Product Description
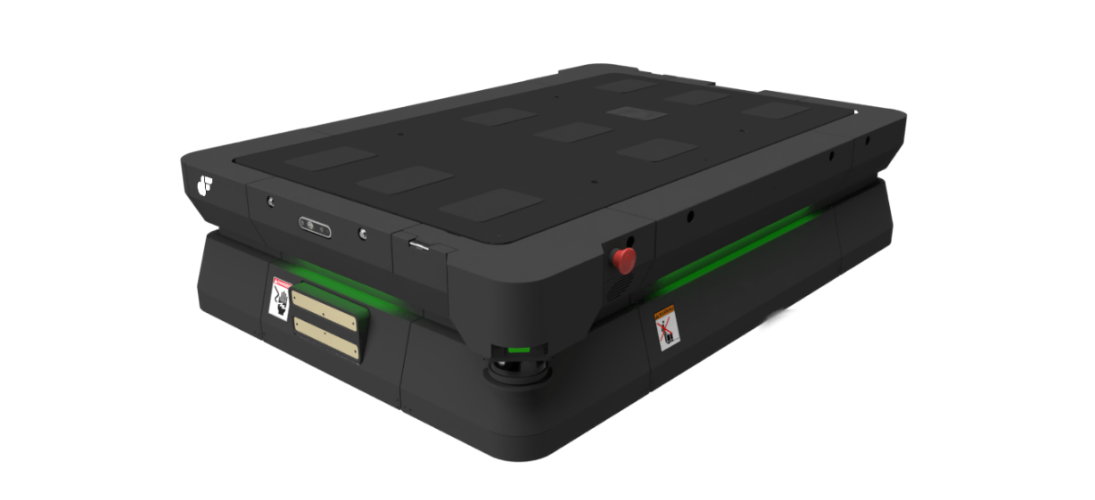
The Titan Series AMR is our flagship Autonomous Mobile Robot a premium solution for businesses looking to improve their operations with advanced automation. Boasting the highest payload capacity among our product line thus making it an ideal fit for industries that require heavy-duty automation, such as manufacturing and distribution.
Our AMR includes premium features such as advanced built-in safety sensors and rugged design, ensuring it can operate in demanding environments with ease. Our technology allows the AMR to independently navigate through complex layouts, minimizing the need for human intervention, and reducing the risk of equipment damage and employee injury.
Customize the AMR by equiping Titan AMR with pallet lifting module to cater for your unique facility specifications and business needs.
Highlights:
Brushless motor integration for a higher overall performances.
Cleaner and more compact internal layout for ease of maintenance.
Safety grade laser sensor for better performances and relibility.
Up to 4.3 degree of graedibility.
High payload up to 1.5 Tonne.
Product Features
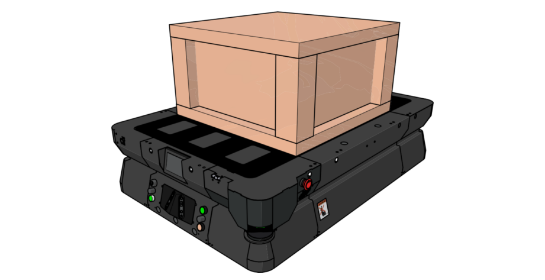
1 | High Payload
High payload capacity (Up to 1.5 Tonne) for heavy-duty automation
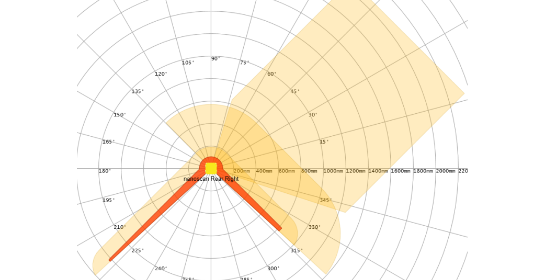
2 | Safety
Equipped with redundant safety features such as laser sensor, bumper, emergency button.
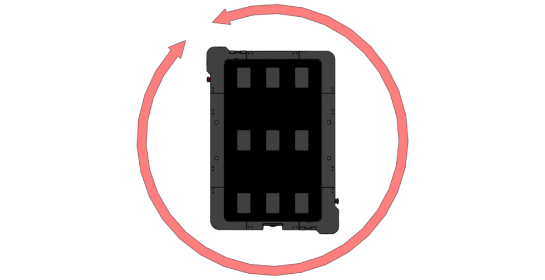
3 | Differential Driven
Zero turning radius.
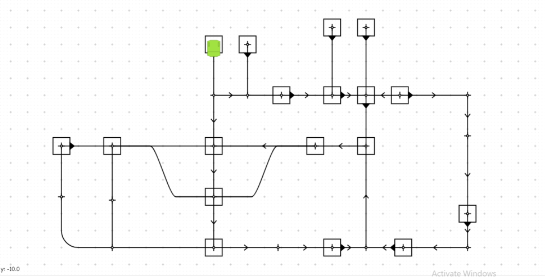
4 | NavWiz Map
Allows user to draw and plan topological map for Titan
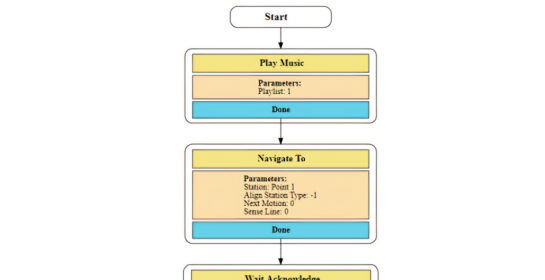
5 | NavWiz Task
Titan programming software using simple flowchart system.
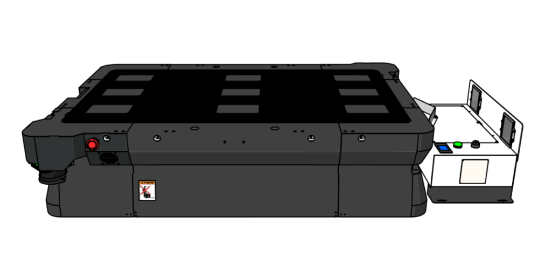
6 | Auto Charging
Automatically charges itself to ensure 24-hour continuous operation.
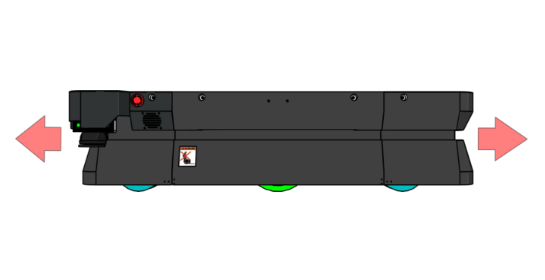
7 | Bi-Directional
Able to move both forward and reverse.
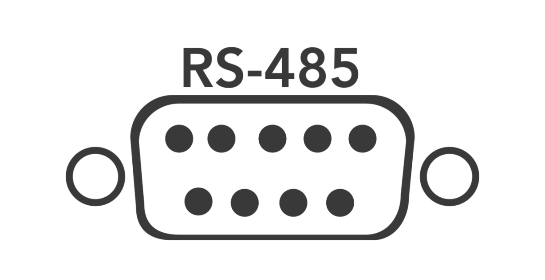
8 | RS-485 Interface
More flexible integartion with RS-485 interface
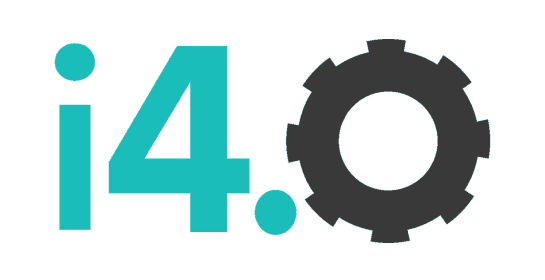
9 | Internet of Thing
Titan is IoT – enabled to meet industry 4.0 requirements.
Product parameters
DIMENSION | |
Length | 1360 mm |
Width | 960 mm |
Height | 330 mm |
Clearance from Ground | 30 mm |
Load Surface | Length: 1360 mm, Width: 960 mm |
Driving Wheel | Diameter: 225 mm, Width: 45 mm |
Wheel-to-wheel Distance | 700 mm |
Caster Wheel | Diameter: 150 mm, Width: 108 mm |
PAYLOAD | |
Carry Payload | 1500 kg l For load directly placed on robot |
APPLICABLE PALLETS | |
Pallet Type | Double deck Reversible Non-reversible Two-way entry Four-way entry Partial four-way Overlap Cruciform perimeter-base Single-wing Double-wing l According to ISO 445:2013, ISO 6780 |
Pallet Dimension | 1200 (L) x 800 (W) 1200 (L) x 1000 (W) 1219 (L) x 1016 (W) 1067 (L) x 1067 (W) 1100 (L) x 1100 (W) 1140 (L) x 1140 (W) l All standard pallets dimension in ISO 6780:2003 |
PERFORMANCE | |
Maximum Speed | 1 m/s (3.6 km/h) l With rated payload l Travelling max speed with rated payload (on site) is recommended to undergo Risk Assessment as welll 2 m/s (7,2 km/h) l Without payload |
Acceleration | 0.25 m/s^2 l With rated payload l Travelling max speed with rated payload (on site) is recommended to undergo Risk Assessment as well |
Stopping Accuracy | Natural Feature: ±100mm, ±2° Marker: ±50mm, ±1° l Speed before stopping: 0.13 m/s (8 m/min) |
Maximum Gradeability | 7.5% / 4.3° l Permissible ramp is to ensure safety, although robot might be able to climb ramp with more than stated value, but doing so will jeopardize robot’s safety compliance l Should not be regarded as normal use |
DRIVING AND NAVIGATION | |
Driving System | 2-Wheel Differential Drive |
Suspension | Bogie (Passive) |
Navigation System | Laser-based Natural Feature Navigation (With Marker/Magnetic Strip Guidance For Precision) |
Minimum Turning Radius | 0 mm |
Navigation Direction | Forward, Reverse, Turning around centre of two driving wheels |
Minimum Width for Pivoting | 1620 mm l Rotate around centre of robot |
Minimum Aisle Width | 2620 mm |
Minimum Safety Clearance of Width | 500 mm l Based on ISO 3691-4:2020 l On both sides of robot |
Minimum Safety Clearance of Height | 2100 mm l Based on ISO 3691-4:2020 l On both sides of robot |
Motor Type | DC Brushless Motor with Closed Loop Speed Control |
Brake | Navigation: Dynamic Brake Parking & Emergency Stop: Electromechanical Brake |
POWER | |
Running Time (100% to 10%) | 12 hours l With rated payload |
Charging Time (10% to 100%) | 3 hours |
Charging Time : Running Time Ratio | 1:4 l With rated payload |
Charging Method | Manual Charge: Through cable (Safety brake will be triggered) Auto Charge: Dock charging through charging station |
Battery Capacity | 64 Ah |
Battery Voltage | 48 V |
Battery Type | LiFePO4 |
Battery Weight | 32±2 kg |
SAFETY | |
Emergency Switch | 2 Units |
Protective Devices | 3D Camera (Front Facing) x 2 units 3D Camera (Rear Facing) x 1 unit Safety Laser Scanner x 2 units MOC (Motion Safety) |
External Safety I/Os | 1 Input, 1 Output |
Indicator | Speakers 360° RGB LED lighting |
INTERFACE | |
Language | English |
Operating System | NavWiz |
User Interface | Physical Buttons 5″, 800×400 pixels, Capacitive Touchscreen |
Additional I/Os | General USB port: 1 Digital I/O : 4 Input, 4 Output Modbus TCP supported LAN: 1 |
CONTROL SYSTEM | |
Central Control System | IPC intel i5 |
Communications | 802.11 a/b/g/n, 2.4GHz / 5GHz WiFi Open WiFi WPA & WPA2 Personal WPA & WPA2 Enterprise |
LIFTING SYSTEM | |
Lifting Height | 80 mm |
Lifting Payload | 1500 kg l For load directly placed on robot. |
Lifting Speed (0-100%) | 7 s |
Sensing | Inductive Sensor |
ENVIRONMENT | |
Ambient Temperature Range | 5 ~ 44°C |
Humidity | 10 ~ 95% l @ 40°C (non-condensing) |
Operating Environment | Indoor usage with no excessive dust or corrosive gases |
Floor Requirement | Level surface or concrete l no water, no oil, no dirt |
IP Class | IP20 |
Floor Flatness | FF25 l Based on ACI 117 standard, it is the American Concrete Institue Standard for concrete floor. FF is flatness, FL is the level. The higher FF numbers represent flatter floors. |