Product Description
High precision rocker arm, manufactured with a carefully controlled forging process, provides exceptional strength and durability while ensuring optimal engine efficiency. Designed to withstand high stress and extreme operating conditions, it enhances valve control, reduces friction, and improves overall engine longevity.
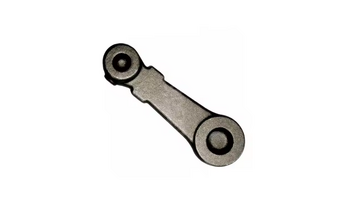
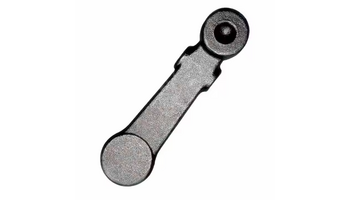
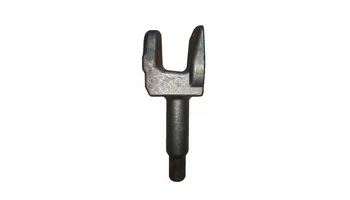
Product parameters
Item Name | Custom Forging Parts |
Size | As per approval product drawings. |
DRW Format | DWG, PDF, IGS, STEP, SLDPRT, SLDDRW, PRT, DRW, DXF, X_T, etc... |
Weight | 0.1-200 kg |
Material | Differenty types of Steels, Carbon Steel, Stainless Steel, Alloy Steel etc;Aluminum alloy, copper alloy, titanium alloy, tungsten molybdenum alloy and other non-ferrous metals. |
Application | Industry Equipments, Autos, Construction machinery Parts, Agricultural machinery, Railway relevant Parts, Petrochemical machinery, Mining machinery, The power industry. |
Surface Treatment | Self color, Polishing, Painting, Powder Coating, Electrophoretic Coating, Anodizing, Nickel Plating, Zinc Plating, Hot dip Galvanizing etc. |
Quality Control | 1.Raw Materials Test, include chemical composition and size; |
2.Random inspection during production; | |
3.Final products size test, with measurement tools, special gauges and Coordinate instrument if needed; | |
4.Final products Strenght and Hardness test, to guarantee the mechanical property; | |
5.Assembly and Function test, with special testing gauges; | |
6.Packing test | |
Packing | Plastic bags, Cartons, Racks, Plywood Cases etc. |
Logistics | Shipping, Air Flight, International Express etc. |
Custom Process
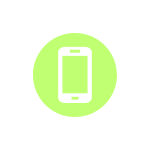
1.send inquiries
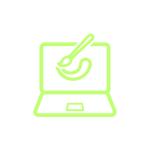
2.drawings or samples
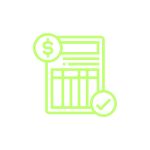
3. Quotation
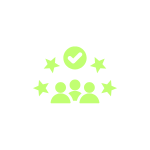
4.customer confirmation
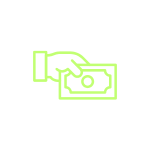
5. places order and pays
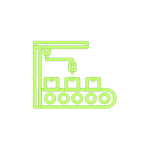
6.Mass production
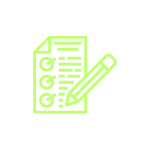
7.Test before packaging
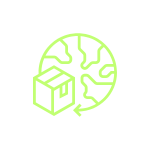
8.Shipping & confirmation
Process Type
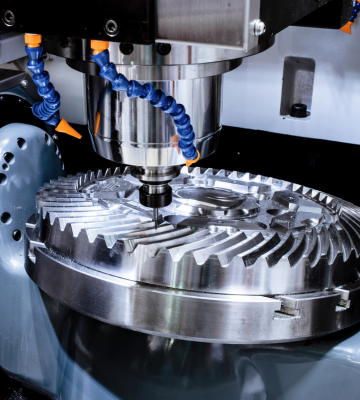
Wood Cutting Machines
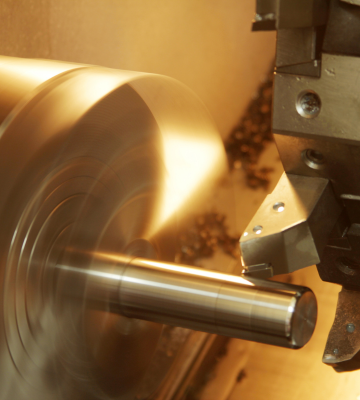
Lathes
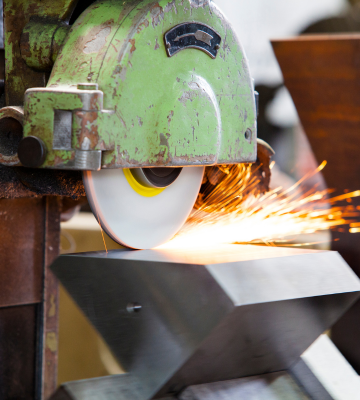
CNC Milling Machines
Material
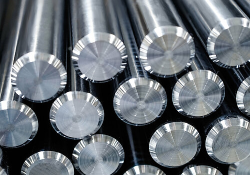
Stainless Steel
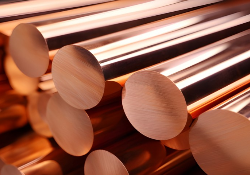
Copper
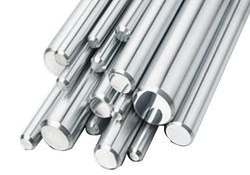
Aluminu Alloy
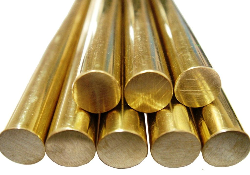
Brass
Quality Control
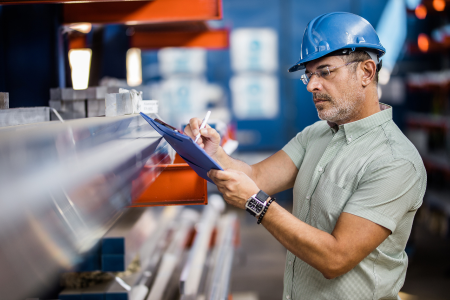
The quality control of the High-Accuracy Lift Arm involves a meticulous inspection process to ensure precision, strength, and durability. Every unit undergoes rigorous dimensional checks, material composition analysis, and surface integrity testing to meet strict industry standards. Advanced manufacturing techniques, including controlled forging and heat treatment, enhance structural integrity and resistance to wear. Non-destructive testing methods are applied to detect any internal defects, ensuring flawless performance.
Processing capability
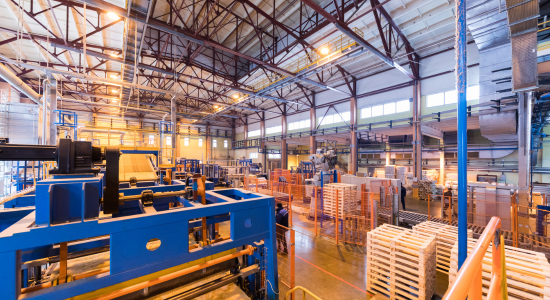
The processing capability of the High-Accuracy Lift Arm combines advanced forging, precision machining, and heat treatment to achieve superior strength and durability. Utilizing high-precision equipment, the manufacturing process ensures tight dimensional tolerances and consistent quality. Surface treatments and coatings are applied to enhance wear resistance and corrosion protection, making the lift arm suitable for demanding environments. Stringent quality control measures, including non-destructive testing, ensure structural integrity and performance reliability.
Additional processes
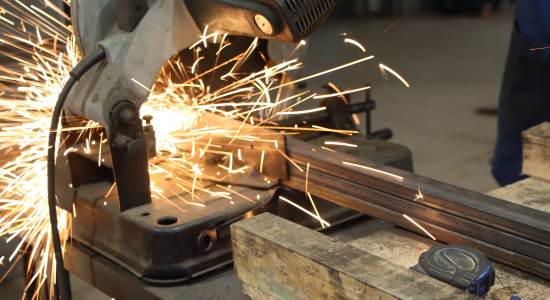
The additional processes of the High-Accuracy Lift Arm include advanced surface treatments to enhance durability and corrosion resistance, precision grinding to achieve tight dimensional tolerances, and heat treatment to optimize strength and wear resistance. Non-destructive testing methods such as ultrasonic and magnetic particle inspection ensure structural integrity and defect-free components. Final finishing processes, including deburring and polishing, improve surface smoothness and reduce friction for optimal performance.