping parts air conditioning parts |
Testing | Salt spray |
Certification | ISO 9001:2008, RoHS |
Custom Process
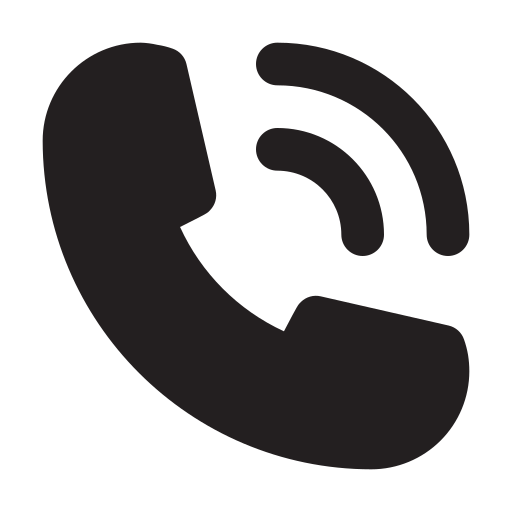
1. Send inquiries
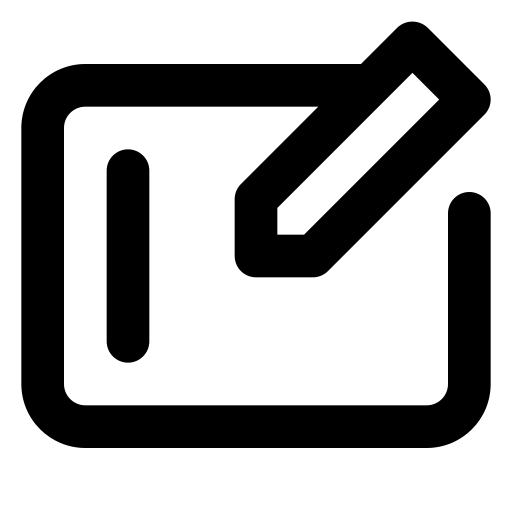
2.Drawings or samples
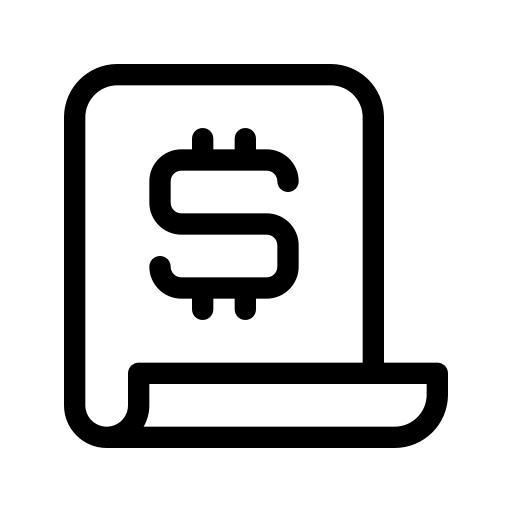
3. Quotation
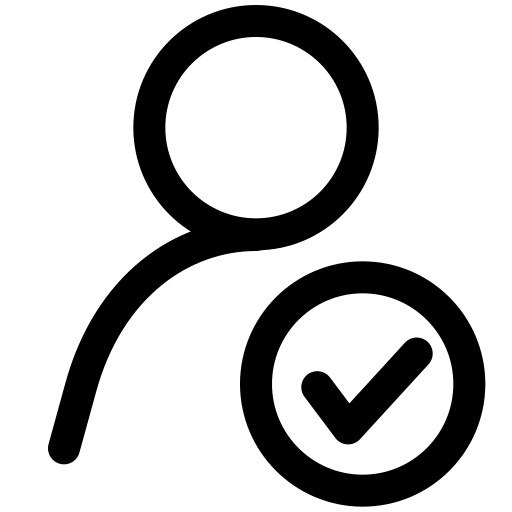
4.customer confirmation
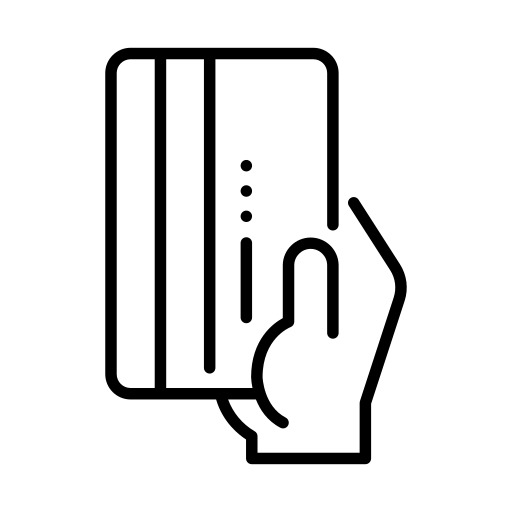
5. Places order and pays
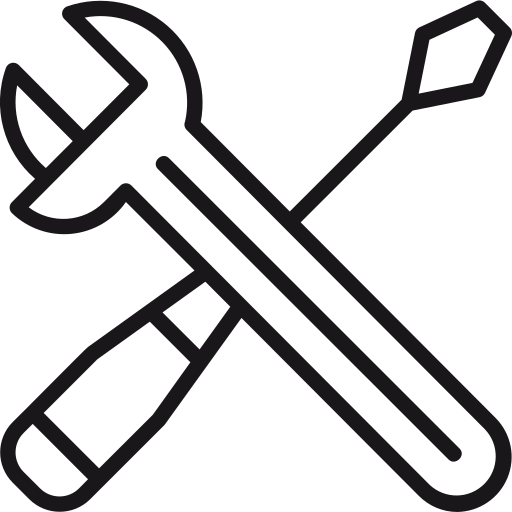
6.Mass production
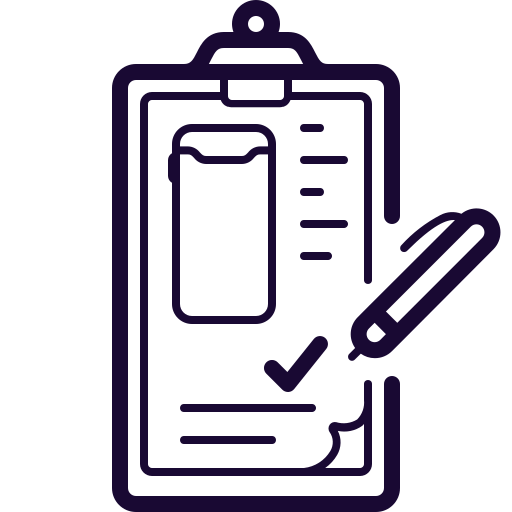
7.Test before packaging
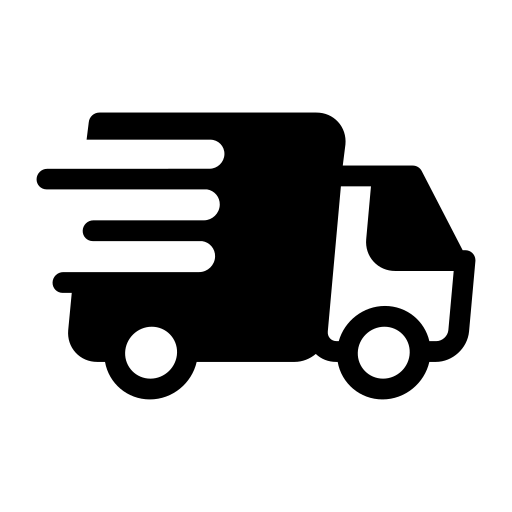
8.Shipping & confirmation
Process Type
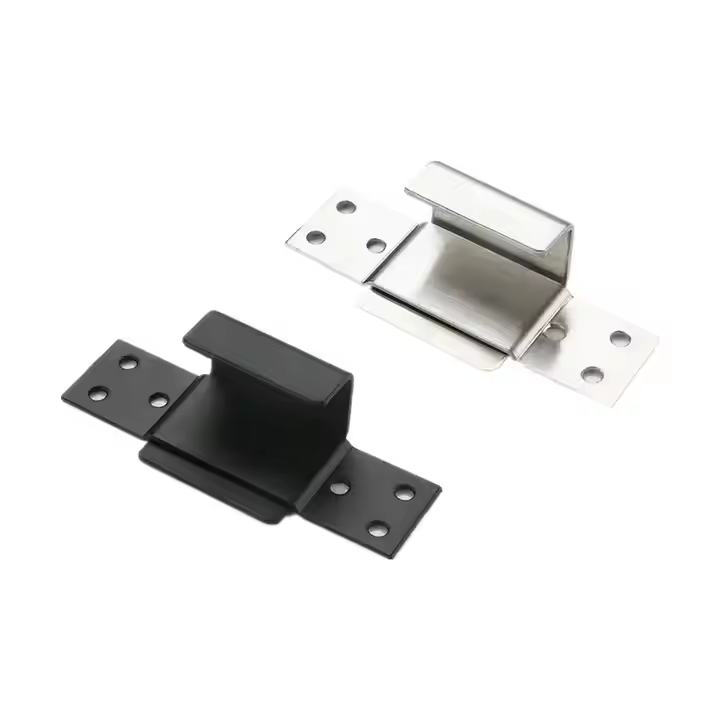
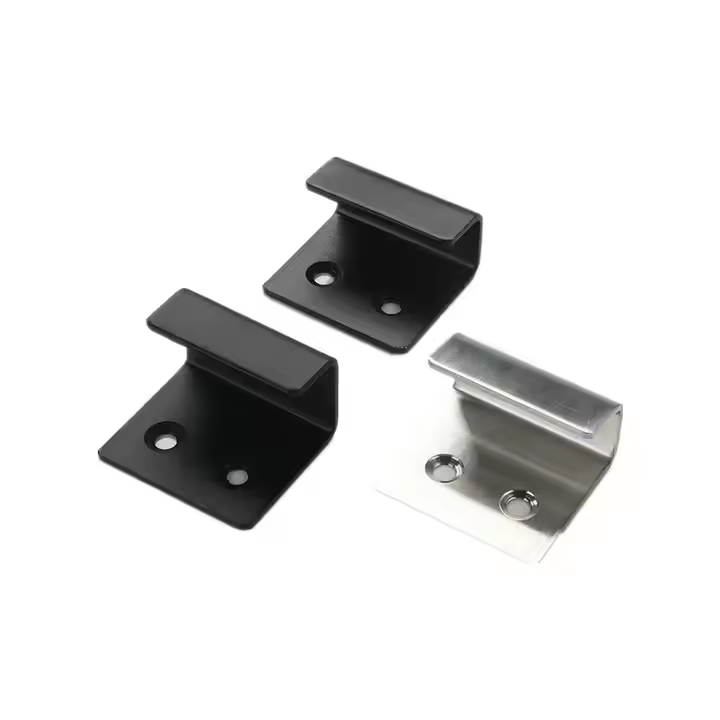
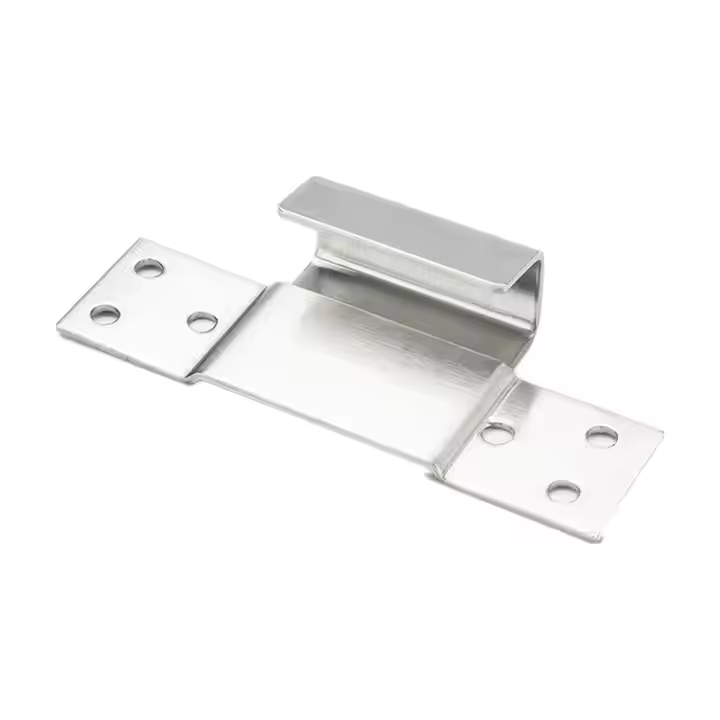
Material

Aluminum alloy
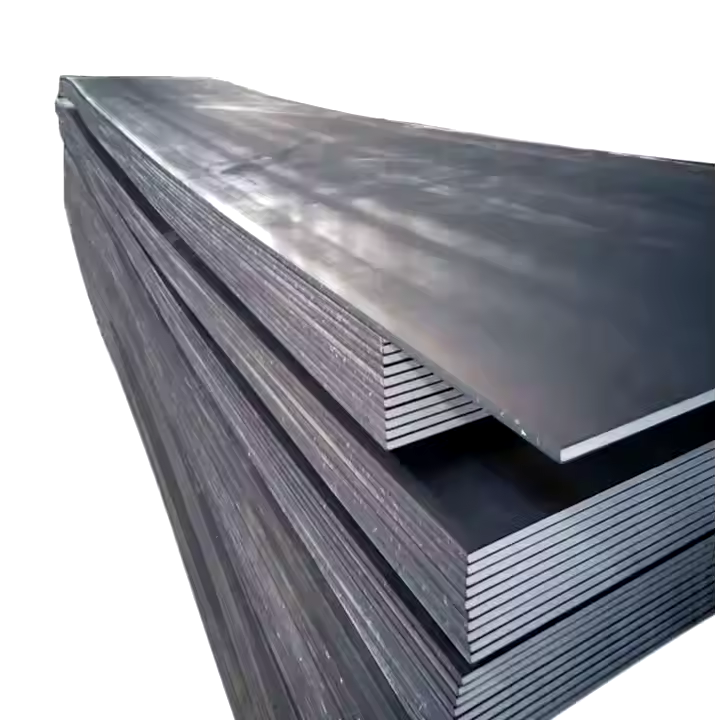
Metal Sheet
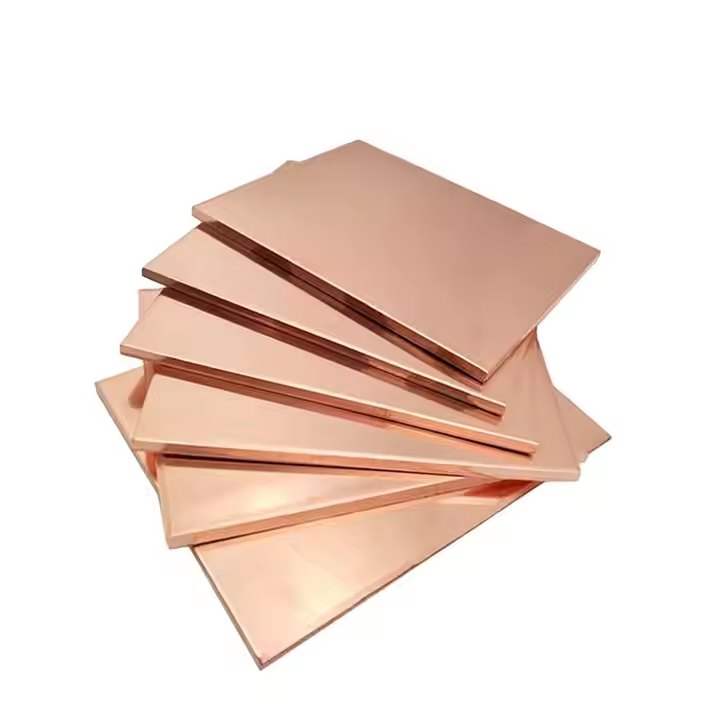
Copper Sheet

Brass Sheet
Quality Control
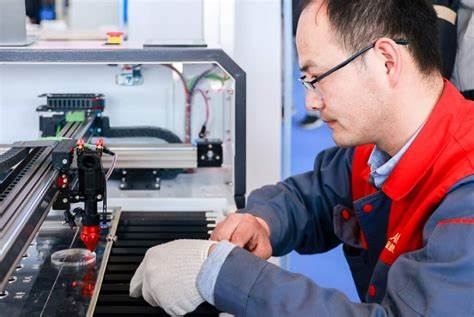
Quality Control (QC) for a laser cutting company specializing in robotic parts focuses on ensuring the highest precision, durability, and functionality of the components. Key QC processes include:
1. Material Inspection: Verifying that materials like metals or alloys meet the required specifications for strength, thickness, and quality before cutting.
2. Laser Calibration and Settings: Regular calibration of the laser cutting machine to ensure accurate cuts, with adjustments to laser power, speed, and focus based on the material and part complexity.
3. Dimensional Accuracy: Measuring and verifying the dimensions of each cut part against the design to ensure tight tolerances, especially for robotic components that must fit and function precisely within a robotic system.
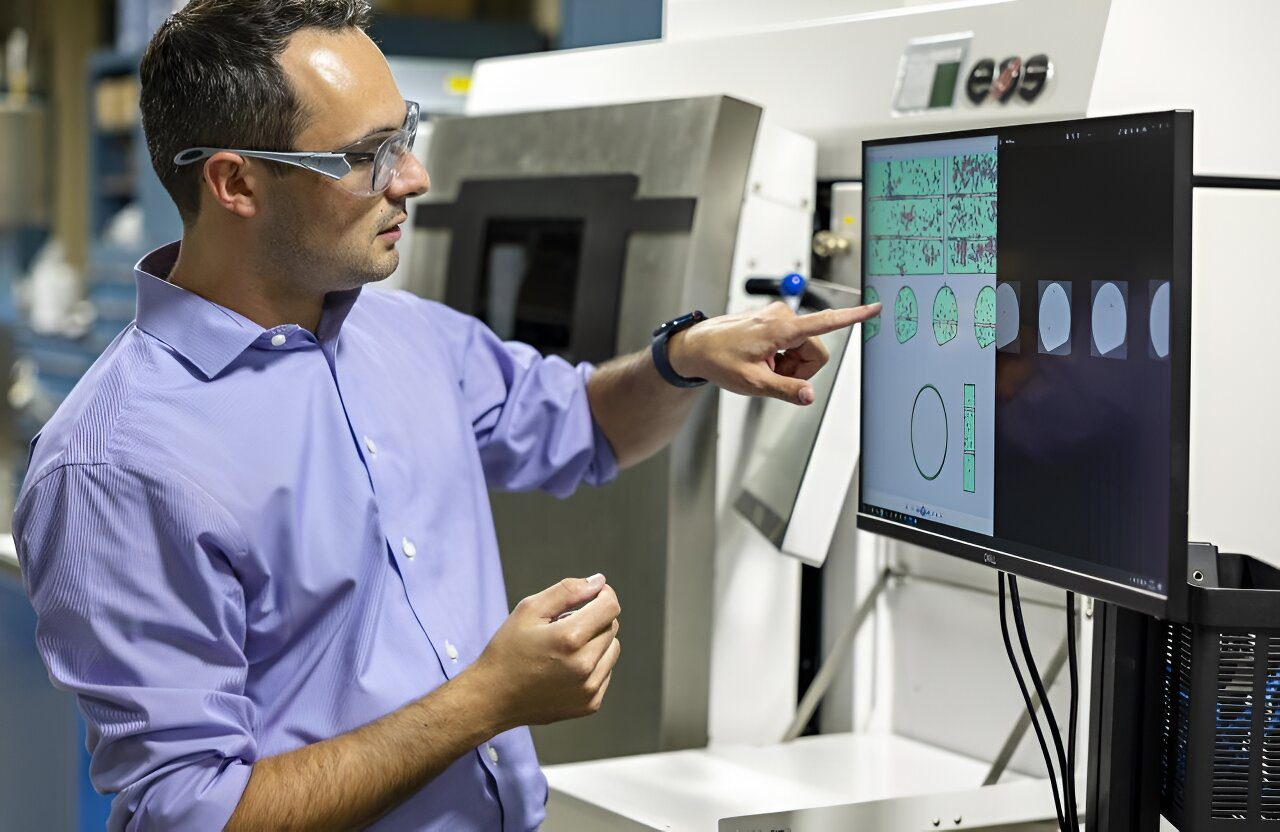
4. Surface Quality Check: Inspecting the cut edges for smoothness, minimal heat-affected zones, and no deformation, as imperfections can impact assembly or performance.
5. Functional Testing: Performing functional checks on parts (e.g., fitment, movement, or integration tests) to ensure they will perform as required within the robotic system.
6. Final Inspection and Documentation: A thorough final inspection of all parts, including visual checks and automated measurement systems, to ensure conformity to the design. Detailed reports are kept for traceability.
In conclusion, QC in laser cutting for robotic parts ensures precision, durability, and performance, reducing errors and improving the quality and reliability of the robotic systems.
Processing capability
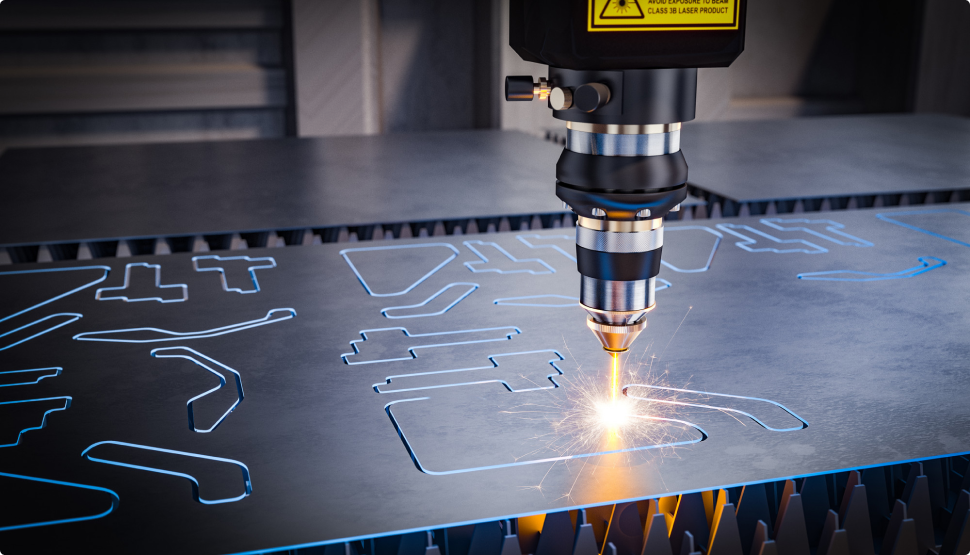
A laser cutting company specializing in robotic parts offers high precision (±0.1 mm tolerance), the ability to process various materials (metals, plastics, composites), and can handle complex, intricate designs. The technology ensures fast, efficient cutting with clean edges, minimal heat-affected zones, and minimal material waste. It also supports rapid prototyping, custom designs, and integration into automated production lines for large-scale manufacturing. This makes laser cutting ideal for producing high-quality, precise robotic components.
Additional processes
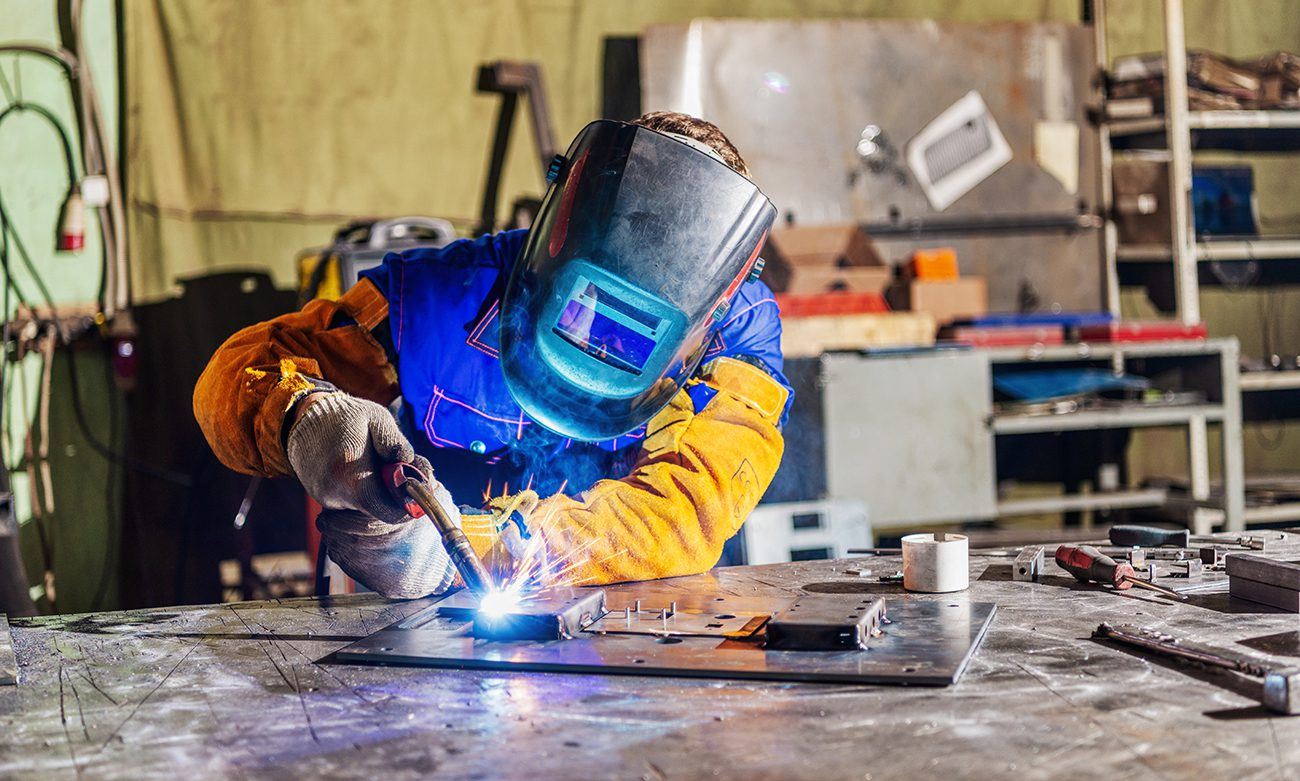
The processing capability of a laser cutting company that specializes in robotic parts revolves around the precision, speed, and flexibility of the laser cutting technology, combined with the ability to handle complex designs and various materials. Key capabilities include:
- Precision Cutting
- Material Versatility
- Complex Shapes and Intricate Designs
- Speed and Efficiency
- Edge Quality
- Automation Integration
- Customization and Prototyping