Product Description
The ERGG series dual-gripping electric gripper integrates drive and control, and has the advantages of high precision, high stability and flexibility. It is designed for small precision handling applications. The product has an effective clamping stroke of 0-26mm, a clamping force range of 10-25N, a recommended load of up to 1kg, and noise during operation is less than 40dB, which is suitable for production environments with high requirements for quietness.
It is powered by a 24V power supply, with a rated current of 1A and a maximum current of 2A to ensure stable operation. The gripper body supports three-sided installation (top, bottom, back), and is equipped with a double gripping component that can rotate 180°, supports independent control of the gripper, and significantly improves flexibility and adaptability.
The product protection level is IP40, which is suitable for a variety of automated operation scenarios such as 3C electronic product assembly, material handling, and precision component transportation. It can also be customized according to the specific needs of customers to meet the requirements of changing and complex industrial sites.
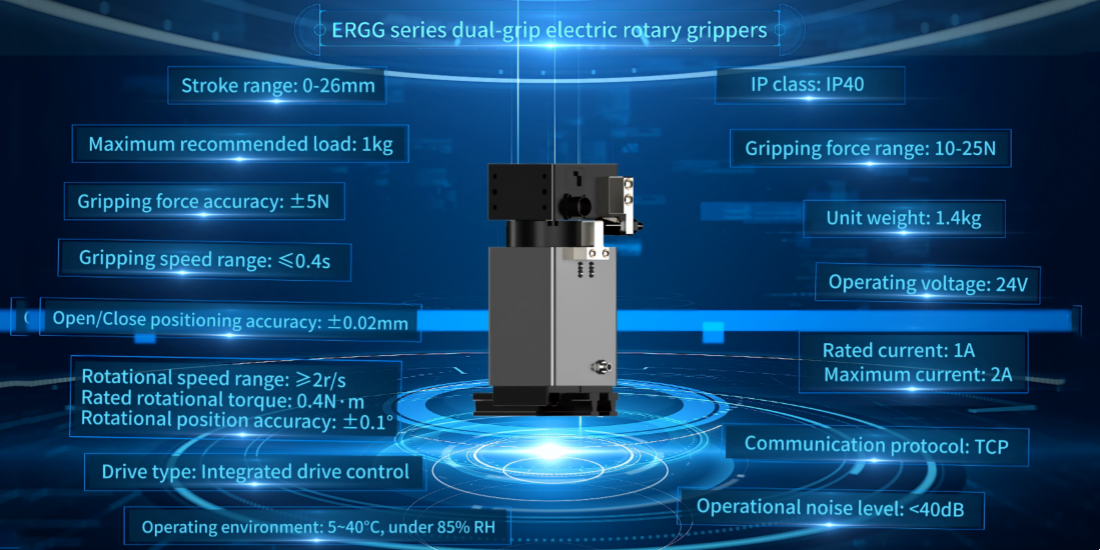
Industry Applications
As the global manufacturing industry moves towards the era of high-end intelligence, enterprises are increasingly demanding automation, informatization, intelligence and energy conservation. Faced with the continuous evolution of the industry, precision motion control and intelligent assembly with high efficiency and economy are gradually becoming the key direction to promote the development of intelligent manufacturing.
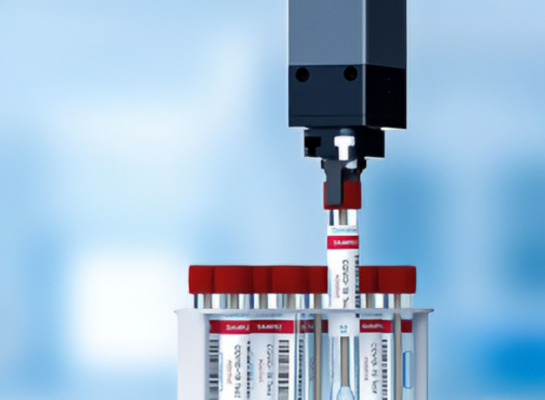
Medical Automation Industry
Our products have successfully served dozens of benchmark customers in the field of life sciences, especially in in vitro diagnostics (IVD) and laboratory automation equipment. The independently developed micro-drive-controlled integrated electric gripper and rotary clamping integrated electric servo gripper have been used in many detection automation equipment. Its compact integrated structure greatly simplifies the complex integrated design of traditional clamping systems, and it also has functions such as drop detection, grasping feedback, and power-off self-locking, which significantly improves the intelligence level of the equipment.
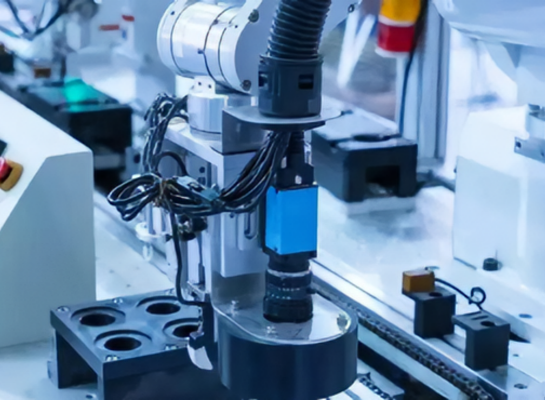
Automation Equipment
With the rapid development of automation equipment in the new energy industry, the demand for lithium battery automation equipment continues to grow, especially in the production of power battery PACK, which involves multiple robot loading and unloading links. We have a deep insight into the industry's needs and pain points, and launched a number of electric grippers customized for the new energy field, which have adjustable and controllable torque, speed and position control capabilities, and integrate power-off self-locking, ultra-long stroke, drop detection, grasping feedback and other functions, support three-sided installation, meet the diverse equipment integration needs, and are easy and reliable to use.
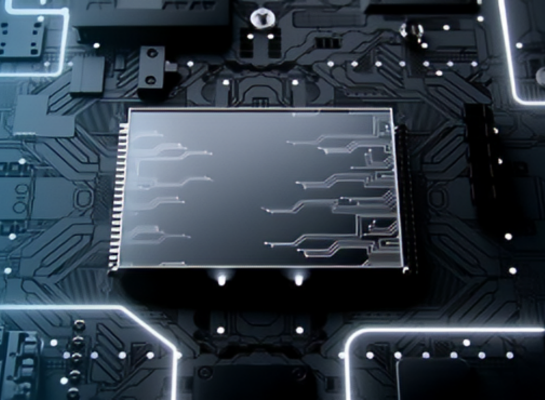
3C Industry
Aiming at the application scenarios in the 3C industry that have extremely high requirements on the appearance of parts, we have specially designed and developed electric grippers suitable for gripping irregular parts. They have the advantages of high frequency response and high precision control, helping customers to complete the assembly and handling of precision parts efficiently and safely.
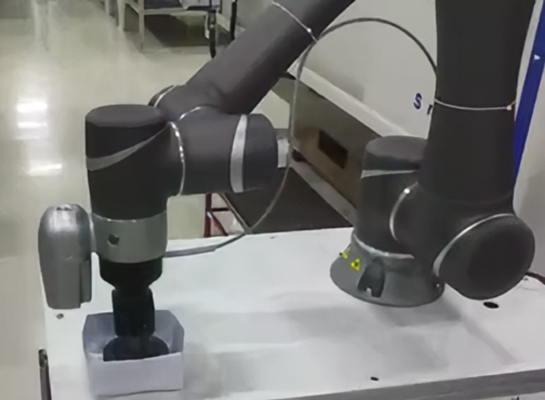
Robotics Industry
The RG series electric grippers are designed for robot applications. They are industrial, beautiful and durable, with a protection level of up to IP75, and are compatible with mainstream robot arm brands on the market, such as Siling, Aobo, Fao, etc. After multiple rounds of technical polishing and customer verification, this series of products has now become a mature and stable core product in the field of robotics.
Installation Dimensions
ERGG26-30-L5000-EC-N-A-P40-C01
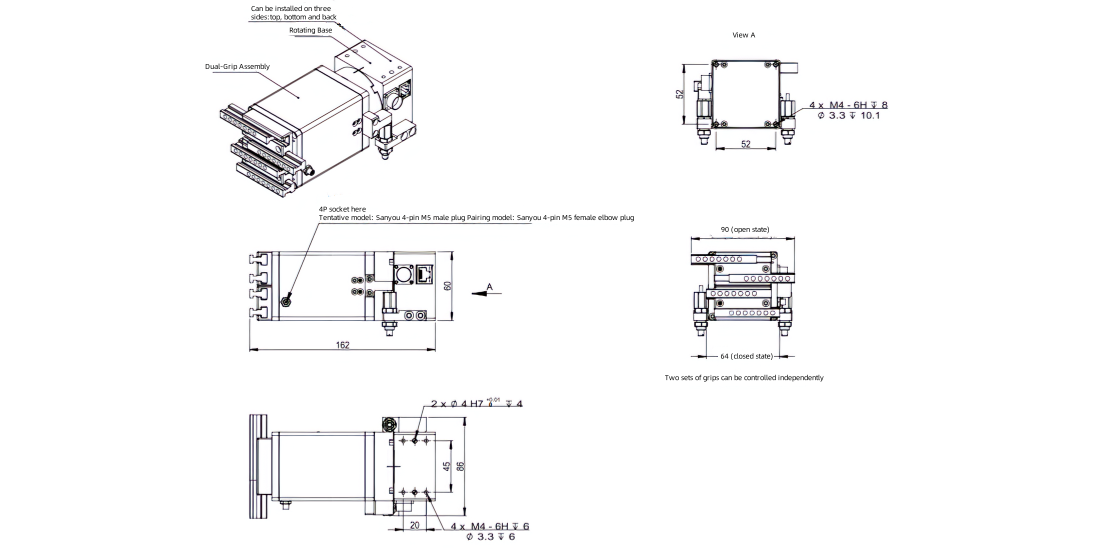
Product parameters
Model | ERGG26-30-L5000-EC-N-A-P40-C01 |
Adjustable stroke | 0-26mm |
IP level | IP40 |
Maximum recommended load | 1kg |
Gripping force | 10-25N |
Gripping force accuracy | ±5N |
Deadweight | 1.4kg |
Gripping speed range | ≤0.4s |
Rated voltage | 24V |
Position repeatability | ±0.02mm |
Rated current | 1A |
Rotation speed range | ≥2r/s |
Maximum current | 2A |
Rotational rated torque | 0.4N·m |
Communication protocol | TCP |
Rotation repeatability | ±0.1° |
Running noise | <40dB |
Drive type | Drive and control integrated |
Working environment | 5~40℃,below 85% RH |
Note: This product does not include finger clips, please contact us if you need them.
Robot Gripper Selection Steps
1、Confirmation of working conditions and uses According to the working conditions and uses, confirm the required actuator type or combination scheme. Examples of working conditions and uses include: workpiece transfer and assembly, workpiece correction and positioning, workpiece inner diameter/outer diameter measurement, etc. For high-precision applications such as correction and positioning, measurement, it is recommended to use product models with the word "HP". | |
2、Determine the maximum robot gripping force required Confirmation of gripping force : The weight of the workpiece that the clamp can hold is related to the friction coefficient of the fixture. To ensure smooth clamping, it is generally recommended that the clamping force be 10 times or more of the workpiece's own weight. For example: when the friction coefficient is 0.2, assuming the workpiece weighs 1kg, the required clamping force is approximately 100N or more. When the clamped workpiece is subject to large acceleration, deceleration or impact force when moving, it is necessary to select an actuator with greater output. Please consult your local sales representative for details. Note: The clamping force described in the product manual is based on the result at 30mm from the palm height; changes in the clamping position may cause changes in the actual clamping force. Please contact the sales staff for assistance in selection. | |
3、Confirm the installation method Actuators generally have multiple installation methods, and different installation methods will affect their maximum load mass value. At the same time, to ensure that the actuator can operate normally, please refer to the product selection manual before selecting the model to determine whether the dynamic load torque of the product is within the parameter range under the required installation method. | |
4、Confirm the stroke & speed Confirm the maximum movement distance range required for the working conditions, as well as the speed/beat requirements. Stroke: When selecting, the rated stroke of the actuator should be greater than the actual movement distance. Stroke = maximum clamping workpiece diameter (H1) - minimum clamping workpiece diameter (H2) (for a variety of clamping workpieces); Small-stroke clamps can clamp large-diameter workpieces by replacing the clamp design. Speed: Please check the opening/closing time of the clamp (the time described in the manual is the movement time of the full stroke). | |
5、Confirm the dynamic load operating torque Users can design and customize the fixture according to the actual application scenario, the size and shape of the clamped workpiece, etc. When designing the fixture, it is necessary to pay attention to the allowable torque value of the electric gripper (Mx/My/Mz=Fx*Sx/Fy*Sy/Fz*Sz) to avoid the fixture exceeding the maximum load allowable force, otherwise it will affect the mechanical life. | |
6、Confirm the control method Please select the required control method according to actual needs, refer to the detailed product model selection list. | |
7、Other requirements If the working conditions have special requirements for working voltage, ambient temperature, ambient humidity, safety protection level, etc., please check the corresponding product selection page or contact us. |
FAQ
1. What industries is the ERGG series suitable for?
The ERGG series is widely used in medical devices, 3C electronics, new energy, semiconductors, and robotics. It is ideal for precision part handling, assembly, and automated inspection.
2. What is the maximum stroke range of the gripper?
The gripping stroke is 0–26mm, suitable for precise handling of small components.
3. What is the recommended maximum payload?
The maximum recommended load is 1kg, ideal for lightweight parts.
4. Is customization supported?
Yes. We offer customization options based on your application needs, including gripping force, structure, and mounting configurations.
5. Can each finger be controlled independently?
Yes, the ERGG series supports independent control of each finger for advanced and flexible gripping strategies.
6. What are the electrical specifications?
Operating voltage is 24V DC, with a rated current of 1A and a maximum current of 2A.
7. What mounting options are available?
Three-sided mounting is supported—top, bottom, and back—for flexible integration with various equipment.
8. What smart features does the gripper offer?
Features include power-off self-locking, drop detection, and grip feedback, enhancing system safety and reliability.
9. What is the IP protection rating?
The gripper has an IP40 rating, suitable for indoor equipment integration.
10. Is it suitable for noise-sensitive environments like laboratories?
Yes. The operating noise is below 40dB, making it ideal for quiet environments such as labs or medical equipment setups.