Product Description
Dc brushless motor is a three-phase permanent magnet synchronous motor driven by electronic commutation of the drive board, which has quiet operation, high speed, large torque and long service life. Dc brushless motor diameter from 16mm to 65mm, the maximum power up to 400W, the motor adopts advanced slotless structure coil. This structural design has significant advantages, while eliminating the negative effects of cogging torque, greatly improving the efficiency and power density of the motor. This means that the motor is able to output more powerful power while consuming the same amount of electricity, and achieve higher power output in a limited space. Dc brushless motors are particularly suitable for applications that require long-term continuous operation. At the same time, for areas with high requirements for control accuracy and reliability, such as industrial automation equipment, high-end medical devices, etc., DC brushless motors can also rely on their own advantages, stable and efficient operation, providing strong support for the stable operation and accurate control of related equipment.
Product parameters
Brushless motor Ball bearing | |||||||||
Model number | 1220 | 1220 | 1214 | 1827 | 1817 | 2420 | 2416 | ||
Rated voltage | V | 12 | 12 | 12 | 18 | 18 | 24 | 24 | |
No-load speed ±12% | rpm | 19822 | 19822 | 13840 | 26874 | 17253 | 19613 | 16063 | |
No-load current Max150% | mA | 85 | 85 | 60 | 77 | 49 | 42 | 35 | |
Recommended limit value for continuous operation | Maximum continuous torque | mN.m | 3 | 3 | 3.2 | 2.2 | 3.1 | 2.8 | 3.1 |
Rated speed | rpm | 16809 | 16809 | 10528 | 24516 | 14233 | 16854 | 13135 | |
Maximum continuous current | mA | 600 | 600 | 450 | 420 | 360 | 280 | 250 | |
Rated power | W | 5.26 | 5.26 | 3.56 | 5.63 | 4.61 | 4.91 | 4.22 | |
Starting current | mA | 3947 | 3947 | 1881 | 4787 | 2050 | 1990 | 1371 | |
Locked-rotor moment | mN.m | 23 | 23 | 16 | 31 | 20 | 23 | 20 | |
Maximum output power | W | 11.8 | 11.8 | 5.6 | 21.5 | 9.2 | 11.9 | 8.2 | |
Maximum efficiency value | % | 73 | 73 | 67 | 76 | 71 | 73 | 71 | |
End resistance ±12% | Ω | 3.04 | 3.04 | 6.38 | 3.76 | 8.78 | 12.06 | 17.5 | |
inductance (1KHZ) | mH | 0 | 0 | 0 | 0 | 0 | 0 | 0 | |
Mechanical time constant | ms | 2.73 | 2.73 | 2.79 | 2.76 | 2.65 | 2.65 | 2.58 | |
Moment of inertia | gcm2 | 0.3 | 0.3 | 0.3 | 0.3 | 0.3 | 0.3 | 0.3 | |
Torque constant | mN.m/A | 5.78 | 5.78 | 8.28 | 6.4 | 9.96 | 11.69 | 14.27 | |
Speed constant | rpm/V | 1652 | 1652 | 1153 | 1493 | 958 | 843.5 | 820.9 | |
Speed/torque slope | rpm/mN.m | 868.6 | 868.6 | 888.7 | 877.7 | 844.7 | 254 | 232 | |
Motor weight | g | 32.6 | 32.6 | 32.6 | 32.6 | 32.6 | 32.6 | 32.6 |
Relevant information | |||||||
Thermal resistance of motor | 22.5 K/W | Thermal time constant of motor | 407 S | ||||
Dynamic load: axial | 1.5 N | Dynamic load: radial (5mm outside face) | 6.0 N | ||||
Maximum installation force (static) | 40 N | Maximum driving depth of mounting screw | 3.0 mm | ||||
Radial clearance (5mm outside face) | ≤0.02 mm | Axial clearance | 0 (<2.0N ) | ||||
Maximum coil temperature | 85ºC | Ambient temperature | -30 to 65ºC | ||||
Standard rear axle diameter | 2 mm | Standard rear axle length "L | 0/3.7/5.5 mm | ||||
Lead Definition (AWG 26#)) | Total length of gear motor: LT=L1+L2+L3 | BL1632AN Recommended combination option | |||||
Lead 1: yellow motor winding A | L1:16GP | L1:19GP | L2:BL16 | L3:EN16T | L3:EN16S | ||
Lead 2: Red motor winding B | 15.9 | 18.8 | 32 | 12 | 10.7 | ||
Lead 3: Blue motor winding C | 19.6 | 23.6 | |||||
Sensor Pin Definition (AWG 28#) Molex:51021-0500 | 23.3 | 28.4 | |||||
27 | 33.2 | ||||||
Pin 1: Brown Hall Vcc 3 to 16V | |||||||
Pin 2: Black Hall GND | Note: Customers can choose the corresponding gear box and encoder to match with the motor, more product combinations, please contact our sales staff. | Recommended gear box: 16GP 19GP 22GP | |||||
Pin 3: Yellow Hall A | |||||||
Pin 4: Red Hall B | |||||||
Pin 5: Blue Hall C | |||||||
The motor data was measured in a standard test environment of 25 ° C. Motor operation beyond the maximum recommended continuous parameters may result in reduced life or damage to the motor. In high temperature environments, the load current must be reduced to protect the motor. |
Brushless motor Ball bearing | ||||||||||
Model number | 1234 | 1221 | 1216 | 1836 | 1821 | 1816 | 2419 | 2413 | ||
Rated voltage | V | 12 | 12 | 12 | 18 | 18 | 18 | 24 | 24 | |
No-load speed ±12% | rpm | 34200 | 21000 | 16400 | 36300 | 20900 | 16160 | 19400 | 12600 | |
No-load current Max150% | mA | 200 | 120 | 80 | 150 | 75 | 60 | 50 | 40 | |
Recommended limit value for continuous operation | Maximum continuous torque | mN.m | 4.6 | 5.8 | 6.3 | 3.5 | 5.7 | 6.2 | 6.2 | 6.4 |
Rated speed | rpm | 31782 | 17888 | 13242 | 34513 | 17874 | 13027 | 16136 | 9133 | |
Maximum continuous current | mA | 1600 | 1200 | 1000 | 900 | 780 | 650 | 580 | 400 | |
Rated power | W | 15.5 | 10.9 | 8.8 | 12.7 | 10.7 | 8.4 | 10.4 | 6.1 | |
Starting current | mA | 20000 | 7407 | 4858 | 15385 | 4945 | 3103 | 3200 | 1348 | |
Locked-rotor moment | mN.m | 66 | 39 | 33 | 71 | 39 | 32 | 37 | 23 | |
Maximum output power | W | 58.8 | 21.5 | 14.1 | 67.9 | 21.6 | 13.4 | 18.6 | 7.6 | |
Maximum efficiency value | % | 81 | 76 | 76 | 81 | 77 | 74 | 77 | 69 | |
End resistance ±12% | Q | 0.6 | 1.62 | 2.47 | 1.17 | 3.64 | 5.8 | 7.5 | 17.8 | |
inductance (1KHZ) | mH | 0.032 | 0.1 | 0.16 | 0.08 | 0.24 | 0.38 | 0.49 | 1.05 | |
Mechanical time constant | ms | 2.2 | 2.3 | 2.1 | 2.2 | 2.3 | 2.2 | 2.3 | 2.3 | |
Moment of inertia | gcm² | 0.41 | 0.41 | 0.41 | 0.41 | 0.41 | 0.41 | 0.41 | 0.41 | |
Torque constant | mN.m/A | 3.3 | 5.4 | 6.9 | 4.7 | 104 | 11.6 | 17.6 | ||
Speed constant | rpm/N | 2879 | 1779 | 1390 | 2037 | 1179 | 915 | 821 | 541 | |
Speed/torque slope | rpm/mN.m | 520.7 | 536.8 | 499.4 | 508.2 | 529.8 | 509.0 | 529.6 | 545.7 | |
Motor weight | g | 42.2 | 42.1 | 41.8 | 42.1 | 42.2 | 41.8 | 41.9 | 41.8 |
Relevant information | |||||||
Thermal resistance of motor | 17.9KW | Thermal time constant of motor | 439S | ||||
Dynamic load: axial | 1.5N | Dynamic load: radial (5mm outside face) | 6.0N | ||||
Maximum installation force (static) | 40N | Maximum driving depth of mounting screw | 3.0mm | ||||
Radial clearance (5mm outside face) | ≤0.02mm | Axial clearance | 0(<2.0N) | ||||
Maximum coil temperature | 85℃ | Ambient temperature | -30to65℃ | ||||
Standard rear axle diameter | 2mm | Standard rear axle length "L | No mm | ||||
Lead Definition (AWG 26#)) | Total length of gear motor: LT=L1+L2+L3 | BL1640AN Recommended combination option | |||||
Lead 1: yellow motor winding A | L1:16GP | L1:19GP | L2:BL16 | L3:EN16S | L3:EN16T | ||
Lead 2: Red motor winding B | 15.9 | 18.8 | 40 | 10.7 | 12 | ||
Lead 3: Blue motor winding C | 19.6 | 23.6 | |||||
Sensor Pin Definition (AWG 28#) Molex:51021-0500 | 23.3 | 28.4 | |||||
27 | 33.2 | ||||||
Pin 1: Brown Hall Vcc 3 to 16V | |||||||
Pin 2: Black Hall GND | Note: Customers can choose the corresponding gear box and encoder to match with the motor, more product combinations, please contact our sales staff. | Recommended gear box: | |||||
Pin 3: Yellow Hall A | |||||||
Pin 4: Red Hall B | |||||||
Pin 5: Blue Hall C | |||||||
The motor data was measured in a standard test environment of 25 ° C. Motor operation beyond the maximum recommended continuous parameters may result in reduced life or damage to the motor. In high temperature environments, the load current must be reduced to protect the motor. |
Brushless motor Ball bearing | ||||||||
Model number | 1225 | 1220 | 1822 | 1819 | 2419 | 2415 | ||
Rated voltage | V | 12 | 12 | 18 | 18 | 24 | 24 | |
No-load speed ±12% | rpm | 24525 | 19908 | 22265 | 18634 | 19339 | 14850 | |
No-load current Max150% | mA | 200 | 200 | 120 | 100 | 90 | 70 | |
Recommended limit value for continuous operation | Maximum continuous torque | mN.m | 2.3 | 4.2 | 2.9 | 4.5 | 3.6 | 4.6 |
Rated speed | rpm | 23581 | 18096 | 21080 | 16679 | 17806 | 12731 | |
Maximum continuous current | mA | 700 | 900 | 500 | 600 | 400 | 380 | |
Rated power | W | 5.7 | 8 | 6.4 | 7.9 | 6.7 | 6.2 | |
Starting current | mA | 13187 | 8392 | 7258 | 4865 | 4000 | 2243 | |
Locked-rotor moment | mN.m | 60 | 47 | 54 | 43 | 45 | 32 | |
Maximum output power | W | 38.4 | 24.3 | 31.6 | 21 | 22.9 | 12.6 | |
Maximum efficiency value | % | 77 | 75 | 76 | 73 | 72 | 68 | |
End resistance ±12% | Ω | 0.91 | 1.43 | 2.48 | 3.7 | 6 | 10.7 | |
inductance (1KHZ) | mH | 0.07 | 0.11 | 0.19 | 0.29 | 0.47 | 0.86 | |
Mechanical time constant | ms | 3 | 3.1 | 3 | 3.1 | 3.1 | 3.3 | |
Moment of inertia | gcm2 | 0.69 | 0.69 | 0.69 | 0.69 | 0.69 | 0.69 | |
Torque constant | mN.m/A | 4.6 | 5.7 | 7.6 | 9 | 11.6 | 15 | |
Speed constant | rpm/V | 2075 | 1689 | 1258 | 1057 | 824 | 639 | |
Speed/torque slope | rpm/mN.m | 410.4 | 427.3 | 410.8 | 432.9 | 427 | 457.1 | |
Motor weight | g | 52 | 52 | 52 | 52 | 52 | 52 |
Relevant information | |||||||
Thermal resistance of motor | 22.8K/W | Thermal time constant of motor | 552S | ||||
Dynamic load: axial | 2.5 N | Dynamic load: radial (5mm outside face) | 16.0N | ||||
Maximum installation force (static) | 50 N | Maximum driving depth of mounting screw | 3.0mm | ||||
Radial clearance (5mm outside face) | ≤0.02 mm | Axial clearance | 0(<4.0N) | ||||
Maximum coil temperature | 85℃ | Ambient temperature | -30to65℃ | ||||
Standard rear axle diameter | 3mm | Standard rear axle length "L | 0/3.7/5.5 mm | ||||
Lead Definition (AWG 26#)) | Total length of gear motor: LT=L1+L2+L3 | BL2032AN Recommended combination option | |||||
Lead 1: yellow motor winding A | L1:19GP | L1:24GP | L2:BL20 | L3:EN16S | L3:EN16T | ||
Lead 2: Red motor winding B | 18.8 | 24 | 32 | 10.7 | 12 | ||
Lead 3: Blue motor winding C | 23.6 | 34.3 | |||||
Sensor Pin Definition (AWG 28#) Molex:51021-0500 | 28.4 | 42.8 | |||||
33.2 | 51.3 | ||||||
Pin 1: Brown Hall Vcc 3 to 16V | |||||||
Pin 2: Black Hall GND | Note: Customers can choose the corresponding gear box and encoder to match with the motor, more product combinations, please contact our sales staff. | Recommended gear box: | |||||
Pin 3: Yellow Hall A | |||||||
Pin 4: Red Hall B | |||||||
Pin 5: Blue Hall C | |||||||
The motor data was measured in a standard test environment of 25 ° C. Motor operation beyond the maximum recommended continuous parameters may result in reduced life or damage to the motor. In high temperature environments, the load current must be reduced to protect the motor. |
Brushless motor Ball bearing | |||||||||
Model number | 1226 | 1220 | 1216 | 1820 | 1817 | 2420 | 2417 | ||
Rated voltage | V | 12 | 12 | 12 | 18 | 18 | 24 | 24 | |
No-load speed ±12% | rpm | 26000 | 20360 | 16260 | 19500 | 17350 | 20000 | 16600 | |
No-load current Max150% | mA | 350 | 190 | 180 | 150 | 140 | 110 | 95 | |
Recommended limit value for continuous operation | Maximum continuous torque | mN.m | 5.4 | 7.3 | 8.5 | 7.4 | 6.4 | 6.7 | 7.5 |
Rated speed | rpm | 24682 | 18605 | 14445 | 17760 | 15721 | 18454 | 14905 | |
Maximum continuous current | mA | 1600 | 1500 | 1400 | 1000 | 800 | 700 | 650 | |
Rated power | W | 14 | 14.2 | 12.8 | 13.7 | 10.6 | 12.9 | 11.8 | |
Starting current | mA | 25000 | 15385 | 11111 | 9677 | 7171 | 7742 | 5530 | |
Locked-rotor moment | mN.m | 107 | 84 | 76 | 83 | 68 | 86 | 74 | |
Maximum output power | W | 72.9 | 45 | 32.3 | 42.2 | 31 | 45.1 | 32 | |
Maximum efficiency value | % | 78 | 79 | 76 | 77 | 74 | 78 | 76 | |
End resistance ±12% | Ω | 0.48 | 0.78 | 1.08 | 1.86 | 2.51 | 3.1 | 4.34 | |
inductance (1KHZ) | mH | 0.034 | 0.061 | 0.097 | 0.17 | 0.22 | 0.29 | 0.42 | |
Mechanical time constant | ms | 2.9 | 2.9 | 2.5 | 2.8 | 3 | 2.7 | 2.7 | |
Moment of inertia | gcm 2 | 1.13 | 1.13 | 1.13 | 1.13 | 1.13 | 1.13 | 1.13 | |
Torque constant | mN.m/A | 4.6 | 5.6 | 6.9 | 8.7 | 9.7 | 11.3 | 13.6 | |
Speed constant | rpm/V | 2197 | 1718 | 1377 | 1100 | 983 | 845 | 704 | |
Speed/torque slope | rpm/mN.m | 242.7 | 241.1 | 214.5 | 235.8 | 254 | 232 | 225.1 | |
Motor weight | g | 65.9 | 66.2 | 66.6 | 65.7 | 65.4 | 65.1 | 65.9 |
Relevant information | |||||||
Thermal resistance of motor | 15KW | Thermal time constant of motor | 673S | ||||
Dynamic load: axial | 2.5N | Dynamic load: radial (5mm outside face) | 16.0N | ||||
Maximum installation force (static) | 50N | Maximum driving depth of mounting screw | 3.0mm | ||||
Radial clearance (5mm outside face) | ≤0.02mm | Axial clearance | 0(<4.0N) | ||||
Maximum coil temperature | 85℃ | Ambient temperature | -30to65℃ | ||||
Standard rear axle diameter | 3mm | Standard rear axle length "L | 0/3.7/5.5 mm | ||||
Lead Definition (AWG 26#)) | Total length of gear motor: LT=L1+L2+L3 | BL2040AN Recommended combination option | |||||
Lead 1: yellow motor winding A | L1:19GP | L1:24GP | L1:24GP | L2:BL20 | L3:EN16T | ||
Lead 2: Red motor winding B | 18.8 | 24 | 24 | 40 | 12 | ||
Lead 3: Blue motor winding C | 23.6 | 34.3 | 34.3 | ||||
Sensor Pin Definition (AWG 28#) Molex:51021-0500 | 28.4 | 42.8 | 42.8 | ||||
33.2 | 51.3 | 51.3 | |||||
Pin 1: Brown Hall Vcc 3 to 16V | |||||||
Pin 2: Black Hall GND | Note: Customers can choose the corresponding gear box and encoder to match with the motor, more product combinations, please contact our sales staff. | Recommended gear box: | |||||
Pin 3: Yellow Hall A | |||||||
Pin 4: Red Hall B | |||||||
Pin 5: Blue Hall C | |||||||
The motor data was measured in a standard test environment of 25 ° C. Motor operation beyond the maximum recommended continuous parameters may result in reduced life or damage to the motor. In high temperature environments, the load current must be reduced to protect the motor. |
Application
Robot DC brushless hollow cup motor with its unique advantages is widely used in many fields. In the field of service robots, used for indoor cleaning robots, lightweight body with efficient power, flexible shuttle between furniture cleaning; In the medical field, help surgical auxiliary robots to accurately operate instruments to ensure surgical safety; In industrial scenarios, it can be used for small assembly robots to respond quickly to complete precision assembly tasks; In terms of education and entertainment, it endows intelligent toy robots with smart actions and brings interesting interactive experience; In logistics warehousing, the sorting robot can be quickly started and stopped to efficiently sort goods.
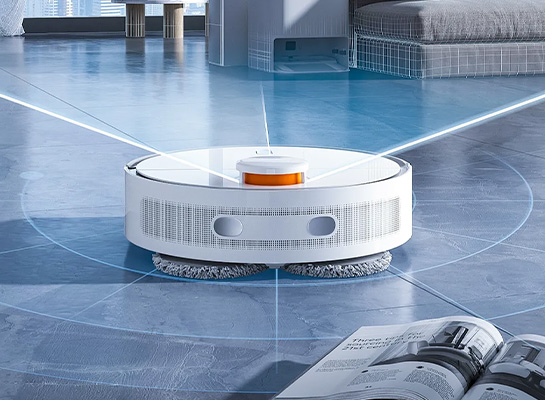
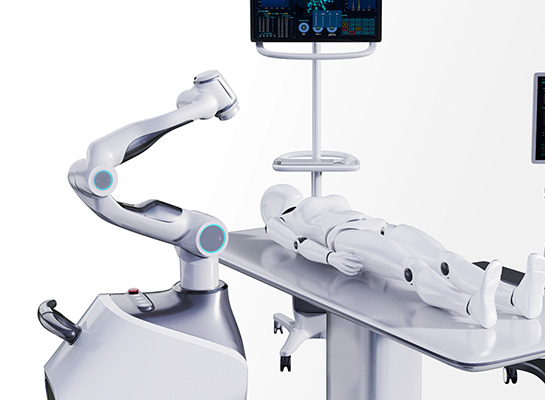
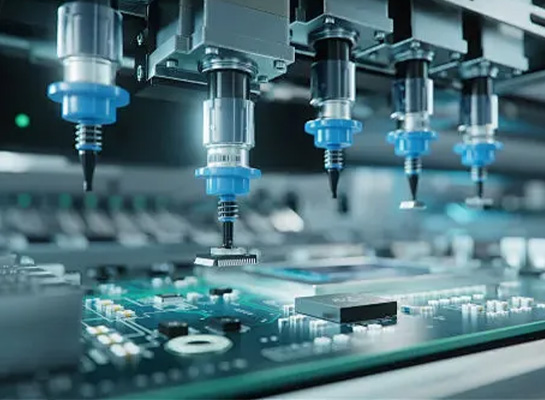
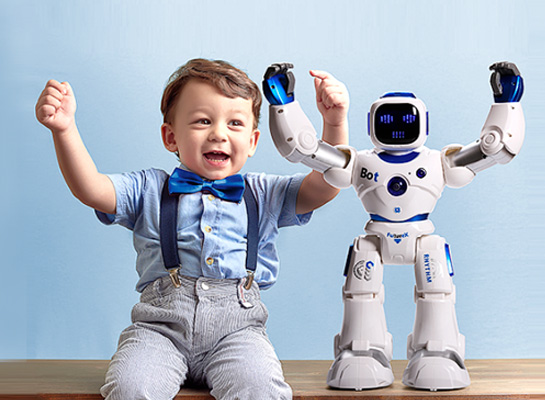