Product Description
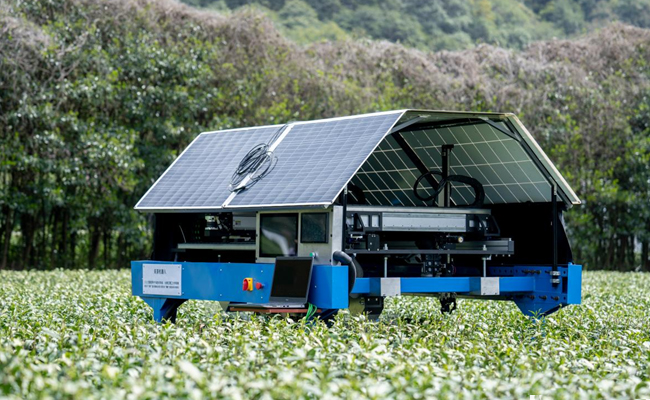
Youcha Intelligent Picking Robot
Youcha Intelligent Picking Robot can accurately identify tea buds through AI image recognition and artificial intelligence algorithms, thus ensuring that the tea buds can be picked correctly. At the same time, the tea picking robot also uses photovoltaic power generation technology to achieve 24-hour uninterrupted green and environmentally friendly continuous tea picking.It is estimated that one machine can replace 1.5 workers and can pick 1.5 kilograms of dry tea per day.
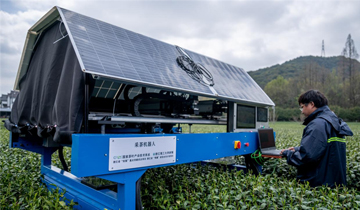
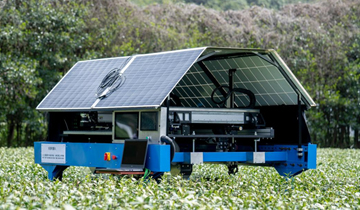
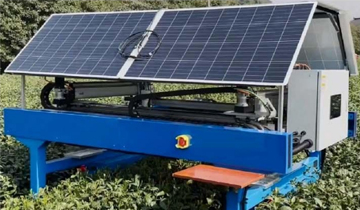
Product Features
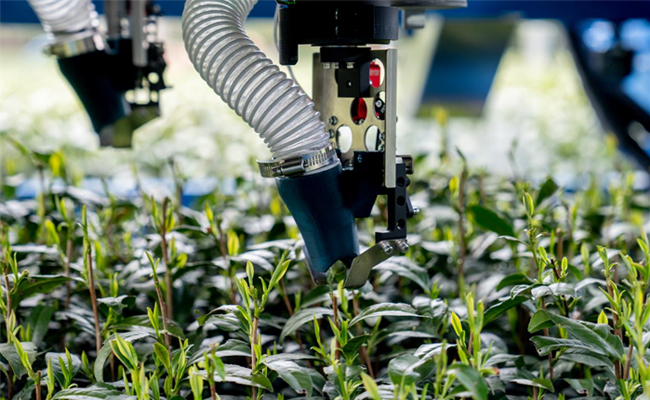
- Efficient picking of young tea leaves
The lightweight rectangular coordinate robot arm (double arms) can easily complete multiple tasks including path planning, picking and negative pressure guided collection; the shearing picking arm enters the picking arm and shears the young tea leaves through negative pressure guidance, and the young tea leaves are transported to the collection frame through the pipeline negative pressure.
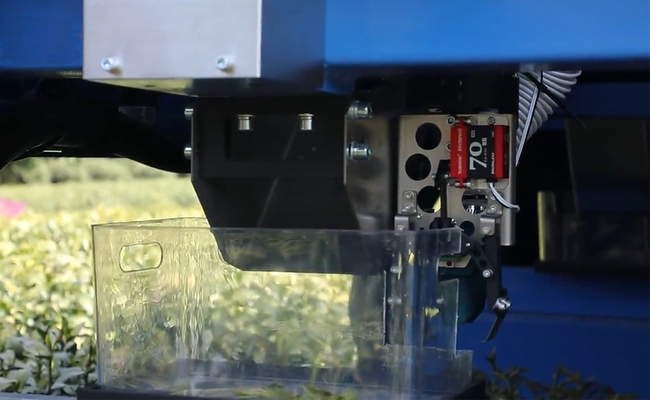
- Green energy system
10kwh large capacity battery, continuous operation time exceeds 8h; the battery has enhanced self-balancing, stable and consistent output voltage, and long life; with solar charging panel roof, the battery life is longer.
- Visual interactive interface
Visual display of tea images, tea leaf identification and location information; real-time display of system working status information; visual parameter adjustment interactive window.
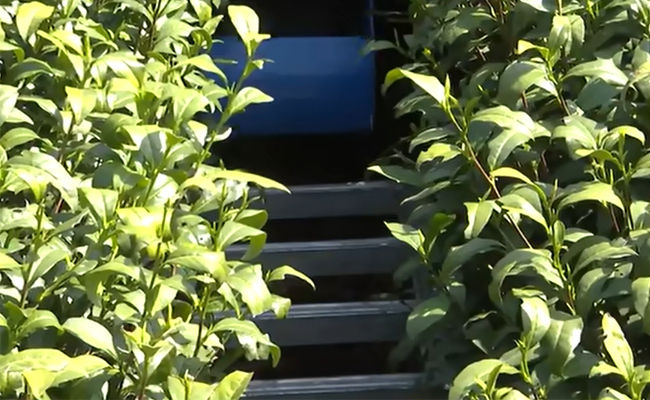
- Tracked autonomous navigation walking
The differential satellite positioning system detects the robot's current position in real time and controls the robot to walk along the tea ridges. It is equipped with visual, laser or magnetic induction sensors to complete accurate navigation walking along the center line of the tea ridges;
The 360° radar can detect the working environment and obstacle information in advance through uninterrupted scanning, and adjust the walking strategy in time according to the environment to achieve autonomous obstacle avoidance;
Application Cases
Youcha intelligent picking robots can be used in tea gardens in various places, greatly improving picking efficiency, ensuring tea quality, adapting to complex terrains and reducing costs, thus promoting the intelligent development of the tea industry.
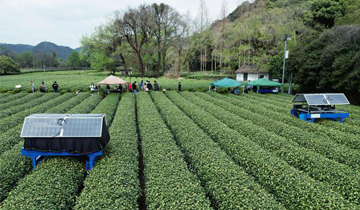
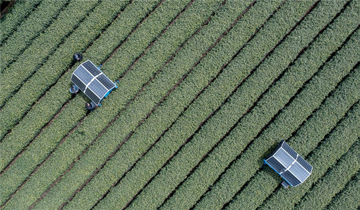
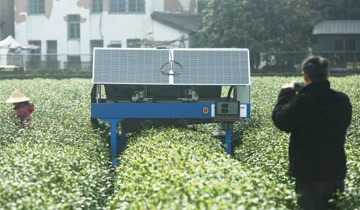
Technical Parameter
Parameters | Unit | Numerical value |
---|---|---|
Overall dimensions (length × width × height) | mm | 2280×2100×2150 |
Satellite navigation accuracy | mm | ±50 |
Vision/laser alignment accuracy | mm | ±25 |
Recognition success rate | % | 88 |
Picking success rate | % | 60 |
Single manipulator picking speed | s/piece | 1.8 |
Maximum driving speed | m/s | 0.6 |
Minimum turning radius | m | 2.5 |
Control method | / | Remote control/automatic |
Obstacle avoidance range | m | 0.1~1 |
Anti-collision function | / | Ultrasound |
Working endurance time | h | ≥8 |
Battery capacity | kwh | 10 |
Product protection
- Professional after-sales service team: Equipped with a professional after-sales service team, the team members have rich robot technology knowledge and maintenance experience, and can respond to customers' after-sales needs in a timely manner. Whether it is during the installation and commissioning stage of the robot or when problems occur during daily use, technical support and solutions can be quickly provided to customers to ensure the normal operation of the robot.
- Timely spare parts supply: A complete spare parts supply system has been established to ensure that the required original spare parts can be provided in time when the robot fails. Adequate spare parts inventory and efficient logistics distribution network minimize the waiting time for maintenance and reduce the impact of equipment failure on tea picking work in the garden.
- Strict production process and quality inspection: Following strict production process and quality control standards, from the processing and manufacturing of parts to the assembly and commissioning of the whole machine, every link is carefully controlled and strictly inspected. On the production line, multiple quality inspection processes are set up to conduct comprehensive inspections on various performance indicators of the robot, such as the movement accuracy of the robot arm, the accuracy of the visual recognition system, the positioning accuracy of the navigation system, etc., to ensure that every robot shipped meets high quality requirements.