Product Description
M16 is a newly developed 16-line three-dimensional liDAR, which is mainly used for the measurement of fast moving objects in the middle and long distance and the measurement of the surrounding environment. With the characteristics of fast measurement speed, high spatial resolution, intensive point cloud data capture, and small size, it is a necessary core sensor for driverless cars and ADAS, and can also be applied to three-dimensional map measurement and other fields.
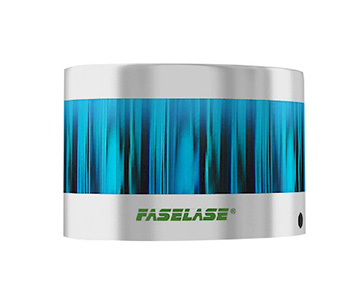
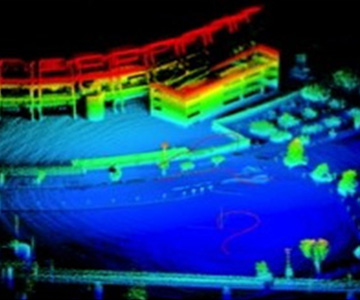
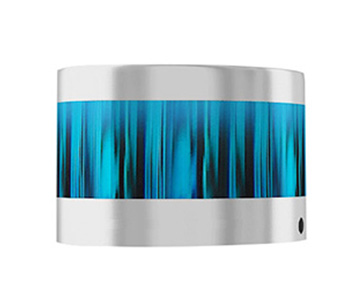
Product parameters
Project | Index |
---|---|
light source | 905nm |
Scanning speed | 20Hz |
Measuring field of view | 360°X30° |
Angular resolution | 0.24°X2° |
Number of scan lines | 16-wire |
Measuring distance | 0.1~200m |
Distance resolution | 1cm |
measurement accuracy | ±3cm |
Output Interface | Ethernet |
Power supply | DC9~32V |
Operating temperature | -20℃~+55℃ |
storage temperature | -40℃~+85℃ |
Protection level | IP67 |
Product Display
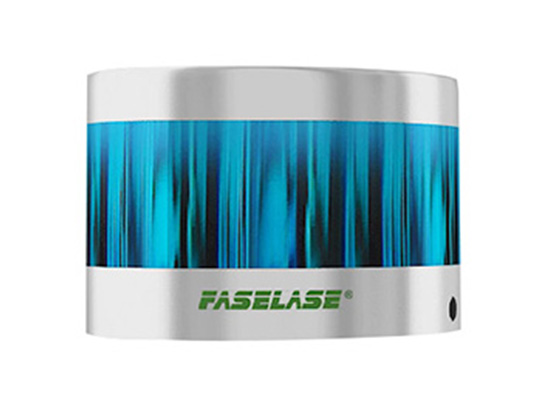
● Long detection distance: up to 200m
● Point cloud data intensive: 320,000 points per second, 360° scanning, 16-line measurement of the surrounding environment, to build accurate three-dimensional spatial maps
● Horizontal scanning Angle :360°, vertical Angle: 30°
● Protection grade: IP65 (dustproof and waterproof)
● Eye safety laser protection, in line with standards
● 3D laser point cloud data analysis system, convenient for users to secondary development
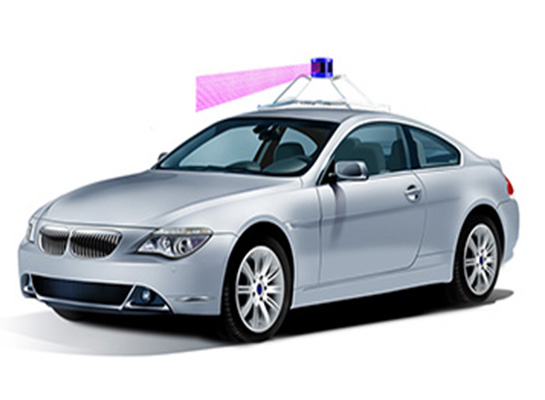
- Large-angle scanning: It usually has a large scanning Angle, and can realize 360° scanning in the horizontal direction and vertical scanning in a certain range, so as to cover a large spatial range and carry out a comprehensive detection of the surrounding environment.
- Long distance detection: can detect a long distance, the general three-dimensional lidar detection distance in tens of meters to hundreds of meters or even farther, can meet the needs of different application scenarios for remote target detection.
Quality Control
- Optical component
For the laser in the laser emission module, the parameters such as wavelength accuracy and output power stability need to be strictly tested. For example, the deviation of the wavelength may affect the accurate reception and resolution of the light reflected by the liDAR on the target object, and the wavelength deviation is generally required to be controlled within a very small range, such as ±5nm.
The quality of the optical lens is also crucial. The curvature accuracy of the lens, the surface flatness and the transmittance of different wavelengths of laser light are all carefully tested. Any small flaw, such as a scratch or uneven curvature on the lens surface, can cause the laser to scatter or focus inaccurately, thus affecting the detection accuracy of the liDAR. The transmittance is generally required to reach more than 90% in a specific band.
- Electronic component
The chip on the circuit board is the "brain" of the lidar, and when conducting quality control, it is necessary to ensure that the performance of the chip meets the design requirements. For example, to test whether its data processing speed can meet the needs of liDAR to acquire and process large amounts of point cloud data in real time. At the same time, it is also necessary to check the stability of the chip in different temperature environments, because the lidar may generate heat during the working process, and the chip performance must be stable within a certain temperature range (such as -40 ℃ -85 ℃).
The parameter accuracy of capacitors, resistors and other discrete components can not be ignored. The deviation range between the nominal value and the actual value of these components should be controlled within a certain limit, such as the resistance value deviation of the resistance does not exceed ±1%, to ensure the normal operation of the circuit and the accuracy of signal transmission.
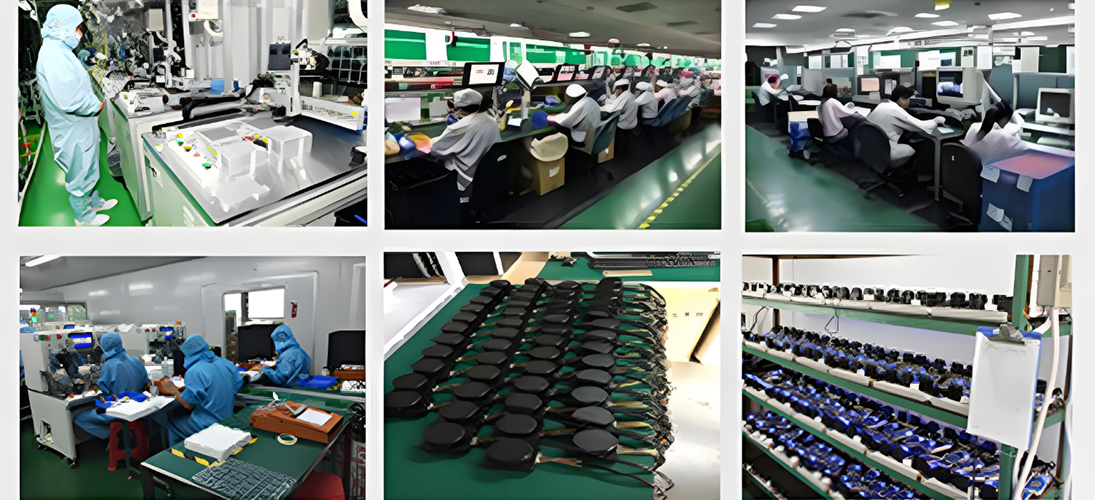
Application Cases
The driverless environment awareness core is designed for production vehicles; Multi-line LiDAR, accurate perception of the surrounding environment of the vehicle, even in bad weather conditions such as sand and haze and extreme light changes, can work normally; Solutions to accelerate the development of L4/L5 level autonomous driving.
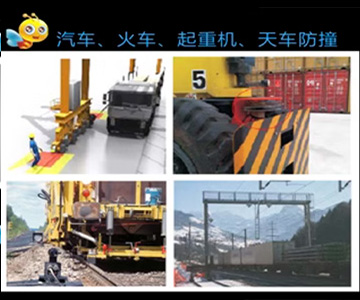
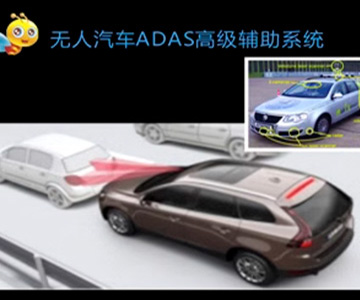
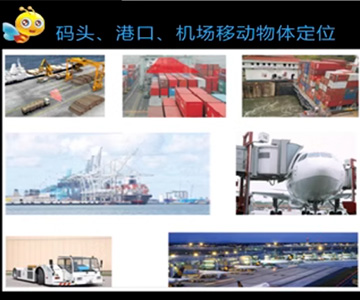
Service
Product training services: The company can provide customers with training on the use of Lidar products, operational processes, data interpretation and other aspects. This helps customers make better use of LiDAR equipment and reduce problems caused by improper operation. For example, engineers in automotive manufacturing companies are trained in the commissioning and data collection methods of in-vehicle lidar so that they can understand how radar works in autonomous driving scenarios.
Product customization services: According to the special needs of different customers, the performance parameters of Lidar (such as detection distance, angular resolution, scanning frequency, etc.), dimensions, installation methods, etc., are customized. For example, for space-constrained UAV application scenarios, customized miniaturized and lightweight liDAR.