Product Description
Machine tool sheet metal uses sheet metal technology to process metal sheets to make them into machine tool shells, protective devices, operating tables and other parts. It involves cutting, bending, stamping, welding and other operations on metal sheets (usually with a thickness of 0.5-6mm).
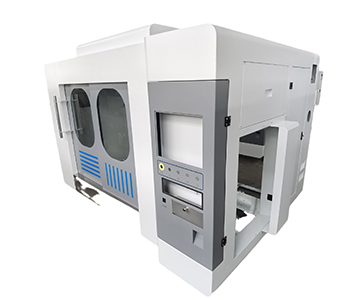
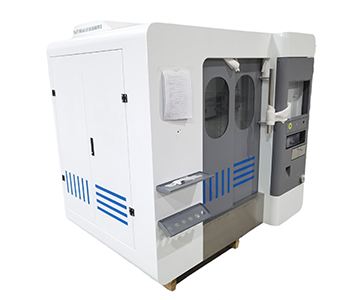
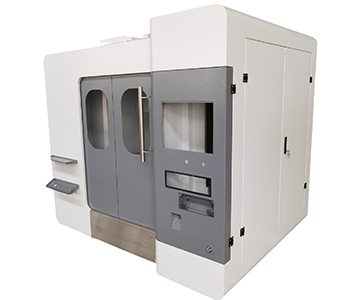
Product parameters
Name | Parameters | Name | Parameters | Name | Parameters |
---|---|---|---|---|---|
Name | Cabinet sheet metal | Material | Cold rolled plate | Surface treatment process | Sandblasting, polishing, other |
Sheet thickness | Customized (mm) | Processing size/length*width*height | Customized (mm) | Dimensional accuracy | ±1mm |
Molding parts | Machine shell | Cutting method | Punching, cutting, stamping, forming, bending, notching | Processable thickness | 0.1-15.0mm |
Surface treatment | Baking paint | Surface roughness | Customized | Sheet metal process | Laser cutting, punching, welding |
Proofing cycle | 1-3 days | Processing cycle | 8-15 days | Assembly service available | Assembly service available |
Application areas | Electricity, industrial equipment, public facilities | Specifications | Machine tool sheet metal consultation customer service | Maximum/minimum processing size | Customized |
Technological Innovation
Machine tool sheet metal can provide physical protection for the precision parts inside the machine tool. For example, it prevents foreign matter such as dust, chips, coolant, etc. from entering the moving parts and electrical systems of the machine tool, and avoids faults such as component wear and short circuit caused by foreign matter intrusion. In CNC machine tools, sheet metal shells can effectively prevent metal debris generated during processing from damaging key components such as screws and guide rails.
It can prevent operators from accidentally contacting dangerous areas of the machine tool, such as high-speed rotating spindles and moving workbenches. For example, sheet metal guardrails installed around lathes can, to a certain extent, prevent operators from being hit by workpieces or tools during operation.
Product Display
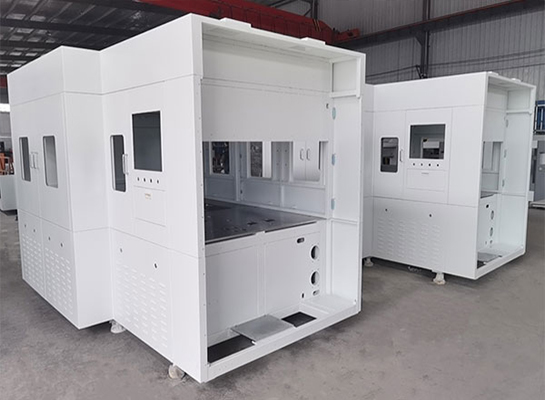
Laser cutting: high cutting accuracy, up to ±0.1mm; narrow cutting seam, small heat-affected zone, capable of cutting sheet metal parts with complex shapes. For example, when processing machine tool operating panels with complex patterns, laser cutting can well meet the design requirements.
Bending process: complex shapes can be processed, such as punching out various button holes, indicator light holes, etc. on the control panel of the machine tool. Stamping production efficiency is high, but the mold design and manufacturing are complex and the cost is high, which is suitable for mass production.
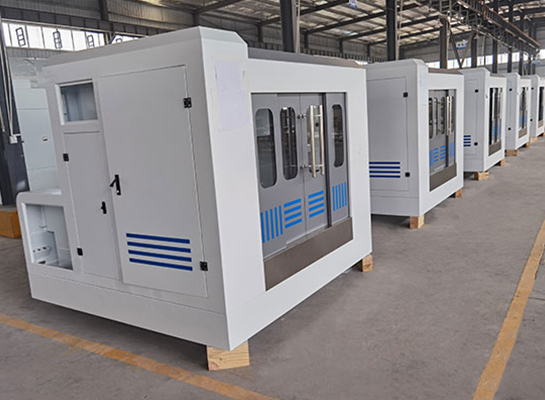
Stamping process: can realize the processing of complex shapes, such as punching out various button holes, indicator light holes, etc. on the control panel of the machine tool. Stamping has high production efficiency, but the mold design and manufacturing are complex and the cost is high, which is suitable for mass production.
Welding process: low cost, high production efficiency, suitable for medium and thick plate welding. In the welding of sheet metal structures of large machine tools, such as the welding of machine tool bases, carbon dioxide gas shielded welding is widely used.
Quality Control
Our products are all customized products. Before shipment, we will pass a special QC quality inspection to ensure product quality.
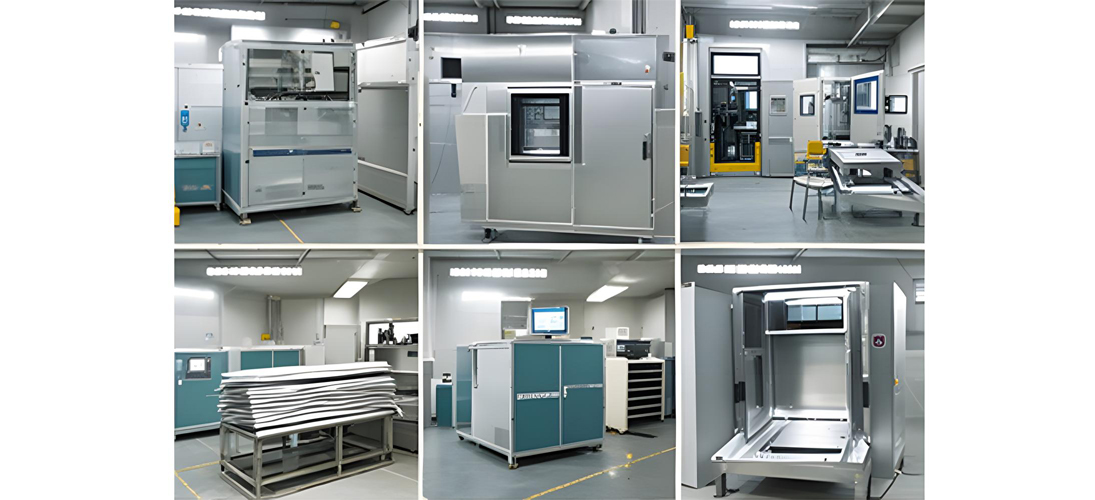
Application Cases
Large-scale sheet metal processing and customization have fully demonstrated its advantages in protection, performance assurance, aesthetics and lightweight in different industry applications. With the continuous development of processing and manufacturing technology, the design and processing technology of shell machine tool sheet metal will also continue to innovate and improve, providing stronger support for the development of the shell machine tool industry.
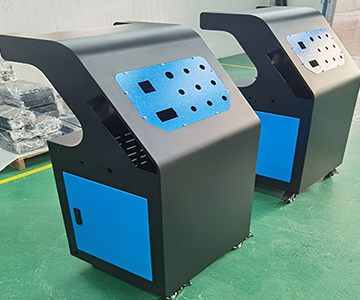
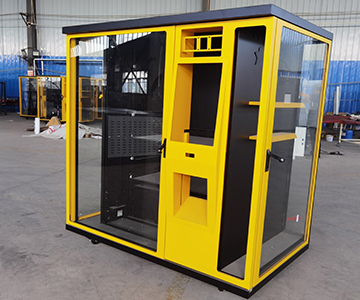
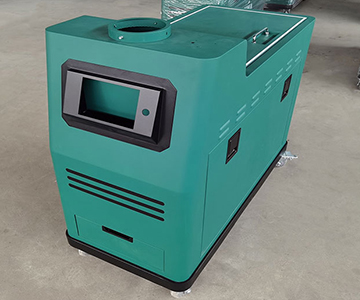