Product Description
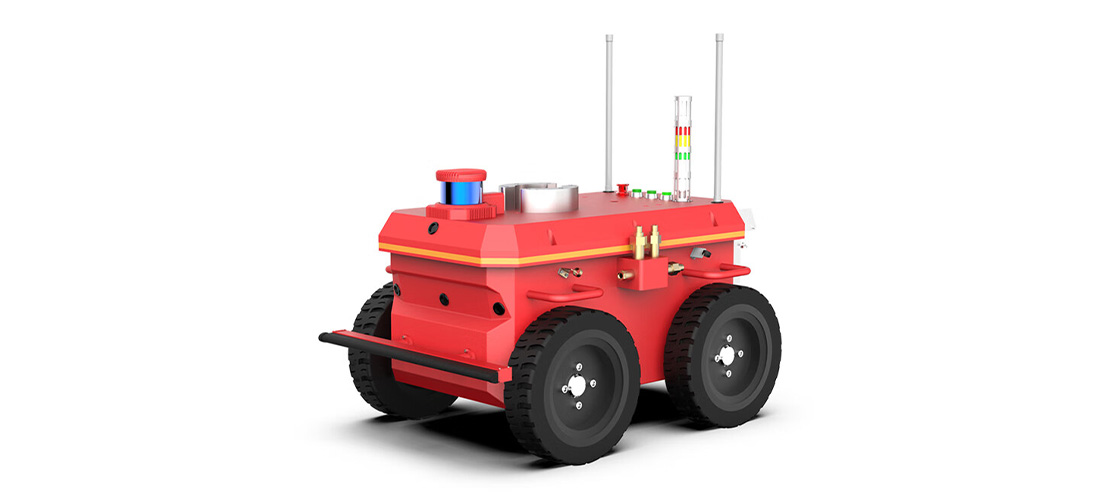
The autonomous navigation robot platform is a hazard all-scene platform solution with functions such as modular mapping, positioning, autonomous navigation, path planning, and autonomous obstacle avoidance in special hazardous scenarios, and supports multi-scene application expansion and modular loading. The autonomous navigation robot builds a modular robot platform for dangerous special scenarios, and supports the integration of various applications to provide professional and reliable data acquisition and composite operation robot platform for dangerous special scenarios such as combustible gas, dust environment, train oil, petrochemical plant, gas station, hydrogen refueling station, ammunition depot, dangerous terminal and other scenarios.
Product Features
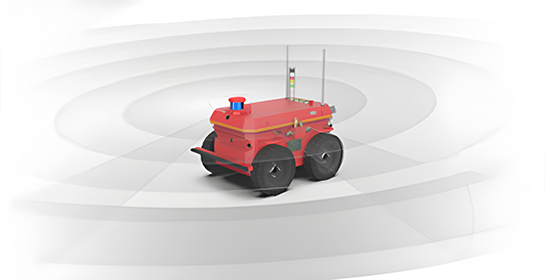
Level L4 closed scene autonomous navigation
Overall software architecture environment awareness algorithm
Planning decision algorithm Low-level control algorithm
Navigation and positioning algorithm
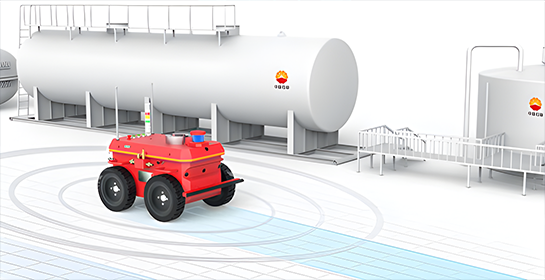
AUTO MS Indicates the automatic navigation function points
Map building: Accurate 2D/3D environment map building
Precise positioning: centimeter-level positioning accuracy
Autonomous navigation: Plan reasonable paths from point to point
Path planning: The APP directly draws the expected path
Intelligent routing: actively generates a local routing path
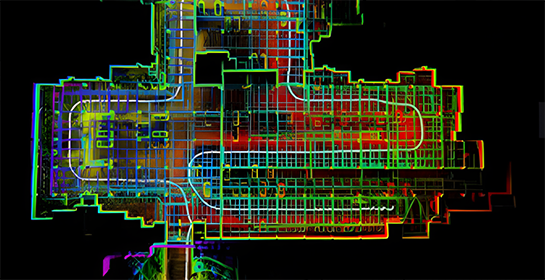
Autonomous charging: Given the charging task, complete the charging docking independently
Fixed point setting: Multiple task points and charging points can be set
Path combination: Combine multiple paths based on actual requirements
Map editing: Draw virtual walls to clearly navigate restricted areas
Standard SDK: Users can integrate the autonomous driving API interface based on the YUHESEN autonomous navigation robot platform to achieve rapid secondary development
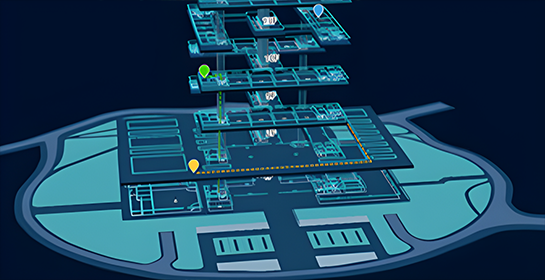
AUTO MS Autonomous navigation robot platform configuration description:
Sensing hardware: 16-wire Lidar, ultrasonic radar,
Communication hardware: vehicle level CAN communication, gigabit network interaction platform,
Computing hardware: Multi-redundancy supercomputer BOX platform (NVIDIA/INTEL),
Platform hardware :FB-001 modular robot platform,
Application software :AUTO MS APP(Android)/ Standard secondary Development SDK.
Structure Diagram
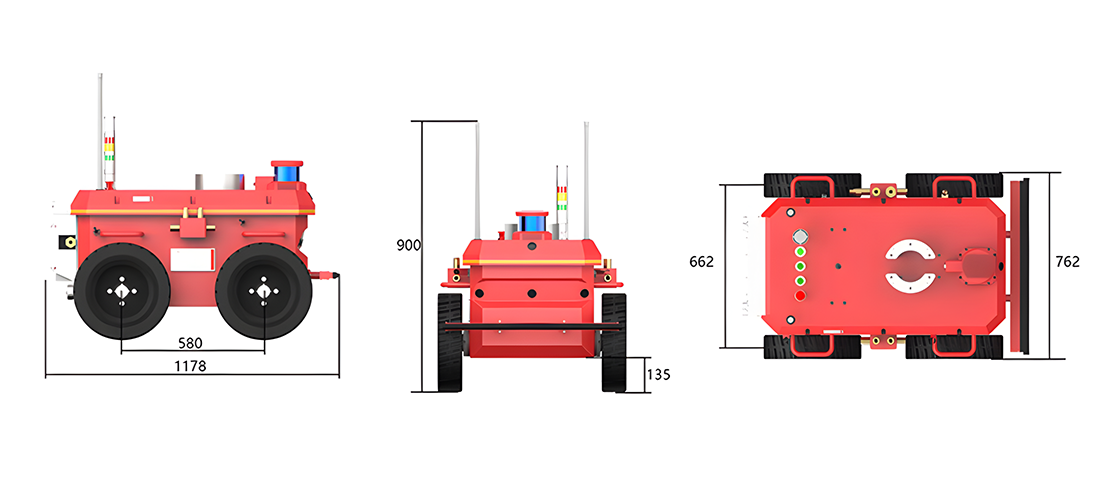
Product parameters
name | argument |
---|---|
Design size | 1178*762*900mm |
Vehicle mass | 270kg |
Structural form | Four-wheel differential |
Chassis main material | Q235 |
Ground clearance | 135mm |
wheelbase | 580mm |
Wheel track | 662mm |
Tyre diameter | 400mm |
Drive motor | 1000W*4, DC servo motor |
battery | 36V/60AH |
Charging time | 3-4h |
Charging mode | 36V/18A manual -36V/6A wireless charging |
Operating temperature | -20°C-60°C |
Braking mode | Motor braking |
Parking mode | Motor parking |
Communication mode | CAN 2.0B |
Kinematic analysis | √ |
Remote control distance | 50m |
Operating speed | 4.5 km/h |
range | 15km |
Fording depth | 140mm |
Maximum Angle of climb | 15 ° |
Obstacle clearance height | Full load 80mm |
Class of protection | IP65 |
Our Factory
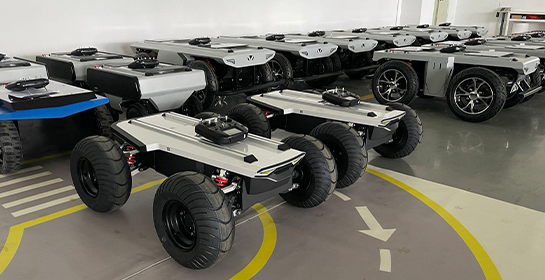
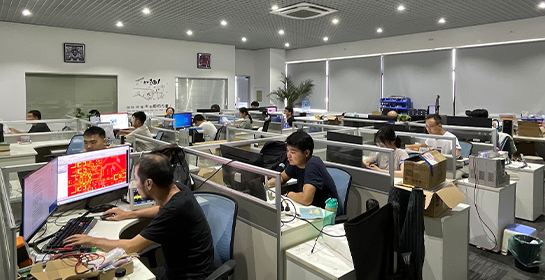
Product Certificate
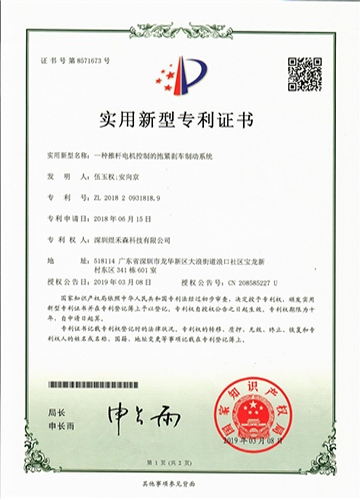
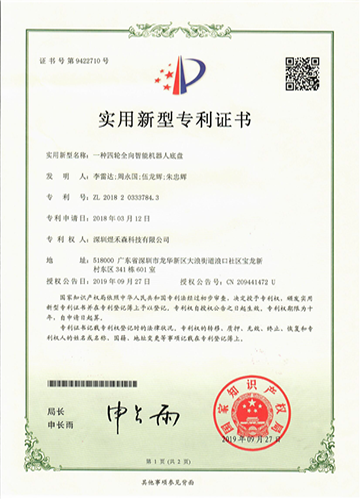
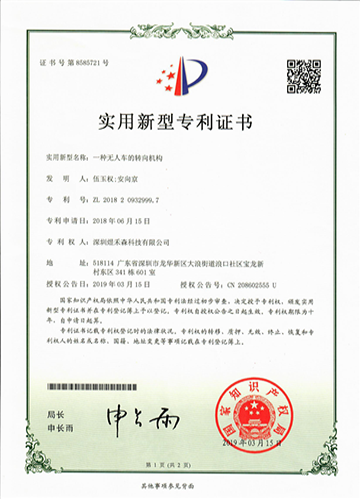
Exhibition & Strength
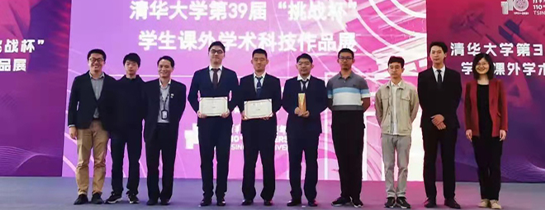
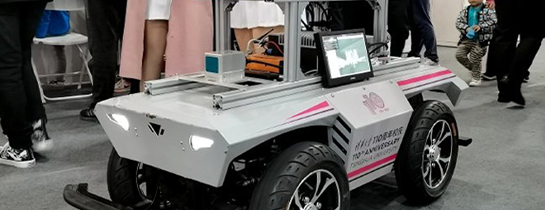
Service
Pre-sale - help reasonable selection
Project evaluation engineers docking, in-depth communication to understand the operating conditions, to confirm the appropriate type selection and specifications, to give customers reasonable suggestions, effectively avoid problems in production.
In sale - Guarantee production delivery
Dedicated engineers and business specialists docking, project managers to process control, active communication and interaction, timely detection of problems and timeliness communication for production delivery escort.
After-sales - Timely response processing
After-sales engineering personnel docking, the same day response; And timely to the scene to confirm, discuss, solve and deal with problems, to meet customer production needs, to avoid downtime and production.