Product Description
We are fully aware of the high requirements of robot technology for precision and reliability, so we pursue perfection in every processing link, strive to provide high-quality components that exceed industry standards, and help customers achieve more efficient production and more precise operations. With an innovative, professional and rigorous attitude, we continue to promote the development of the robot industry and have won wide industry recognition and customer trust.
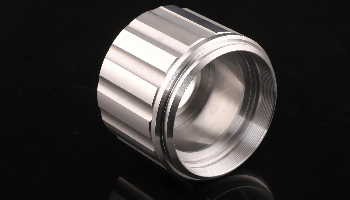
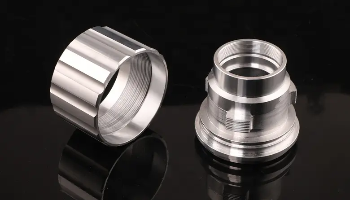
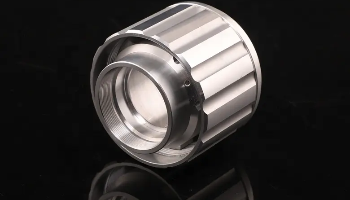
Product parameters
Product Name | Custom precision aluminum/metal/zinc alloy cnc machining service |
Material | Aluminum,Hardened Metals, Precious Metals, Zinc alloy |
Weight | / |
Tolerance | 0.005mm~0.1mm |
Equipment | CNC Machining center, CNC Lathe, Turning machine, Milling machine, Drilling machine, Internal and external grinding machine, Cylindrical grinding machine, Tapping drilling machine, Wire cutting machine, polishing machine etc. |
Surface treatment | Anodizing, sandblasting,Powder Coating, zinc/chrome/nickel/silver/gold Plating, Polish, Nitriding, Blacking, Painting, Heat treatment etc |
MOQ | 100pcs, according to your drawings |
QC System | 100% inspection before shipment, product OK rate 99.8% |
Drawing | Provide by customer, or design according as the sample |
Drawing format | Pro/E, AutoCAD, Solidworks, CAXA, UG, CAD, CAM, CAE, STP, IGES, etc. |
Payment term | T/T, Erik pay, West Union,etc |
Custom Process
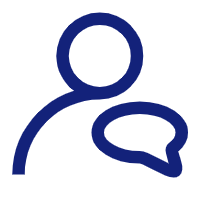
1. Customer inquiry
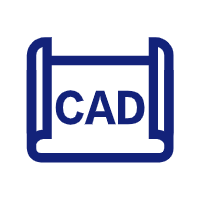
2.Send drawing/sample
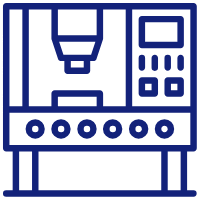
3. Mold making
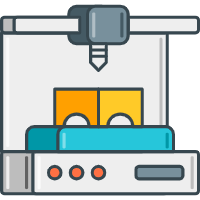
4. Machine processing
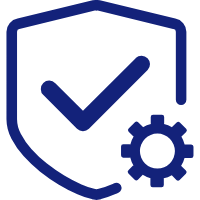
5. Quality Control
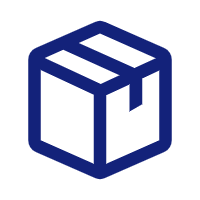
6. Packing
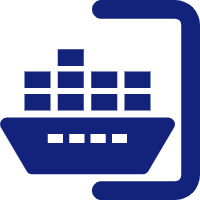
7. Transportation
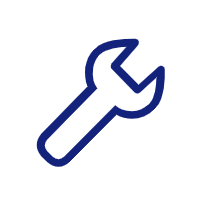
8. After-sale support
Process Type
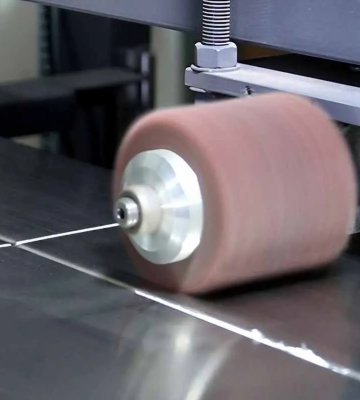
Polishing
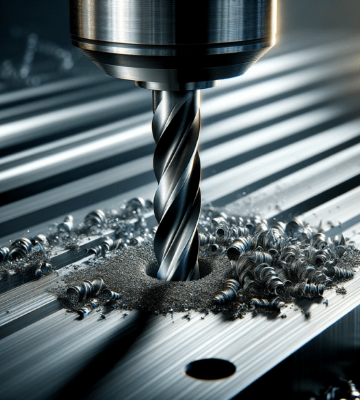
Drilling
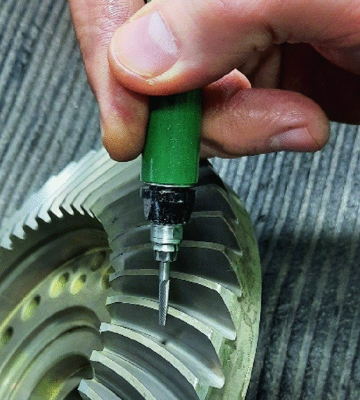
Deburring
Material
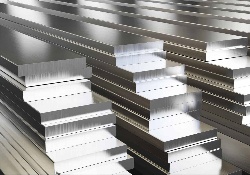
Aluminum Alloy
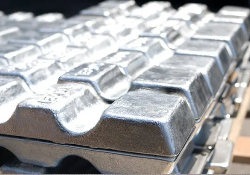
Zinc Alloy
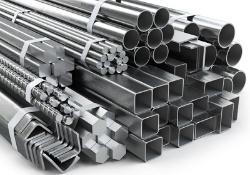
Alloy Steel
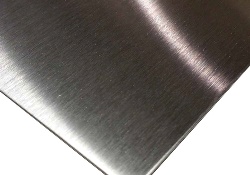
Stainless Steel
Quality Control
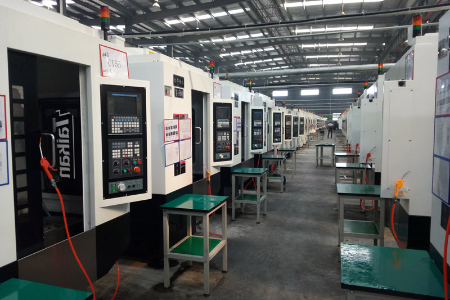
The advantages of CNC tapping machines make them an essential tool in modern manufacturing environments, especially for industries that require high-precision, high-volume production. The machine's ability to automate complex operations ensures high consistency, increases productivity and reduces costs, making it a valuable investment in any production line.
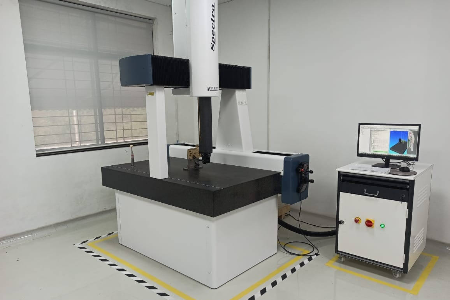
The Coordinate Measuring Machine (CMM) is an invaluable tool in manufacturing and quality control due to its high precision, repeatability, efficiency, and versatility. It significantly enhances the quality control process by providing fast, accurate, and automated measurements across a wide range of part sizes and geometries. CMMs reduce human error, scrap, and rework, while improving productivity and providing traceability for compliance with industry standards. This makes them an essential tool in industries that demand the highest levels of part accuracy and quality, from aerospace and automotive to electronics and medical devices.
Additional processes
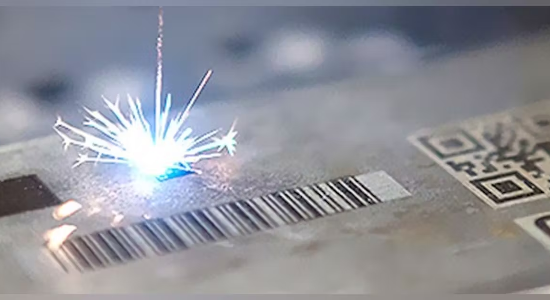
Laser Marking and Engraving
· Laser Marking: A high-precision process used to add identification marks, barcodes, serial numbers, or logos to parts. It uses a laser beam to alter the surface of the material without causing deformation.
· Laser Engraving: A more intense process where the laser is used to engrave designs or text on a part, commonly used in industries like aerospace or medical devices for permanent identification.
Advantage: High-precision engraving and marking without affecting the part’s integrity, ideal for traceability and aesthetic purposes.
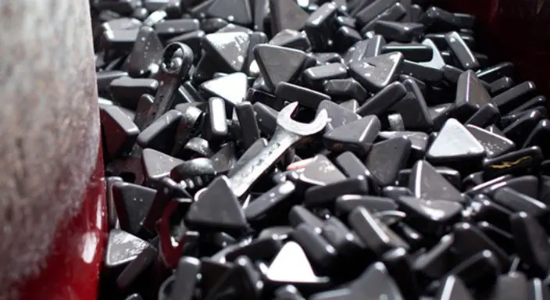
Tumbling and Vibratory Finishing
· Tumbling: A process where parts are placed in a rotating drum with abrasives or polishing media. This process is ideal for deburring, polishing, and rounding edges of small parts.
· Vibratory Finishing: Similar to tumbling, but instead of rotation, parts are vibrated with media in a bowl or trough. This is used for deburring and polishing parts in bulk, especially small and delicate components.
Advantage: Ideal for deburring, polishing, and surface preparation for high-precision parts with intricate geometries or sharp edges.