Product Description
Automatic Copper Knurling for precision parts ensures highly accurate and consistent texture patterns, improving both grip and surface quality. This process is ideal for enhancing the performance, durability, and functionality of mechanical components used in various high-precision applications, delivering optimal results in industries that require reliable and finely crafted parts.
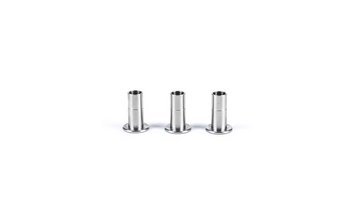

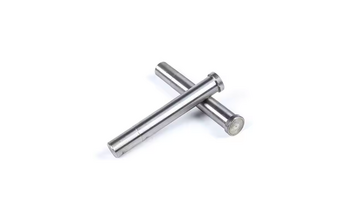
Product parameters
Service | CNC Machining Turning and Milling CNC Turning OEM Parts |
Material | 1). Aluminum: AL 6061-T6, 6063, 7075-T etc 2). Stainless steel: 303,304,316L, 17-4(SUS630) etc 3). Steel: 4140, Q235, Q345B,20#,45# etc. 4). Titanium: TA1,TA2/GR2, TA4/GR5, TC4, TC18 etc 5). Brass: C36000 (HPb62), C37700 (HPb59), C26800 (H68), C22000(H90) etc 6). Copper, bronze, Magnesium alloy, Delrin, POM,Acrylic, PC, etc. |
Finish | Sandblasting, Anodize color, Blackenning, Zinc/Nickl Plating, Polish, Power coating, Passivation PVD, Titanium Plating, Electrogalvanizing, electroplating chromium, electrophoresis, QPQ(Quench-Polish-Quench), Electro Polishing,Chrome Plating, Knurl, Laser etch Logo, etc. |
Drawing format | STEP,STP,GIS,CAD,PDF,DWG,DXF etc or samples. |
Tolerance | +/-0.01mm ~ +/-0.05mm |
Surface roughness | Ra 0.1~3.2 |
Inspection | Complete inspection lab with Micrometer, Optical Comparator, Caliper Vernier,CMM Depth Caliper Vernier, Universal Protractor, Clock Gauge, Internal Centigrade Gauge |
Capacity | CNC turning work range: φ0.5mm-φ150mm*300mm CNC milling work range: 510mm*1020mm*500mm |
Custom Process
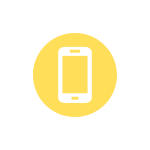
1.send inquiries
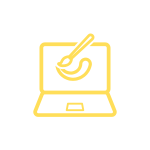
2.drawings or samples
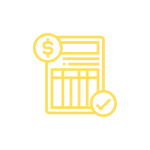
3. Quotation
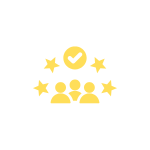
4.customer confirmation
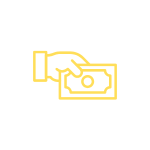
5. places order and pays
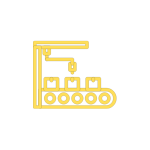
6.Mass production
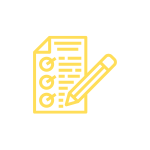
7.Test before packaging
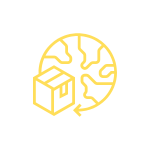
8.Shipping & confirmation
Process Type
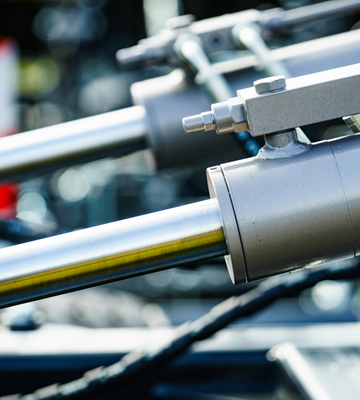
Hydraulic System Components
- Corrosion Resistance: Pins used in hydraulic systems often undergo treatment to resist corrosion, which is crucial in environments with exposure to fluids.
- Impact Resistance: Hydraulic systems face sudden pressure surges. The pin's material is designed to handle dynamic loads without deforming.
- Smooth Operation: The pin's polished surface reduces friction, improving the efficiency of hydraulic cylinders and extending their lifespan.
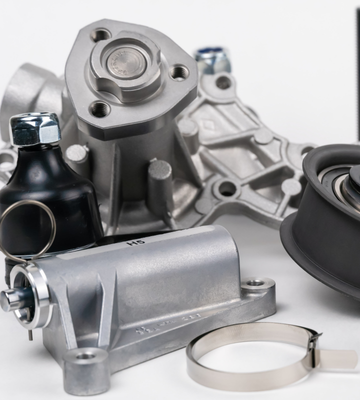
Automotive Suspension System
- Load Distribution: Helps evenly distribute forces from the suspension arm to the wheel assembly, reducing wear on other components.
- Durability in Harsh Conditions: Resistant to road debris, heat, and moisture, ensuring reliable performance in diverse driving environments.
- Safety Enhancement: The pin's precise fit prevents wobbling or misalignment, maintaining the vehicle's stability and safety
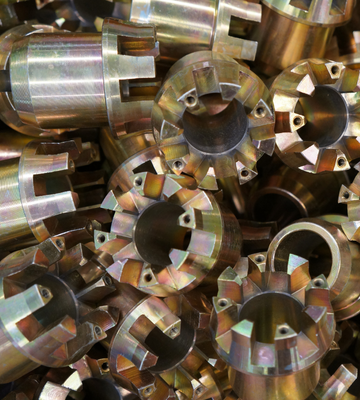
CNC Machine Components
- Repeatability: Guide pins ensure workpieces are consistently positioned, enabling mass production with minimal errors.
- Minimized Vibration: By securely holding the part, the pin reduces vibrations during machining, improving surface finishes.
- High-Temperature Tolerance: Pins used in CNC machines are often exposed to heat generated by cutting. Their material resists deformation under high temperatures
Material
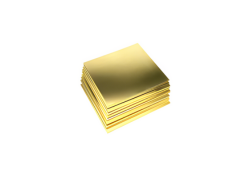
Brass
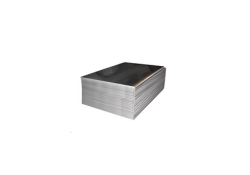
Aluminum Alloy
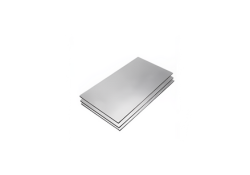
Stainless Steel
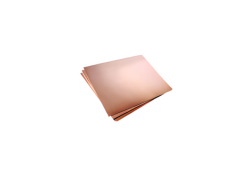
Copper
Quality Control
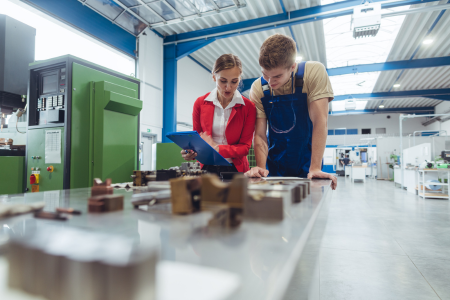
Quality control for Automatic Copper Knurling for precision parts involves a comprehensive inspection process to ensure the accuracy of knurling patterns, consistency in texture, and proper dimensional tolerance. Each part is carefully checked for uniformity and precision, with emphasis on surface quality to ensure no defects such as distortion or uneven knurling. Advanced measurement tools and techniques are used to verify that the parts meet stringent performance and durability standards. The process also includes testing for grip effectiveness and functionality in real-world applications, ensuring high-quality, reliable results for every component.
Processing capability
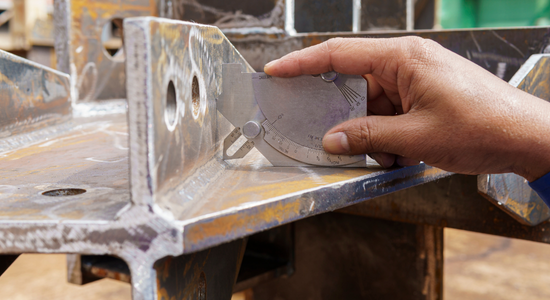
The processing capability of Automatic Copper Knurling for precision parts includes high-speed, automated operations that ensure consistent and precise knurling patterns on copper materials. The process can accommodate various knurling designs and geometries, with the ability to handle small to large production runs. Advanced machinery allows for tight tolerance control, ensuring that each part meets the required specifications. The process also offers flexibility in handling different copper alloys and thicknesses, providing a high level of customization for diverse mechanical applications, all while maintaining optimal surface finish and durability.
Additional processes
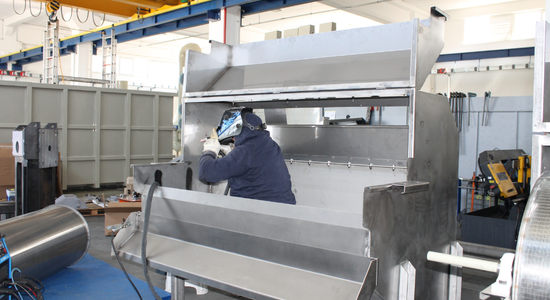
Additional processes for Automatic Copper Knurling for precision parts may include surface treatments such as anodizing or coating to enhance corrosion resistance and durability. Post-knurling finishing processes, such as polishing or deburring, ensure a smooth and clean surface free from any sharp edges or imperfections. Heat treatment may also be applied to improve material strength and hardness, while precision machining ensures dimensional accuracy and a perfect fit for assembly. These additional processes help further refine the part, ensuring it meets all functional, aesthetic, and durability requirements for high-performance applications.