Product Description
Electrical insulator molding provides exceptional strength, resistance to pressure, and environmental durability, making it an ideal choice for power distribution systems. Designed to withstand extreme weather conditions, high electrical stress, and mechanical loads, it plays a critical role in maintaining the stability and reliability of electrical networks. By effectively insulating and preventing electrical faults, it helps to increase safety, reduce the risk of power outages, and enhance overall system efficiency.
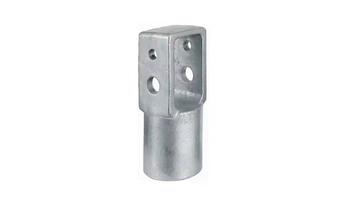
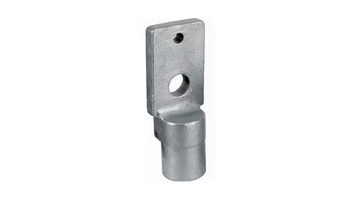
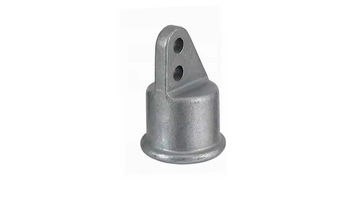
Product parameters
Surface Treatment | Self color, Polishing, Painting, Powder Coating, Electrophoretic Coating, Anodizing, Nickel Plating, Zinc Plating, Hot dip Galvanizing etc. |
Material | Differenty types of Steels, Carbon Steel, Stainless Steel, Alloy Steel etc;Aluminum alloy, copper alloy, titanium alloy, tungsten molybdenum alloy and other non-ferrous metals. |
Process | Die Forging, Free Forging, Hot forging, Cold forging, Heat Treatment, Machining, Surface Treatment etc. |
Service | Custom OEM/ODM metal parts processing, Whole Product assembly, 2D & 3D drawings design, International Delivery Logistics, Serivce before & after sales etc. |
Custom Process
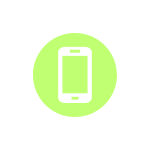
1.send inquiries
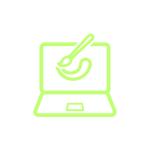
2.drawings or samples
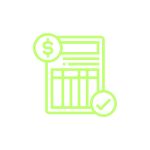
3. Quotation
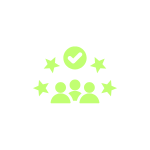
4.customer confirmation
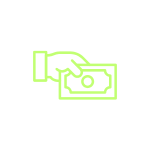
5. places order and pays
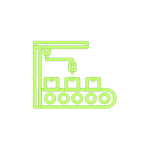
6.Mass production
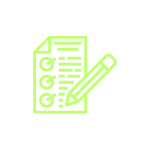
7.Test before packaging
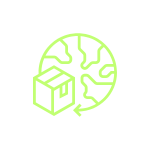
8.Shipping & confirmation
Process Type
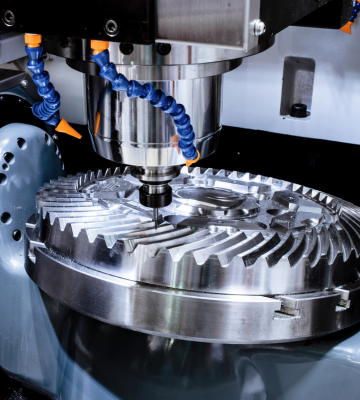
Wood Cutting Machines
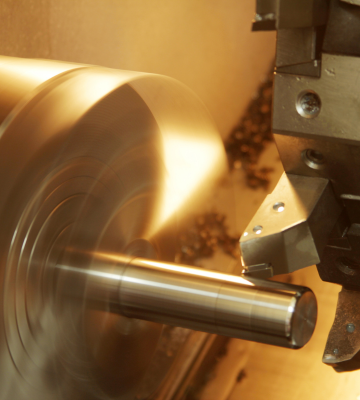
Wood Cutting Machines
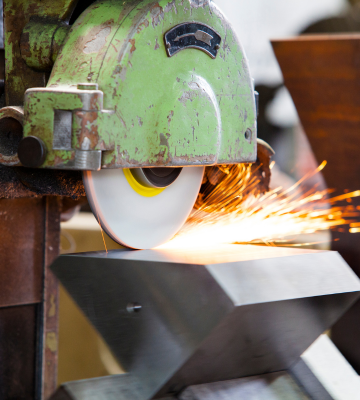
Wood Cutting Machines
Material
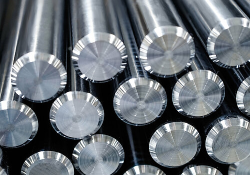
Stainless Steel
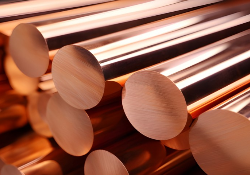
Copper
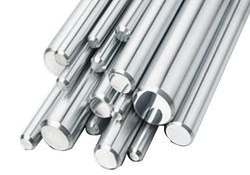
Aluminu Alloy
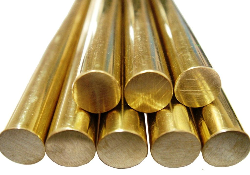
Brass
Quality Control
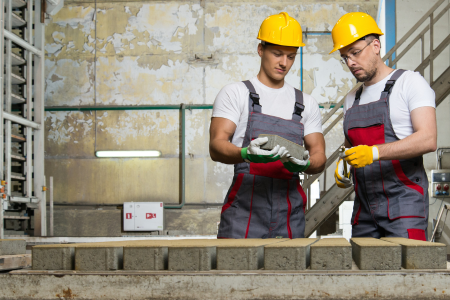
The quality control of Power Station Insulator Forgings ensures that each component meets the highest standards of strength, reliability, and performance. Every stage of the manufacturing process, from forging to final inspection, is carefully monitored for precision and consistency. The material composition is analyzed to guarantee optimal properties, while dimensional accuracy is verified through advanced measurement techniques. Surface integrity is checked for defects, and heat treatment processes are precisely controlled to enhance mechanical properties. Non-destructive testing, such as ultrasonic and magnetic particle inspection, is conducted to detect any internal flaws, ensuring the insulators are free from defects and meet industry safety requirements.
Processing capability
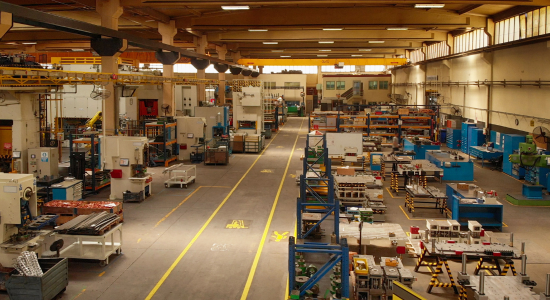
The processing capability of Power Station Insulator Forgings encompasses a range of advanced manufacturing techniques to produce high-quality, durable components. Precision forging ensures the insulators are formed with tight tolerances, providing the necessary strength to withstand electrical and mechanical stresses. The forging process is followed by precise machining to achieve the required dimensional accuracy, ensuring a perfect fit in power station applications.
Additional processes
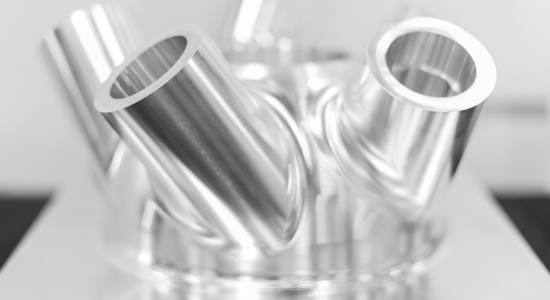
Additional processes of Power Station Insulator Forgings include advanced surface treatments such as coating and polishing to enhance resistance to corrosion, wear, and environmental damage. After forging, each component undergoes precise machining to achieve the necessary dimensional accuracy and smoothness. Heat treatment is applied to optimize the material’s mechanical properties, ensuring higher strength and durability. Non-destructive testing methods like ultrasonic and x-ray inspections are used to detect any internal defects, ensuring the insulators meet safety and performance standards.