Product Description
Stable at low speed Low noise High precision
Strong carrying capacity Precise control Easy to operate
Product Highlights:
The ER Series Integrated Direct-Drive Joint Modules are designed for collaborative robots, service robots, AGVs, and precision automation systems. Featuring a compact size, lightweight design, fast dynamic response, and high torque output, these joint modules are ideal for next-generation robotic applications. Each unit is equipped with a high-resolution 17-bit encoder, achieving control precision of less than 0.01° per step. The hollow shaft structure allows for easy internal wiring and system integration.
Performance & Technical Advantages:
The ER Series supports multiple communication interfaces such as CAN bus, and integrates a patented communication protocol developed in-house, ensuring high-speed and efficient control. All core components, including the motor and encoder, are manufactured in our own facility, enabling fast technical support and quality assurance. Compared to similar products on the market, the ER Series delivers superior size reduction, weight optimization, and precision motion control, making it a standout solution for smart robotic joints.
Application
The ER Series Integrated Joint Modules are widely used in humanoid robots, robotic arms, exoskeletons, quadruped robots, AGV smart transport systems, and educational & research robots. With a highly integrated structure, hollow shaft design, and precision motion control, the ER series provides powerful support for multi-DOF systems, serving as the core drive unit that enables agile motion and efficient execution in intelligent robotics.
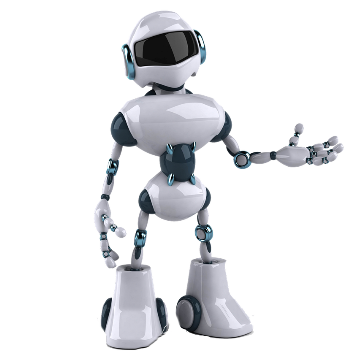
Humanoid Robots
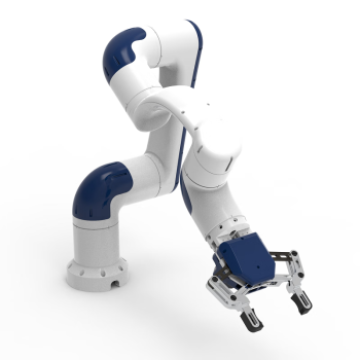
Robotic Arm
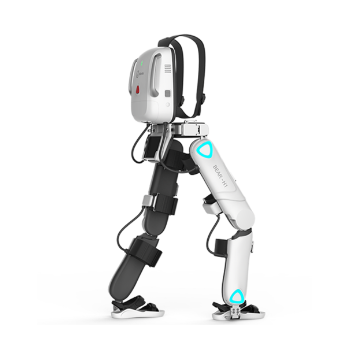
Exoskeleton Robots
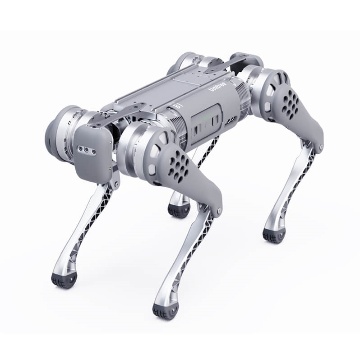
Quadruped Robots
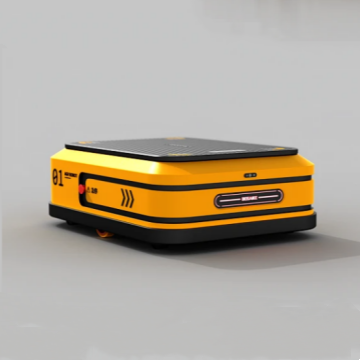
AGV Smart Truck
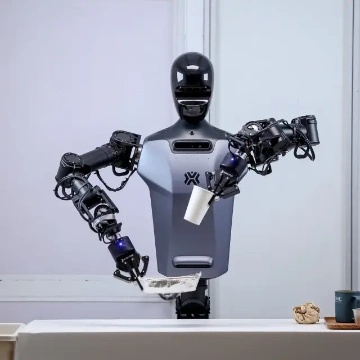
Educational & Research Robots
Choosing the EH series joint module means choosing efficient development, reliable performance and broad adaptability. We are committed to providing more intelligent and flexible motion control solutions for global developers, integrators and end users to help your robot products quickly achieve a leap from conception to implementation.
Product parameters
The following is a selection introduction of this series of products for your reference:
① ER Stands For The Series Name: Integrated Hollow Direct Drive Robot Joint Module
② 70 Represent Motor Model Number e.g:50/70/90 etc
③ Stator stack height 15
④ Motor power 200
⑤ Communication C:CANbus E:Ethercat
For example:
Model ER-90-15-400-C
illustrate EHS:Integrated Hollow Direct Drive Robot Joint Module 90:Motor Model Number
15:Stator stack height 400:Motor power C:Communication C:CAN BUS
Parameters | ER-50-15 | ER-70-15 | ER-90-15 |
Outside diameter(mm) | 50 | 70 | 90 |
Input Voltage(V) | 24 | 48 | 48 |
No Load Speed(RPM) | 3200 | 2800 | 2000 |
No Load Current(A) | 0.4 | 0.18 | 0.35 |
Rated Speed(RPM) | 2500 | 2400 | 1600 |
Rated Torque(N.m) | 0.35 | 0.8 | 1.5 |
Rated Power(W) | 91.6 | 200 | 252 |
Rated Current(A) | 4.9 | 4.4 | 6.6 |
Peak Torque(N.m) | 0.9 | 2 | 3.75 |
Peak Current(A) | 12.4 | 13.2 | 19.8 |
Efficiency(%) | >83% | >84% | >83% |
Back-EMF Constant(Vdc/Krpm) | 7.93 | 17 | 21.1 |
Torque Constant(N.m/A) | 0.07 | 0.18 | 0.23 |
Phase Resistance(Ω) | 0.4 | 0.5 | 0.35 |
Phase Inductance(mH) | 0.19 | 0.55 | 0.28 |
Pole Pair | 13 | 13 | 16 |
Cogging Torque(mN.m) | 12 | 30.83 | 64 |
Phase Connection3 | Y | Y | Y |
Max Axial Payload(N) | 489 | 1870 | 2350 |
Max Radial Payload(N) | 100 | 440 | 770 |
Inertia(Kg.m2) | 0.005 | 0.01 | 0.05 |
Encoder Type&Interface | ABS-17bit | ABS-17bit | ABS-17bit |
Repeat Position Accuracy(Degree) | <0.01 | <0.01 | <0.01 |
Communication | CAN | CAN | CAN |
Weight(Kg) | 0.24 | 0.47 | 0.71 |
Insulation grade | F | F | F |
Dimensional Installation Drawing
ER-50-15-100-C
ER-70-15-200-C
ER-90-15-400-C
FAQ
Q1: What communication protocols are supported by the ER Series?
A1: The ER Series currently supports CANBUS only, which offers stable and real-time communication for multi-node robotic systems.
Q2: Is EtherCAT or other protocols supported?
A2: Currently, EtherCAT, Modbus, and RS485 are not supported. For customized protocol integration, please contact us for evaluation.
Q3: What types of robots are suitable for the ER Series?
A3: The ER Series is ideal for humanoid robots, robotic arms, quadruped robots, exoskeletons, AGV systems, and educational or research platforms, especially where compact size, low weight, and high precision are required.
Q4: What is the encoder resolution?
A4: The ER Series uses a 17-bit high-resolution encoder, providing control precision better than 0.01° per step.
Q5: Does the product support hollow shaft wiring?
A5: Yes, the ER Series features a hollow shaft structure, allowing easy internal wiring and sensor integration.
Q6: Is there an SDK or sample code available?
A6: We provide a CANBUS protocol manual and sample source code to help users quickly develop and integrate the module.