产品描述
直流无刷电机是由驱动板电子换向驱动的三相永磁同步电机,运行安静,转速高,转矩大,使用寿命长。直流无刷电机直径从16mm到65mm,最大功率可达400W,电机采用了先进的无齿槽结构线圈。这种结构设计具有显著优势,在消除齿槽转矩带来的负面影响的同时,极大地提升了电机的效率以及功率密度。这意味着电机在消耗相同电量的情况下,能够输出更强大的动力,并且在有限的空间内实现更高的功率输出。直流无刷电机特别适用于那些需要长期连续运行的应用场景。同时,对于对控制精度以及可靠性有着较高要求的领域,如工业自动化设备、高端医疗器械等,直流无刷电机同样能够凭借自身优势,稳定且高效地运行,为相关设备的稳定运行和精准控制提供有力支持 。
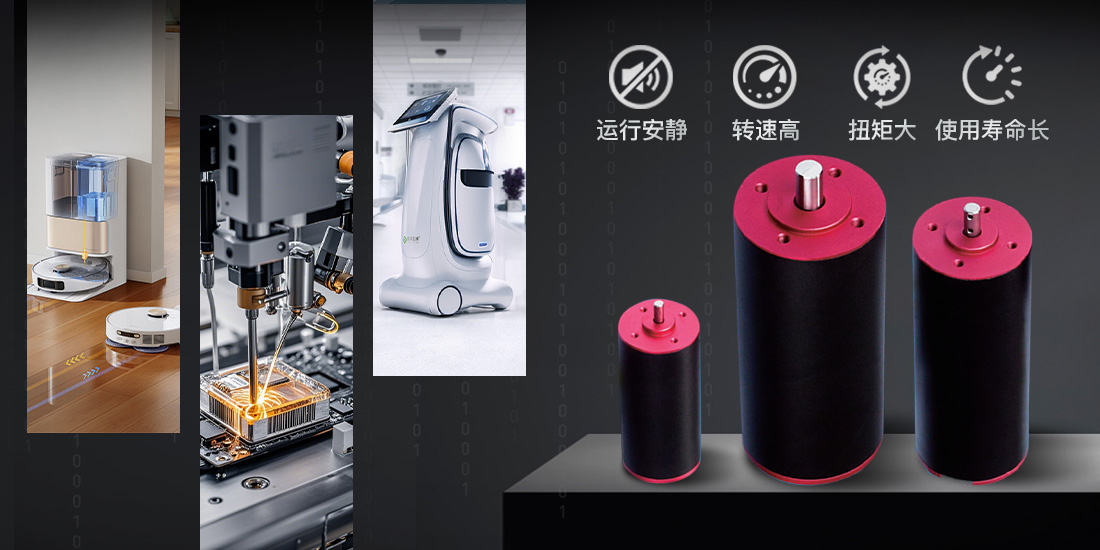
产品参数
无刷电机 滚珠轴承 | |||||||||
型号 | 1220 | 1220 | 1214 | 1827 | 1817 | 2420 | 2416 | ||
额定电压 | V | 12 | 12 | 12 | 18 | 18 | 24 | 24 | |
空载转速 ±12% | rpm | 19822 | 19822 | 13840 | 26874 | 17253 | 19613 | 16063 | |
空载电流 Max150% | mA | 85 | 85 | 60 | 77 | 49 | 42 | 35 | |
连续运行推荐 极限值 | 最大连续转矩 | mN.m | 3 | 3 | 3.2 | 2.2 | 3.1 | 2.8 | 3.1 |
额定转速 | rpm | 16809 | 16809 | 10528 | 24516 | 14233 | 16854 | 13135 | |
最大连续电流 | mA | 600 | 600 | 450 | 420 | 360 | 280 | 250 | |
额定功率 | W | 5.26 | 5.26 | 3.56 | 5.63 | 4.61 | 4.91 | 4.22 | |
启动电流 | mA | 3947 | 3947 | 1881 | 4787 | 2050 | 1990 | 1371 | |
堵转转矩 | mN.m | 23 | 23 | 16 | 31 | 20 | 23 | 20 | |
最大输出功率 | W | 11.8 | 11.8 | 5.6 | 21.5 | 9.2 | 11.9 | 8.2 | |
最高效率值 | % | 73 | 73 | 67 | 76 | 71 | 73 | 71 | |
端电阻 ±12% | Ω | 3.04 | 3.04 | 6.38 | 3.76 | 8.78 | 12.06 | 17.5 | |
电感 (1KHZ) | mH | 0 | 0 | 0 | 0 | 0 | 0 | 0 | |
机械时间常数 | ms | 2.73 | 2.73 | 2.79 | 2.76 | 2.65 | 2.65 | 2.58 | |
转动惯量 | gcm2 | 0.3 | 0.3 | 0.3 | 0.3 | 0.3 | 0.3 | 0.3 | |
转矩常数 | mN.m/A | 5.78 | 5.78 | 8.28 | 6.4 | 9.96 | 11.69 | 14.27 | |
转速常数 | rpm/V | 1652 | 1652 | 1153 | 1493 | 958 | 843.5 | 820.9 | |
速度/转矩 斜率 | rpm/mN.m | 868.6 | 868.6 | 888.7 | 877.7 | 844.7 | 254 | 232 | |
电机重量 | g | 32.6 | 32.6 | 32.6 | 32.6 | 32.6 | 32.6 | 32.6 |
相关信息 | ||||||
电机热阻 | 22.5 K/W | 电机热时间常数 | 407 S | |||
动态荷载:轴向 | 1.5 N | 动态荷载:径向(端面外5mm) | 6.0 N | |||
最大安装力(静态) | 40 N | 安装螺丝最大旋入深度 | 3.0 mm | |||
径向间隙(端面外5mm) | ≤0.02 mm | 轴向间隙 | 0 (<2.0N ) | |||
线圈最高温度 | 85ºC | 环境温度 | -30 to 65ºC | |||
标准后轴直径 | 2 mm | 标准后轴长度”L | 0/3.7/5.5 mm | |||
引线定义(AWG 26#) | 减速电机总长: LT=L1+L2+L3 | BL1632AN 推荐组合选配方案 | ||||
引线 1 :黄色 电机绕组 A | L1:16GP | L1:19GP | L2:BL16 | L3:EN16T | L3:EN16S | |
引线 2:红色 电机绕组 B | 15.9 | 18.8 | 32 | 12 | 10.7 | |
引线 3:蓝色 电机绕组 C | 19.6 | 23.6 | ||||
传感插件脚定义(AWG 28#) Molex:51021-0500 | 23.3 | 28.4 | ||||
27 | 33.2 | |||||
插件脚 1 :棕色 霍尔Vcc 3~16V | ||||||
插件脚 2:黑色 霍尔 GND | 注:客户可选择相应的齿轮箱与编码器来与电机搭配,更多产品组合请联系咨询我司销售人员。 | 推荐齿轮箱:推荐编码器: | ||||
插件脚 3:黄色 霍尔 A | ||||||
插件脚 4:红色 霍尔 B | ||||||
插件脚 5:蓝色 霍尔 C | ||||||
电机数据在25℃标准测试环境中测得。 电机超过连续最大推荐参数运行可能造成寿命缩减或导致电机损坏。 在高温环境中,必须降低负载电流以保护电机。 |
无刷电机 滚珠轴承 | ||||||||||
型号 | 1234 | 1221 | 1216 | 1836 | 1821 | 1816 | 2419 | 2413 | ||
额定电压 | V | 12 | 12 | 12 | 18 | 18 | 18 | 24 | 24 | |
空载转速 ±12% | rpm | 34200 | 21000 | 16400 | 36300 | 20900 | 16160 | 19400 | 12600 | |
空载电流 Max150% | mA | 200 | 120 | 80 | 150 | 75 | 60 | 50 | 40 | |
连续运行推荐 | 最大连续转矩 | mN.m | 4.6 | 5.8 | 6.3 | 3.5 | 5.7 | 6.2 | 6.2 | 6.4 |
顿定转速 | rpm | 31782 | 17888 | 13242 | 34513 | 17874 | 13027 | 16136 | 9133 | |
最大连续电流 | mA | 1600 | 1200 | 1000 | 900 | 780 | 650 | 580 | 400 | |
额定功率 | W | 15.5 | 10.9 | 8.8 | 12.7 | 10.7 | 8.4 | 10.4 | 6.1 | |
启动电流 | mA | 20000 | 7407 | 4858 | 15385 | 4945 | 3103 | 3200 | 1348 | |
堵转转矩 | mN.m | 66 | 39 | 33 | 71 | 39 | 32 | 37 | 23 | |
最大输出功率 | W | 58.8 | 21.5 | 14.1 | 67.9 | 21.6 | 13.4 | 18.6 | 7.6 | |
最高效率值 | % | 81 | 76 | 76 | 81 | 77 | 74 | 77 | 69 | |
端电阻 ±12% | Q | 0.6 | 1.62 | 2.47 | 1.17 | 3.64 | 5.8 | 7.5 | 17.8 | |
电感 (1KHz) | mH | 0.032 | 0.1 | 0.16 | 0.08 | 0.24 | 0.38 | 0.49 | 1.05 | |
机械时间常数 | ms | 2.2 | 2.3 | 2.1 | 2.2 | 2.3 | 2.2 | 2.3 | 2.3 | |
转动惯量 | gcm² | 0.41 | 0.41 | 0.41 | 0.41 | 0.41 | 0.41 | 0.41 | 0.41 | |
转矩常数 | mN.m/A | 3.3 | 5.4 | 6.9 | 4.7 | 8.1 | 104 | 11.6 | 17.6 | |
转速常数 | rpm/N | 2879 | 1779 | 1390 | 2037 | 1179 | 915 | 821 | 541 | |
速度/转矩斜率 | rpm/mN.m | 520.7 | 536.8 | 499.4 | 508.2 | 529.8 | 509.0 | 529.6 | 545.7 | |
电机重量 | g | 42.2 | 42.1 | 41.8 | 42.1 | 42.2 | 41.8 | 41.9 | 41.8 |
相关信息 | |||||||
电机热阻 | 17.9KW | 电机热时间常数 | 439S | ||||
动态荷载:轴向 | 1.5N | 动态荷载:径向(端面外5mm) | 6.0 N | ||||
最大安装力(静态) | 40N | 安装螺丝最大旋入深度 | 3.0 mm | ||||
径向间隙(端面外5mm) | ≤0.02 mm | 轴向间隙 | 0(<2.0N) | ||||
线圈最高温度 | 85℃ | 环境温度 | -30 to 65℃ | ||||
标准后轴直径 | 2 mm | 标准后轴长度”L" | No mm | ||||
引线定义(AWG 24#) | 减速电机总长: LT=L1+L2+L3 | BL1640AN 推荐组合选配方案 | |||||
引线 1 :黄色 电机绕组 A | L1:16GP | L1:19GP | L2:BL16 | L3:EN16S | L3:EN16T | ||
引线 2:红色 电机绕组 B | 15.9 | 18.8 | 40 | 10.7 | 12 | ||
引线 3:蓝色 电机绕组 C | 19.6 | 23.6 | |||||
传感插件脚定义(AWG 28#) Molex:51021-0500 | 23.3 | 28.4 | |||||
27 | 33.2 | ||||||
插件脚 1 :棕色 霍尔Vcc 3~16V | |||||||
插件脚 2:黑色 霍尔 GND | 注:客户可选择相应的齿轮箱与编码器来与电机搭配,更多产品组合请联系咨询我司销售人员。 | 推荐齿轮箱: | 推荐编码器: | ||||
插件脚 3:黄色 霍尔 A | |||||||
插件脚 4:红色 霍尔 B | |||||||
插件脚 5:蓝色 霍尔 C | |||||||
电机数据在25℃标准测试环境中测得。 电机超过连续最大推荐参数运行可能造成寿命缩减或导致电机损坏。 在高温环境中,必须降低负载电流以保护电机。 |
无刷电机 滚珠轴承 | ||||||||
型号 | 1225 | 1220 | 1822 | 1819 | 2419 | 2415 | ||
额定电压 | V | 12 | 12 | 18 | 18 | 24 | 24 | |
空载转速 ±12% | rpm | 24525 | 19908 | 22265 | 18634 | 19339 | 14850 | |
空载电流 Max150% | mA | 200 | 200 | 120 | 100 | 90 | 70 | |
连续运行推荐 极限值 | 最大连续转矩 | mN.m | 2.3 | 4.2 | 2.9 | 4.5 | 3.6 | 4.6 |
额定转速 | rpm | 23581 | 18096 | 21080 | 16679 | 17806 | 12731 | |
最大连续电流 | mA | 700 | 900 | 500 | 600 | 400 | 380 | |
额定功率 | W | 5.7 | 8 | 6.4 | 7.9 | 6.7 | 6.2 | |
启动电流 | mA | 13187 | 8392 | 7258 | 4865 | 4000 | 2243 | |
堵转转矩 | mN.m | 60 | 47 | 54 | 43 | 45 | 32 | |
最大输出功率 | W | 38.4 | 24.3 | 31.6 | 21 | 22.9 | 12.6 | |
最高效率值 | % | 77 | 75 | 76 | 73 | 72 | 68 | |
端电阻 ±12% | Ω | 0.91 | 1.43 | 2.48 | 3.7 | 6 | 10.7 | |
电感 (1KHZ) | mH | 0.07 | 0.11 | 0.19 | 0.29 | 0.47 | 0.86 | |
机械时间常数 | ms | 3 | 3.1 | 3 | 3.1 | 3.1 | 3.3 | |
转动惯量 | gcm2 | 0.69 | 0.69 | 0.69 | 0.69 | 0.69 | 0.69 | |
转矩常数 | mN.m/A | 4.6 | 5.7 | 7.6 | 9 | 11.6 | 15 | |
转速常数 | rpm/V | 2075 | 1689 | 1258 | 1057 | 824 | 639 | |
速度/转矩 斜率 | rpm/mN.m | 410.4 | 427.3 | 410.8 | 432.9 | 427 | 457.1 | |
电机重量 | g | 52 | 52 | 52 | 52 | 52 | 52 |
相关信息 | |||||||
电机热阻 | 22.8K/W | 电机热时间常数 | 552S | ||||
动态荷载:轴向 | 2.5 N | 动态荷载:径向(端面外5mm) | 16.0 N | ||||
最大安装力(静态) | 50 N | 安装螺丝最大旋入深度 | 3.0 mm | ||||
径向间隙(端面外5mm) | ≤0.02 mm | 轴向间隙 | 0 (<4.0N ) | ||||
线圈最高温度 | 85ºC | 环境温度 | -30 to 65ºC | ||||
标准后轴直径 | 3mm | 标准后轴长度”L” | 0/3.7/5.5 mm | ||||
引线定义(AWG 24#) | 减速电机总长: LT=L1+L2+L3 | BL2032AN 推荐组合选配方案 | |||||
引线 1 :黄色 电机绕组 A | L1:19GP | L1:24GP | L2:BL20 | L3:EN16S | L3:EN16T | ||
引线 2:红色 电机绕组 B | 18.8 | 24 | 32 | 10.7 | 12 | ||
引线 3:蓝色 电机绕组 C | 23.6 | 34.3 | |||||
传感插件脚定义(AWG 28#) Molex:51021-0500 | 28.4 | 42.8 | |||||
33.2 | 51.3 | ||||||
插件脚 1 :棕色 霍尔Vcc 3~16V | |||||||
插件脚 2:黑色 霍尔 GND | 注:客户可选择相应的齿轮箱与编码器来与电机搭配,更多产品组合请联系咨询我司销售人员。 | 推荐齿轮箱: | 推荐编码器: | ||||
插件脚 3:黄色 霍尔 A | |||||||
插件脚 4:红色 霍尔 B | |||||||
插件脚 5:蓝色 霍尔 C | |||||||
电机数据在25℃标准测试环境中测得。 电机超过连续最大推荐参数运行可能造成寿命缩减或导致电机损坏。 在高温环境中,必须降低负载电流以保护电机。 |
无刷电机 滚珠轴承 | |||||||||
型号 | 1226 | 1220 | 1216 | 1820 | 1817 | 2420 | 2417 | ||
额定电压 | V | 12 | 12 | 12 | 18 | 18 | 24 | 24 | |
空载转速 ±12% | rpm | 26000 | 20360 | 16260 | 19500 | 17350 | 20000 | 16600 | |
空载电流 Max 150% | mA | 350 | 190 | 180 | 150 | 140 | 110 | 95 | |
连续运行推荐 极限值 | 最大连续转矩 | mN.m | 5.4 | 7.3 | 8.5 | 7.4 | 6.4 | 6.7 | 7.5 |
额定转速 | rpm | 24682 | 18605 | 14445 | 17760 | 15721 | 18454 | 14905 | |
最大连续电流 | mA | 1600 | 1500 | 1400 | 1000 | 800 | 700 | 650 | |
额定功率 | W | 14 | 14.2 | 12.8 | 13.7 | 10.6 | 12.9 | 11.8 | |
启动电流 | mA | 25000 | 15385 | 11111 | 9677 | 7171 | 7742 | 5530 | |
堵转转矩 | mN.m | 107 | 84 | 76 | 83 | 68 | 86 | 74 | |
最大输出功率 | W | 72.9 | 45 | 32.3 | 42.2 | 31 | 45.1 | 32 | |
最高效率值 | % | 78 | 79 | 76 | 77 | 74 | 78 | 76 | |
端电阻±12% | Ω | 0.48 | 0.78 | 1.08 | 1.86 | 2.51 | 3.1 | 4.34 | |
电感 (1KHz) | mH | 0.034 | 0.061 | 0.097 | 0.17 | 0.22 | 0.29 | 0.42 | |
机械时间常数 | ms | 2.9 | 2.9 | 2.5 | 2.8 | 3 | 2.7 | 2.7 | |
转动惯量 | gcm 2 | 1.13 | 1.13 | 1.13 | 1.13 | 1.13 | 1.13 | 1.13 | |
转矩常数 | mN.m/A | 4.6 | 5.6 | 6.9 | 8.7 | 9.7 | 11.3 | 13.6 | |
转速常数 | rpm/V | 2197 | 1718 | 1377 | 1100 | 983 | 845 | 704 | |
速度/转矩 斜率 | rpm/mN.m | 242.7 | 241.1 | 214.5 | 235.8 | 254 | 232 | 225.1 | |
电机重量 | g | 65.9 | 66.2 | 66.6 | 65.7 | 65.4 | 65.1 | 65.9 |
相关信息 | |||||||
电机热阻 | 15 K/W | 电机热时间常数 | 673 S | ||||
动态荷载:轴向 | 2.5 N | 动态荷载:径向(端面外5mm) | 16.0 N | ||||
最大安装力(静态) | 50 N | 安装螺丝最大旋入深度 | 3.0 mm | ||||
径向间隙(端面外5mm) | ≤0.02 mm | 轴向间隙 | 0 (<4.0N ) | ||||
线圈最高温度 | 85ºC | 环境温度 | -30 to 65ºC | ||||
标准后轴直径 | 3 mm | 标准后轴长度”L” | 0/3.7/5.5 mm | ||||
引线定义(AWG 24#) | 减速电机总长: LT=L1+L2+L3 | BL2040AN 推荐组合选配方案 | |||||
引线 1 :黄色 电机绕组 A | L1:19GP | L1:24GP | L1:24GP | L3:EN16S | L3:EN16T | ||
引线 2:红色 电机绕组 B | 18.8 | 24 | 24 | 10.7 | 12 | ||
引线 3:蓝色 电机绕组 C | 23.6 | 34.3 | 34.3 | ||||
传感插件脚定义(AWG 28#) Molex:51021-0500 | 28.4 | 42.8 | 42.8 | ||||
33.2 | 51.3 | 51.3 | |||||
插件脚 1 :棕色 霍尔Vcc 3~16V | |||||||
插件脚 2:黑色 霍尔 GND | 注:客户可选择相应的齿轮箱与编码器来与电机搭配,更多产品组合请联系咨询我司销售人员。 | 推荐齿轮箱: | 推荐编码器: | ||||
插件脚 3:黄色 霍尔 A | |||||||
插件脚 4:红色 霍尔 B | |||||||
插件脚 5:蓝色 霍尔 C | |||||||
电机数据在25℃标准测试环境中测得。 电机超过连续最大推荐参数运行可能造成寿命缩减或导致电机损坏。 在高温环境中,必须降低负载电流以保护电机。 |
应用
机器人直流无刷空心杯电机凭借其独特优势,在多领域广泛应用。在服务机器人领域,用于室内清洁机器人,轻巧机身搭配高效动力,灵活穿梭于家具间清扫;在医疗领域,助力手术辅助机器人精准操作器械,确保手术安全;工业场景里,可用于小型装配机器人,快速响应完成精密装配任务;教育娱乐方面,为智能玩具机器人赋予灵动动作,带来趣味互动体验;物流仓储中,能让分拣机器人迅速启停,高效分拣货物 。
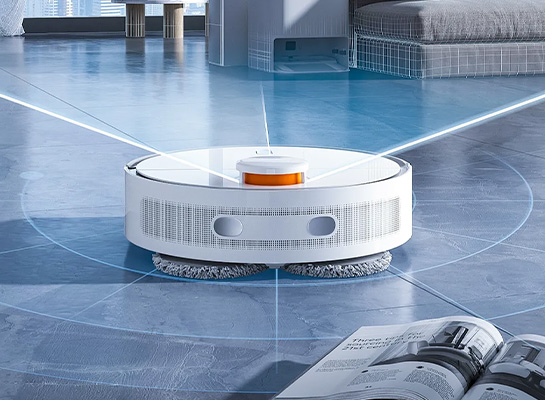
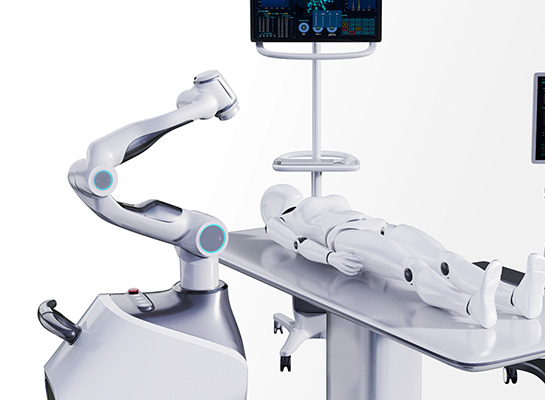
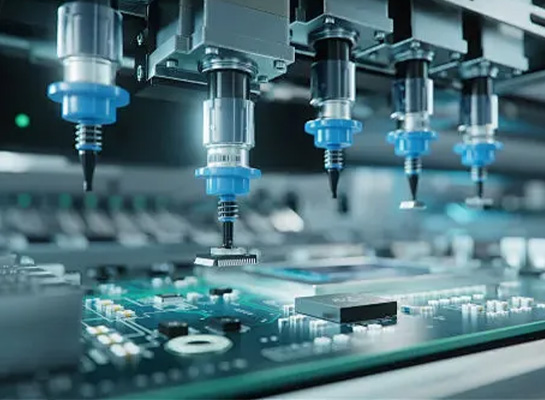
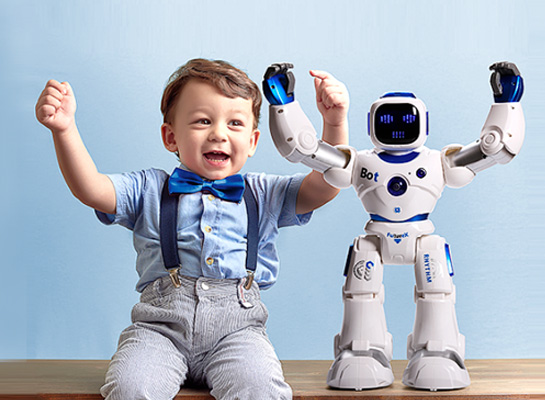