Product Description
The XR-ARM-A3 six-degree-of-freedom robotic arm is an industrial weapon that combines advanced technology with excellent performance. It has flexible and precise six-degree-of-freedom motion capabilities, can easily complete complex trajectory operations, and has high repeatability. The powerful load capacity enables it to handle workpieces of various weights, and high-speed and stable joint movement ensures efficient operation. The body structure is made of high-quality materials to create a sturdy and durable structure, and is equipped with intelligent programming and control systems. It is easy to operate and can be widely used in industrial manufacturing, scientific research experiments, logistics warehousing and other fields, providing reliable support for the automation upgrade of various industries and helping enterprises improve production efficiency and competitiveness.
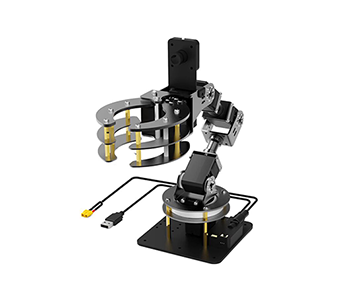
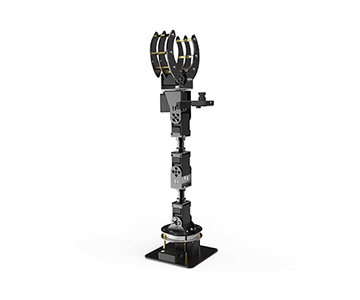
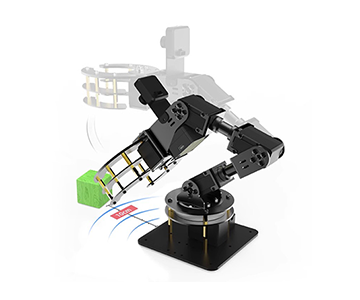
Product parameters
Overall parameters | |||
---|---|---|---|
Product name | XR 6-DOF Robotic Arm | Model | XR-ARM-A3 |
Product size | 270*110*260mm | Weight | 940g |
Lifting weight | 500g | Material | Aluminum alloy |
Surface treatment | Anodized | Control method | Kinematics/inverse kinematics |
Power supply method | XT30 | Communication interface | usart serial bus |
Degree of freedom | 6-DOF | Camera | USB2.0 CAM RBG 1080P |
Robotic arm steering gear parameters | |||
---|---|---|---|
Model | XRHS300 | Working range voltage | 8.4-12.6V |
Quiescent current | 150mA | current | 170mA |
Speed | 0.13ses/60° | rated torque | 0.37kgf·cm |
Locked rotor current | 800mA | stall torque | 25kgf·cm |
Mechanical limit angle | 360° | operating angle | 90°±10° |
Product Display
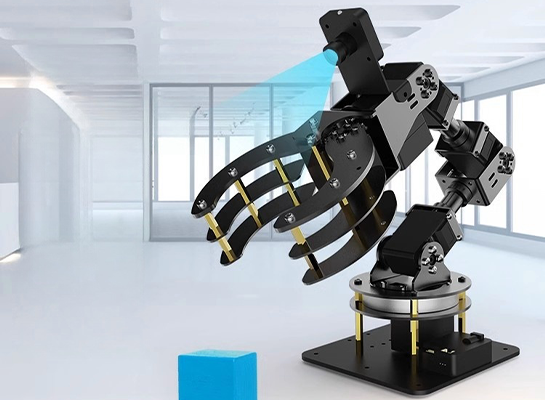
- High-precision serial bus servo motor
- Open source inverse kinematics algorithm for precise positioning
- Lifting weight up to 500g
- Compatible with "Jueying" robot dog, ready to use
- Python language SDK for easy calling
- Precise rotation angle
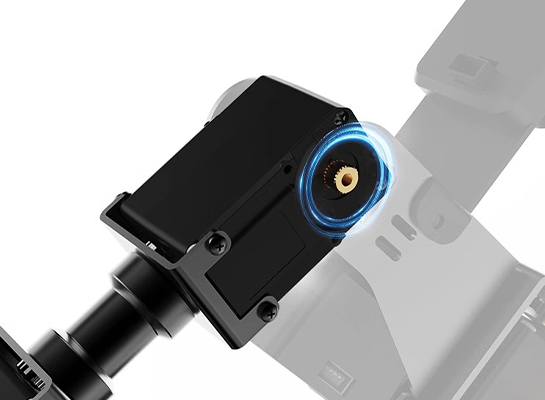
25KG high precision serial bus servo
The robot arm uses 6 high-precision serial buses unique to XiaoR Technology
Servo motor (4 joints + 1 horizontal rotation + 1 gripper)
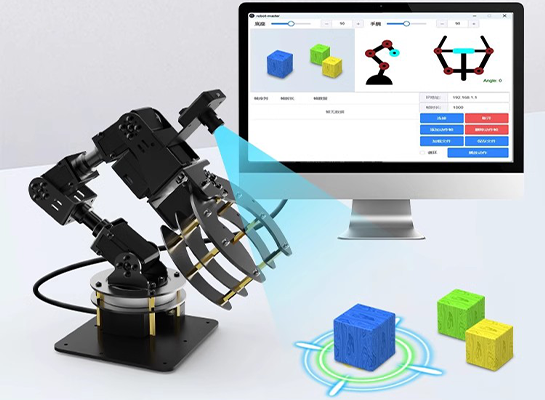
hand-eye unity
RGB camera
It can be connected to the main control through the USB interface, and can be used with embedded Linux systems such as Jetson Nano and Raspberry Pi to easily obtain camera data, and drive the robotic arm to move according to the data processing results to achieve the "hand-eye integration" effect.
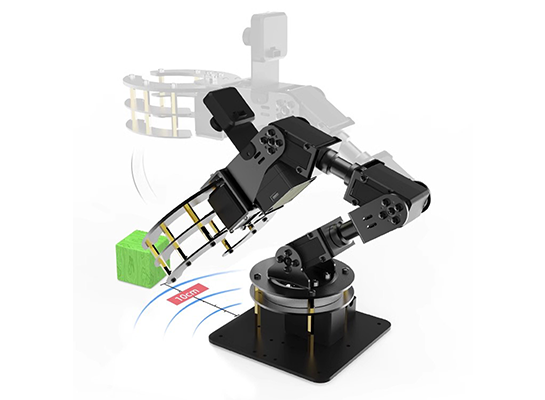
Using inverse kinematics algorithms
Precise positioning of the end effector
Provide Python version source code for easy calling and secondary development
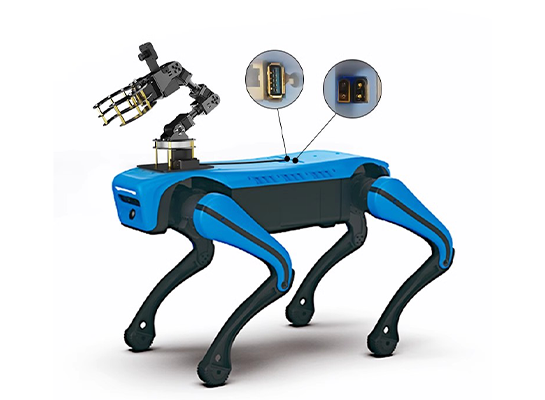
Power supply and camera interface
Directly matches the robot dog interface
The robot arm uses the XT30 interface for power supply, which is directly plugged into the 12V power interface on the back of the Jueying robot dog;
The robot arm camera uses the USB2.0 interface, which is directly plugged into the USB interface on the back of the Jueying robot dog.
Size & Interface
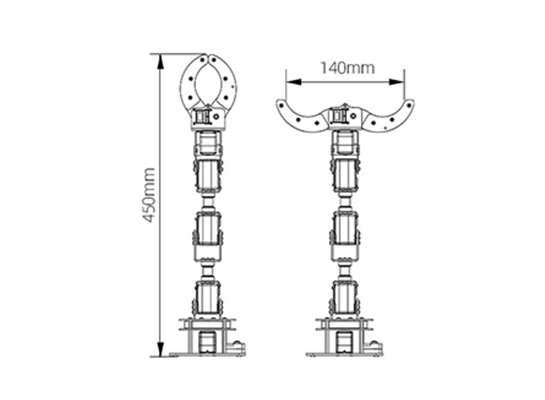
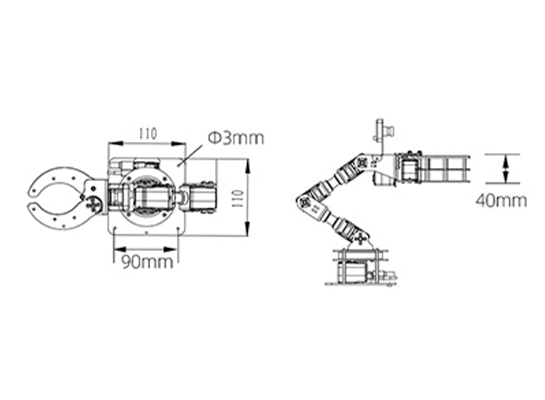
Application Cases
On the stage of various robot competitions, this combination of six-degree-of-freedom robotic arm gripper, RGB camera and compatible Jueying robot dog shines. In the simulated industrial production scene, the six degrees of freedom of the robotic arm enables it to flexibly simulate the assembly process of parts and components, accurately grasp and place tiny parts, and the RGB camera clearly captures the position and posture information of the parts to ensure that the operation is accurate to the millimeter; in the search and rescue simulation, the robotic arm gripper can quickly grasp the rescue supplies and accurately deliver them to the designated area, and the camera timely scans the surrounding environment to guide the Jueying robot dog and help it cross complex terrain. The three work closely together to efficiently complete the task, fully demonstrating its high adaptability and excellent performance in the complex and changeable competition environment, becoming a powerful assistant for many participating teams in their pursuit of victory, and also providing a vivid practical sample for the development of robotics technology in practical applications.
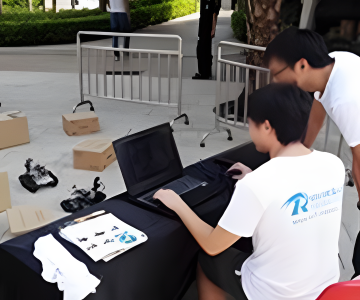
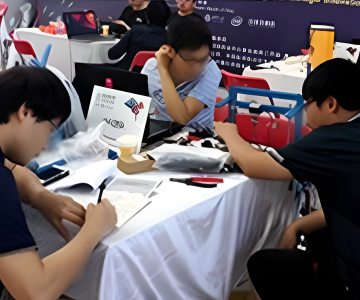
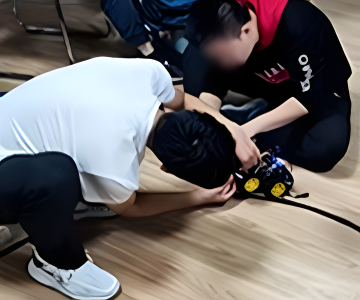
Service
Customized development and mass production of software and hardware product solutions for pipeline video inspection, bomb disposal, and survey robots for wind power, municipal administration, power and other industries.
Customized development and mass production of teaching and training software and hardware products based on common open source platforms such as Micro:bit and Raspberry Pi.
Customized development and mass production of other industrial control system software and hardware product solutions based on Internet of Things technology (ODM, OEM).